Induction brazing and furnace brazing are both widely used metal joining processes, each with its own set of advantages and limitations. The choice between the two depends on specific application requirements, production scale, material types, and desired outcomes. Furnace brazing is particularly advantageous for mass production, complex designs, and joining dissimilar materials, offering consistent temperature control, minimal distortion, and clean joints without secondary finishing. Induction brazing, on the other hand, is typically faster, more localized, and energy-efficient, making it suitable for smaller-scale production or applications requiring precise heat application. Below, we explore the key differences and considerations to determine which method might be better for a given scenario.
Key Points Explained:
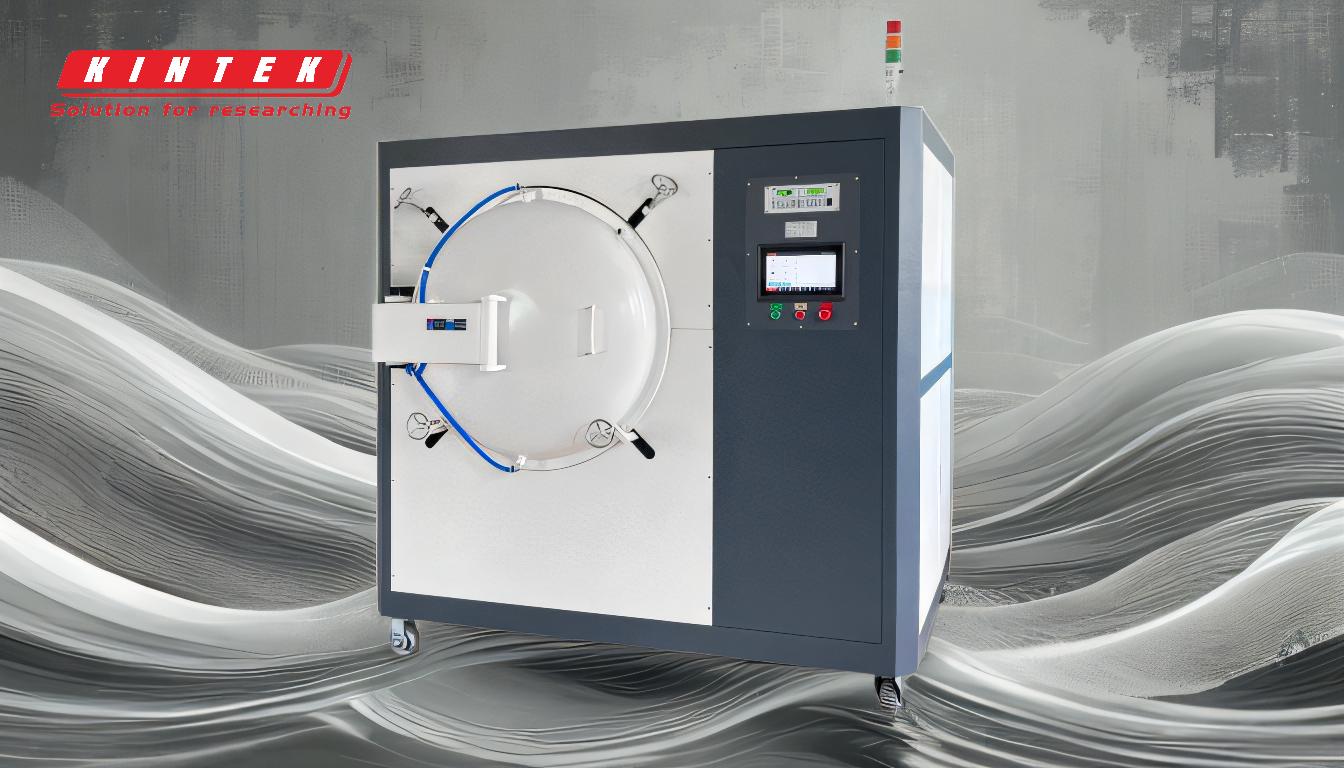
-
Production Scale and Automation
- Furnace Brazing: Ideal for mass production due to its ability to handle multiple joints simultaneously. It is easily automated, making it cost-effective for large-scale manufacturing.
- Induction Brazing: Better suited for smaller production runs or custom jobs where localized heating is required. It is less efficient for mass production but offers greater flexibility for unique or complex assemblies.
-
Material Compatibility
- Furnace Brazing: Excels at joining dissimilar materials, including unweldable and non-metallic components. It provides a clean atmosphere, reducing the need for fluxes and post-braze cleaning.
- Induction Brazing: Works well with metals that respond to electromagnetic induction, such as ferrous materials. It may struggle with non-conductive or dissimilar materials unless specialized techniques are used.
-
Temperature Control and Uniformity
- Furnace Brazing: Offers precise and uniform heating, minimizing thermal distortion and ensuring consistent joint quality. It allows for step brazing and combining heat treatments like annealing.
- Induction Brazing: Provides localized heating, which reduces heat-affected zones and energy consumption. However, achieving uniform heating across large or complex assemblies can be challenging.
-
Cost and Efficiency
- Furnace Brazing: More cost-effective for high-volume production due to lower operator skill requirements and faster lead times. It also reduces the need for secondary finishing, saving time and resources.
- Induction Brazing: While energy-efficient, it may require more skilled operators and setup time, making it less economical for large-scale production.
-
Joint Quality and Strength
- Furnace Brazing: Produces high-integrity joints with greater tensile strength, tighter tolerances, and cleaner surfaces. It is ideal for high-precision assemblies.
- Induction Brazing: Can achieve strong joints but may require more careful control to avoid defects like overheating or incomplete bonding.
-
Flexibility and Versatility
- Furnace Brazing: Highly versatile, capable of joining simple or complex designs with multiple joints in a single operation. It can also integrate additional heat treatments.
- Induction Brazing: Offers flexibility in terms of localized heating and quick setup but is less versatile for large or intricate assemblies.
In conclusion, furnace brazing is generally better for high-volume production, complex assemblies, and joining dissimilar materials, while induction brazing is more suitable for smaller-scale, localized applications. The choice ultimately depends on the specific requirements of the project, including production scale, material types, and desired joint quality.
Summary Table:
Aspect | Furnace Brazing | Induction Brazing |
---|---|---|
Production Scale | Ideal for mass production; easily automated. | Suited for smaller-scale or custom jobs; less efficient for mass production. |
Material Compatibility | Excels at joining dissimilar materials, including non-metallic components. | Works well with metals responsive to induction; struggles with non-conductive materials. |
Temperature Control | Precise and uniform heating; minimizes distortion and ensures consistent quality. | Localized heating reduces heat-affected zones but may lack uniformity. |
Cost & Efficiency | Cost-effective for high-volume production; reduces secondary finishing needs. | Energy-efficient but may require skilled operators and setup time. |
Joint Quality | High-integrity joints with greater tensile strength and cleaner surfaces. | Strong joints possible but requires careful control to avoid defects. |
Flexibility | Highly versatile for complex designs and multiple joints in one operation. | Flexible for localized heating but less versatile for large or intricate assemblies. |
Still unsure which brazing method is right for your project? Contact our experts today for personalized guidance!