Brazing and soldering are both metal-joining processes, but they differ significantly in terms of temperature, filler materials, and the resulting joint strength. The flux used in these processes also varies due to the differences in temperature and materials. Brazing flux is designed to withstand higher temperatures (above 450°C) and is formulated to work with stronger filler metals, while soldering flux operates at lower temperatures (below 450°C) and is tailored for softer filler materials. Understanding these differences is crucial for selecting the appropriate flux and achieving optimal results in metal-joining applications.
Key Points Explained:
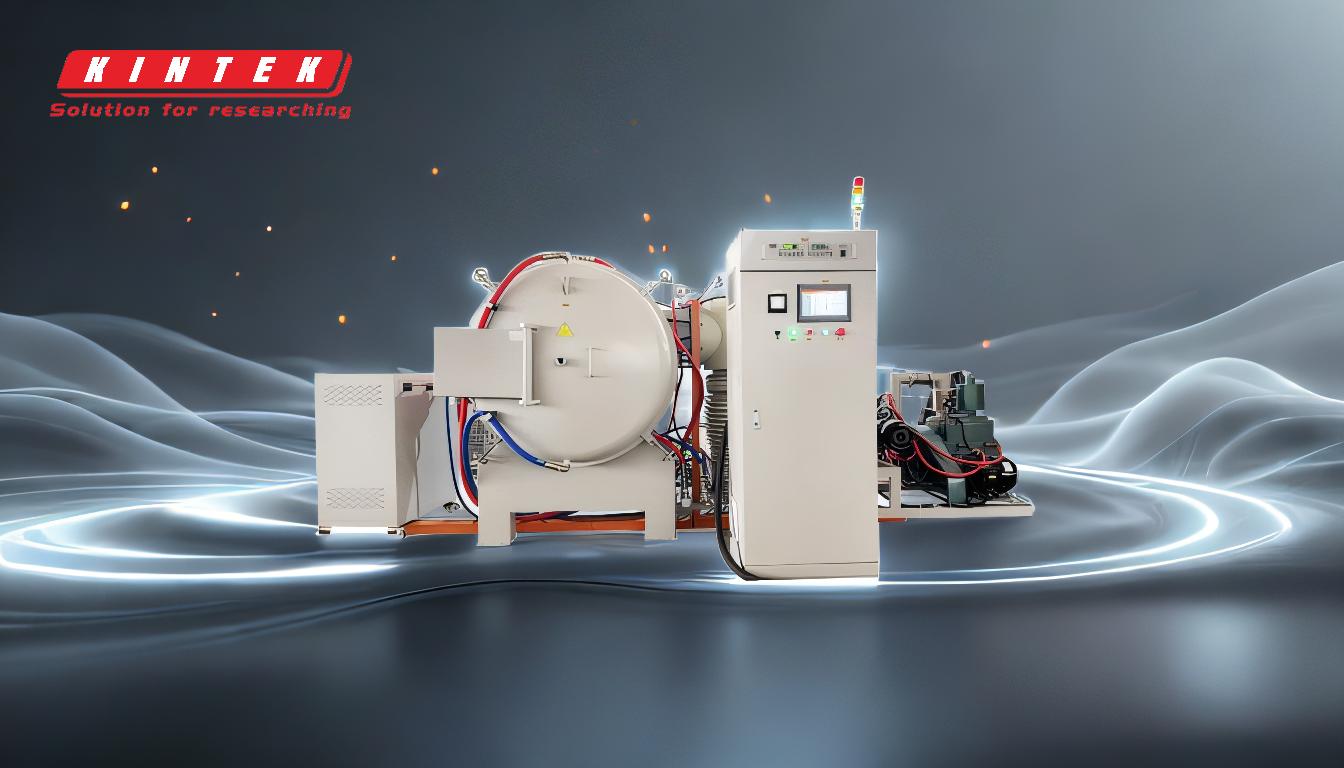
-
Temperature Differences
- Brazing: Occurs at temperatures above 450°C (840°F). The higher temperatures require a flux that can remain stable and active at these levels without breaking down or evaporating.
- Soldering: Takes place at temperatures below 450°C. The flux used here is designed to work effectively at lower temperatures and is less heat-resistant than brazing flux.
-
Filler Material Compatibility
- Brazing: Uses stronger filler metals like brass, bronze, or silver alloys. These materials require a flux that can remove oxides and impurities at high temperatures to ensure a strong bond.
- Soldering: Employs softer filler metals such as tin-lead or lead-free alloys. The flux must be compatible with these materials and capable of promoting wetting and capillary action at lower temperatures.
-
Flux Composition and Function
- Brazing Flux: Typically contains borax, boric acid, or fluorides, which are effective at high temperatures. These compounds help dissolve oxides and prevent re-oxidation during the brazing process.
- Soldering Flux: Often made from rosin, organic acids, or inorganic acids. These are formulated to clean the metal surfaces and improve the flow of the filler material at lower temperatures.
-
Joint Strength and Application
- Brazing: Produces joints with higher strength and durability, making it suitable for applications requiring robust connections, such as in HVAC systems or automotive components.
- Soldering: Creates joints that are less strong but sufficient for electrical connections, plumbing, or delicate assemblies where high strength is not a primary concern.
-
Practical Considerations
- Brazing Flux: Must be carefully selected to match the filler metal and base materials. It often requires post-braze cleaning to remove residual flux, which can be corrosive.
- Soldering Flux: Easier to handle and clean, but care must be taken to avoid flux residues that could cause electrical conductivity issues or corrosion in sensitive applications.
By understanding these key differences, you can choose the appropriate flux for your specific metal-joining task, ensuring a strong, reliable, and durable joint.
Summary Table:
Aspect | Brazing Flux | Soldering Flux |
---|---|---|
Temperature Range | Above 450°C (840°F) | Below 450°C |
Filler Materials | Stronger metals like brass, bronze, or silver alloys | Softer metals like tin-lead or lead-free alloys |
Flux Composition | Borax, boric acid, or fluorides for high-temperature stability | Rosin, organic acids, or inorganic acids for lower-temperature effectiveness |
Joint Strength | Higher strength, suitable for robust applications (e.g., HVAC, automotive) | Lower strength, ideal for electrical connections or delicate assemblies |
Practical Considerations | Requires post-braze cleaning to remove corrosive residues | Easier to handle, but residues may cause conductivity issues or corrosion |
Need help choosing the right flux for your metal-joining project? Contact our experts today for personalized advice!