PVD (Physical Vapor Deposition) coating is generally considered a highly beneficial and advanced surface treatment method. It offers numerous advantages, including exceptional durability, corrosion resistance, and environmental friendliness. PVD coatings are thin yet ultra-hard, making them ideal for applications requiring wear resistance and longevity. They are versatile, applicable to a wide range of materials, and operate at lower temperatures, reducing the risk of thermal damage to substrates. Additionally, PVD coatings are environmentally friendly, as the process occurs in a vacuum, minimizing pollution. These qualities make PVD coatings a superior choice for industries such as automotive, medical, and manufacturing, where durability and sustainability are critical.
Key Points Explained:
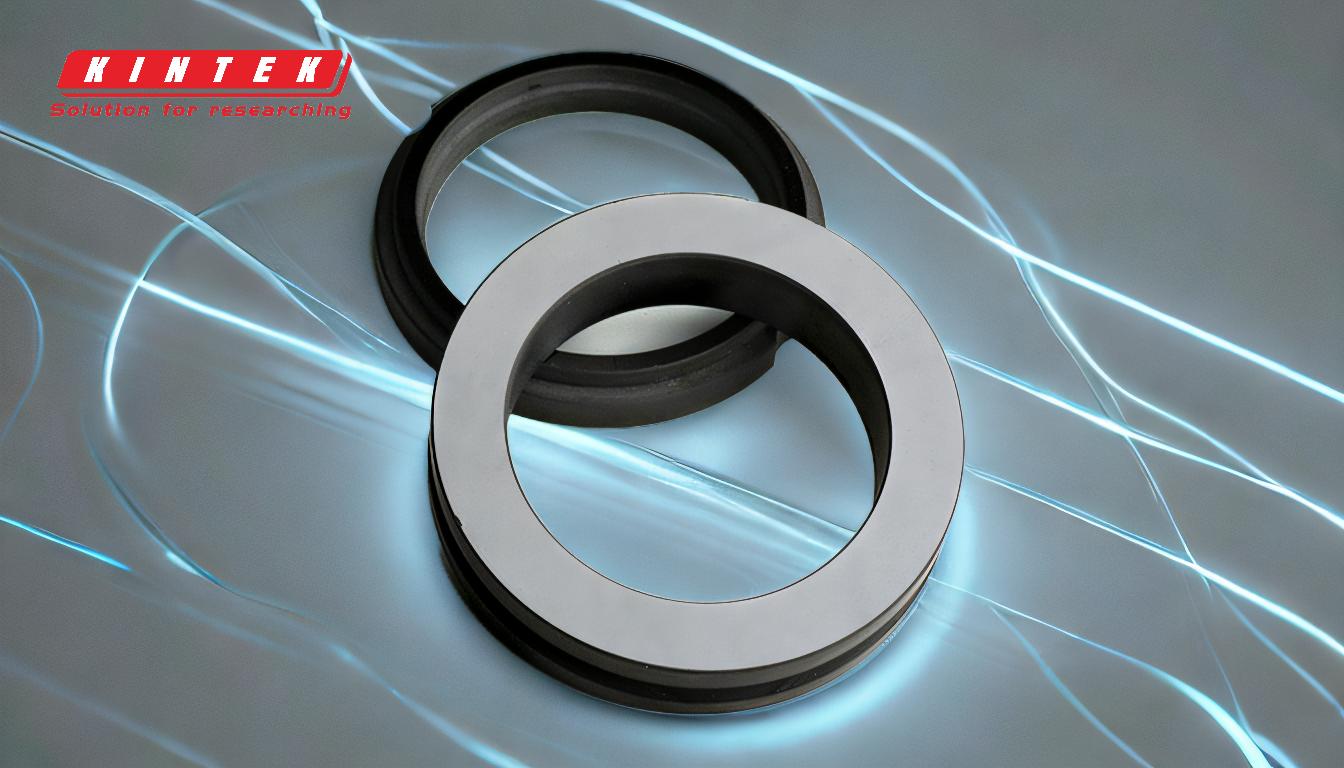
-
Durability and Wear Resistance:
- PVD coatings are highly durable, resistant to tarnishing, corrosion, and scratching. They permeate the surface of the material, creating a thicker and more robust finish compared to other coating methods.
- The coatings are ultra-hard (3~5μm), which enhances wear resistance and extends the lifespan of products. For example, studies show that PVD coatings can increase a product's lifespan by up to ten times, lasting more than 25 years in some cases.
-
Corrosion and Oxidation Resistance:
- PVD coatings are highly resistant to corrosion and oxidation, making them suitable for harsh environments. This property is particularly beneficial for automotive parts, surgical tools, and industrial equipment.
- The thinness of the coating (0.5 to 5 microns) ensures it adheres tightly to the substrate, making it difficult to remove and enhancing its protective qualities.
-
Environmental Friendliness:
- PVD coating is an eco-friendly alternative to traditional methods like chrome plating or electroplating. The process occurs in a vacuum, reducing the release of toxic substances and minimizing environmental pollution.
- It is considered a sustainable and ethical choice for industries looking to reduce their environmental impact.
-
Versatility in Application:
- PVD coatings can be applied to nearly all inorganic materials and some organic materials, making them highly versatile. They are used in industries ranging from automotive (e.g., wheels, pistons) to medical (e.g., surgical tools) and manufacturing (e.g., drill bits, cutting tools).
- The coatings can replicate the original finish of materials, preserving their aesthetic appeal while enhancing functionality.
-
Thermal and Mechanical Properties:
- PVD coatings operate at lower temperatures (around 500 °C), reducing the risk of thermal damage to the substrate. This makes them suitable for heat-sensitive materials.
- The coatings form compressive stress during cooling, which prevents crack formation and expansion. This property is particularly advantageous for interrupted cutting processes like milling.
-
Aesthetic and Functional Benefits:
- PVD coatings offer high-quality finishes with fine, smooth surfaces and rich metallic luster. They are available in multiple color choices, enhancing the visual appeal of products.
- The coatings preserve the sharpness of cutting tools, reduce cutting force and heat, and improve overall performance in demanding applications.
-
Cost-Effectiveness and Longevity:
- While the initial cost of PVD coating may be higher than some traditional methods, its durability and extended lifespan make it cost-effective in the long run. Products coated with PVD require less frequent replacement or maintenance.
- The ability to enhance a product's lifespan by up to ten times translates to significant savings over time, especially in industries where equipment longevity is critical.
In conclusion, PVD coating is an excellent choice for applications requiring durability, corrosion resistance, and environmental sustainability. Its versatility, combined with its ability to enhance both functional and aesthetic properties, makes it a superior alternative to traditional coating methods. Whether for automotive, medical, or industrial use, PVD coatings provide long-lasting protection and performance, making them a valuable investment for manufacturers and consumers alike.
Summary Table:
Key Benefit | Description |
---|---|
Durability | Ultra-hard (3~5μm) coatings enhance wear resistance, extending product lifespan. |
Corrosion Resistance | Resistant to corrosion and oxidation, ideal for harsh environments. |
Environmental Friendliness | Eco-friendly process in a vacuum, reducing pollution and toxic emissions. |
Versatility | Applicable to nearly all inorganic and some organic materials. |
Thermal Properties | Operates at lower temperatures (500°C), reducing thermal damage to substrates. |
Aesthetic & Functional | High-quality finishes, multiple colors, and improved performance. |
Cost-Effectiveness | Long lifespan reduces replacement and maintenance costs. |
Upgrade your products with PVD coating for unmatched durability and sustainability—contact us today to learn more!