PVD (Physical Vapor Deposition) and electroplating are both widely used coating technologies, but PVD offers several advantages over traditional electroplating. PVD coatings are known for their superior hardness, durability, wear resistance, and corrosion resistance. They are also more environmentally friendly, as they do not release harmful chemicals or produce toxic residues. Additionally, PVD coatings provide a wider range of aesthetic options and can be applied at lower temperatures, preserving the mechanical properties of the substrate. While electroplating has its own merits, PVD is generally considered a more advanced and sustainable solution for modern coating needs.
Key Points Explained:
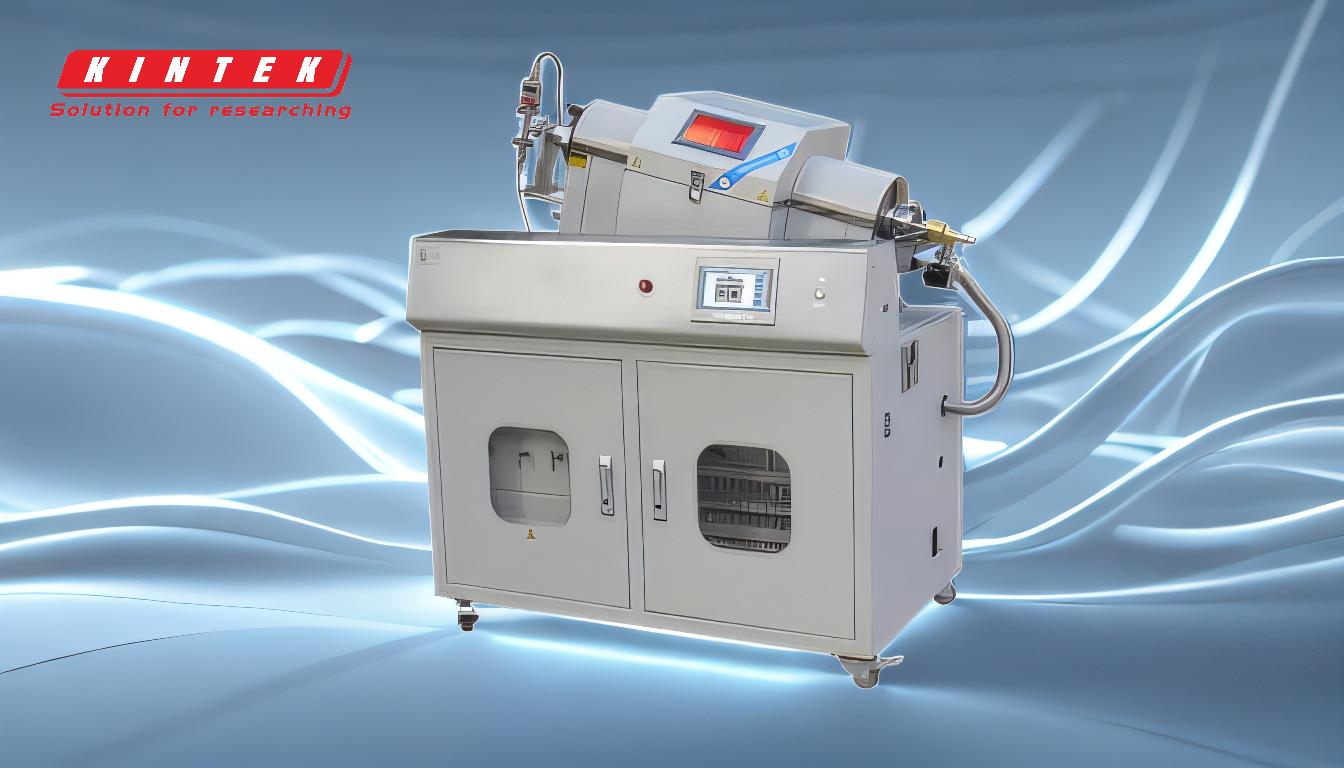
-
Superior Durability and Wear Resistance:
- PVD coatings are harder and more durable than electroplated coatings. They exhibit excellent wear resistance, making them ideal for applications where the coating is subjected to friction or mechanical stress. This is particularly beneficial for tools, automotive components, and industrial equipment.
-
Enhanced Corrosion Resistance:
- PVD coatings provide better protection against rust and corrosion compared to electroplating. This is due to the dense and uniform nature of PVD films, which create a barrier against environmental factors like moisture and chemicals. This makes PVD coatings suitable for outdoor and marine applications.
-
Environmental Safety:
- Unlike electroplating, which often involves the use of toxic chemicals and produces hazardous waste, PVD is a cleaner and more environmentally friendly process. It does not emit harmful by-products or require the disposal of toxic residues, aligning with modern sustainability goals.
-
Aesthetic Versatility:
- PVD coatings offer a wide range of colors and finishes, including metallic, matte, and glossy options. This versatility allows for greater design flexibility in industries like jewelry, consumer electronics, and architecture. Additionally, PVD coatings do not require a clear top coat, reducing the risk of tarnishing or fading over time.
-
Low-Temperature Application:
- PVD processes operate at temperatures below 250 °C, which is beneficial for materials like steel. The low temperature prevents changes to the core microstructure and mechanical properties of the substrate, ensuring that the material retains its strength and integrity.
-
Uniformity and Purity:
- PVD coatings are known for their excellent uniformity and low impurity levels. This results in high-quality films with consistent thickness and composition, which are critical for precision applications in industries like electronics and optics.
-
No Clear Coat Required:
- Traditional electroplating often requires a clear top coat to protect the finish, which can degrade over time. PVD coatings, on the other hand, are inherently durable and do not need additional protective layers, making them more resistant to tarnishing and corrosion.
In summary, while both PVD and electroplating have their uses, PVD stands out as a more advanced, durable, and environmentally friendly coating technology. Its superior performance in terms of hardness, corrosion resistance, and aesthetic options makes it a preferred choice for many modern applications.
Summary Table:
Feature | PVD | Electroplating |
---|---|---|
Durability | Superior hardness and wear resistance | Less durable, prone to wear and tear |
Corrosion Resistance | Excellent protection against rust and corrosion | Moderate protection, less effective in harsh environments |
Environmental Impact | Clean process, no toxic chemicals or residues | Uses toxic chemicals, produces hazardous waste |
Aesthetic Options | Wide range of colors and finishes, no clear coat required | Limited options, often requires a clear top coat |
Temperature | Low-temperature application (below 250 °C), preserves substrate | Higher temperatures may alter substrate properties |
Uniformity | High-quality, consistent films with low impurities | Less uniform, may have impurities |
Ready to upgrade to PVD coatings? Contact us today for expert guidance and solutions!