PVD (Physical Vapor Deposition) coatings are generally considered non-toxic, safe to handle, and often biocompatible. They are widely used in industries such as cutlery, medical implants, and commercial kitchen equipment due to their durability, wear resistance, and chemical inertness. Once applied, the coatings are firmly bonded to the substrate, making them safe for use and preventing any risk of inhalation. However, during the application process, precautions are necessary to avoid inhaling particles, which can be harmful. PVD coatings are also environmentally friendly, reducing the use of toxic substances compared to other coating methods. Their thinness, ranging from 0.5 to 5 microns, and strong adhesion make them difficult to remove and highly resistant to corrosion and oxidation.
Key Points Explained:
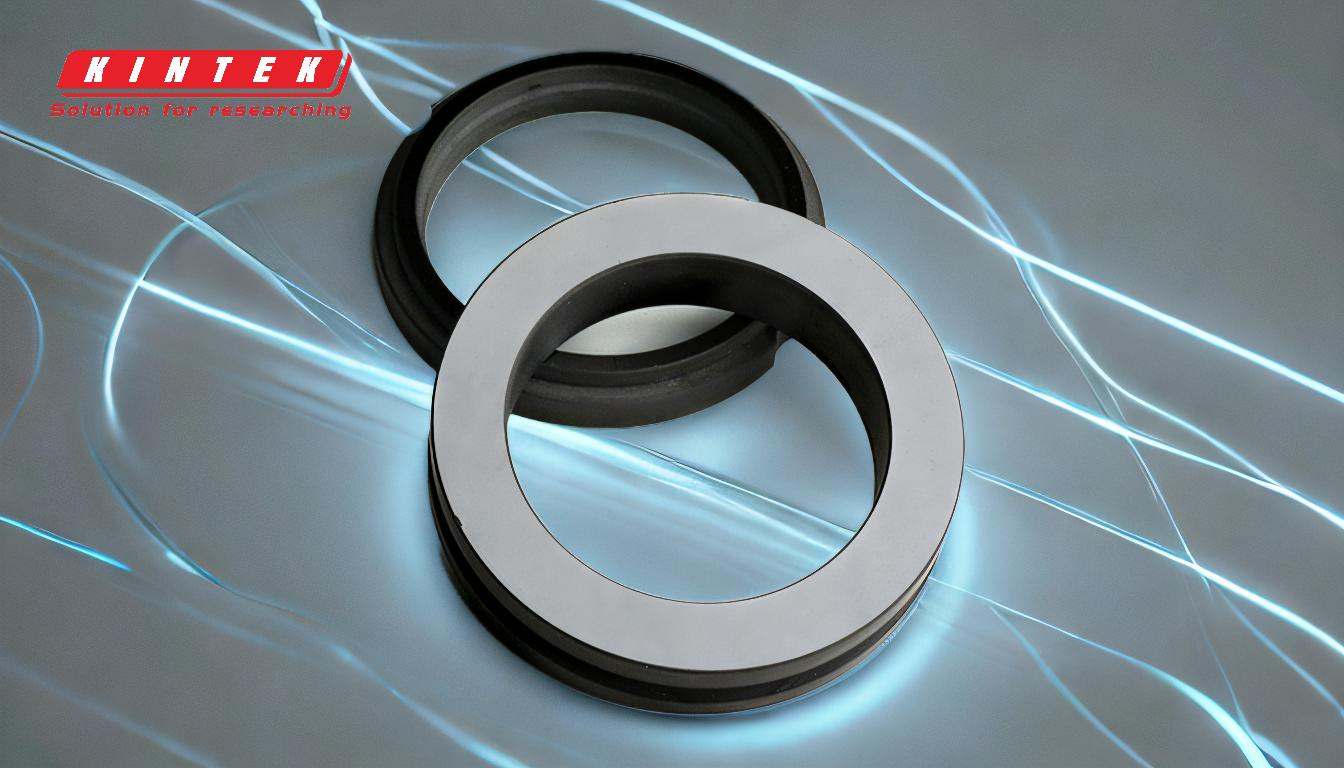
-
Non-Toxicity and Safety of PVD Coatings:
- PVD coatings are non-toxic and safe to handle once applied. The particles are firmly bonded to the substrate, preventing them from becoming airborne and posing any inhalation risk.
- References emphasize that PVD coatings are biocompatible, making them suitable for medical and surgical applications, including implants.
-
Food-Safe and Chemically Inert:
- Most PVD coatings are food-safe due to their strong adhesion to the substrate and chemical inertness. This makes them ideal for use in the cutlery industry and commercial kitchen equipment.
- Their wear-resistant properties further enhance their suitability for functional and decorative applications in food-related industries.
-
Environmental Friendliness:
- PVD processes are environmentally friendly compared to traditional "wet" coating methods, as they reduce the use of toxic substances.
- The technology produces pure, clean, and durable coatings, aligning with sustainable and eco-friendly manufacturing practices.
-
Safety During Application:
- While PVD coatings are safe once applied, the application process requires precautions. Inhaling particles during coating can be harmful, so proper safety measures, such as ventilation and protective equipment, are necessary.
-
Durability and Resistance:
- PVD coatings are highly resistant to corrosion and oxidation, making them durable for long-term use.
- Their thinness (0.5 to 5 microns) and strong adhesion make them difficult to remove, ensuring longevity and reliability in various applications.
-
Industry Applications:
- PVD coatings are widely used in industries such as medical implants, cutlery, and commercial kitchen equipment due to their non-toxic, durable, and wear-resistant properties.
- Their ability to replicate original finishes with minimal effort adds to their versatility in decorative and functional applications.
In summary, PVD coatings are non-toxic, safe, and environmentally friendly, making them a preferred choice for various industries. While precautions are necessary during application, the final product is highly durable, resistant, and suitable for sensitive applications like food handling and medical implants.
Summary Table:
Key Feature | Description |
---|---|
Non-Toxicity | Safe to handle, biocompatible, and suitable for medical and food applications. |
Food-Safe | Chemically inert and wear-resistant, ideal for cutlery and kitchen equipment. |
Environmental Friendliness | Reduces toxic substances, aligning with sustainable manufacturing practices. |
Safety During Application | Precautions needed to avoid inhaling particles during the coating process. |
Durability | Resistant to corrosion, oxidation, and wear, ensuring long-term performance. |
Industry Applications | Widely used in medical implants, cutlery, and commercial kitchen equipment. |
Interested in PVD coatings for your industry? Contact us today to learn more!