Sintered metal can indeed be stronger, depending on the specific materials, process parameters, and intended application. Sintering involves heating compacted metal powders below their melting point, allowing the particles to bond through diffusion. This process enhances mechanical properties such as strength, density, and hardness. However, the strength of sintered metals depends on factors like sintering time, temperature, and cooling rate. Over-sintering or improper cooling can lead to defects, reducing strength. Sintering is particularly advantageous for creating complex shapes, conserving material, and producing isotropic materials with consistent properties.
Key Points Explained:
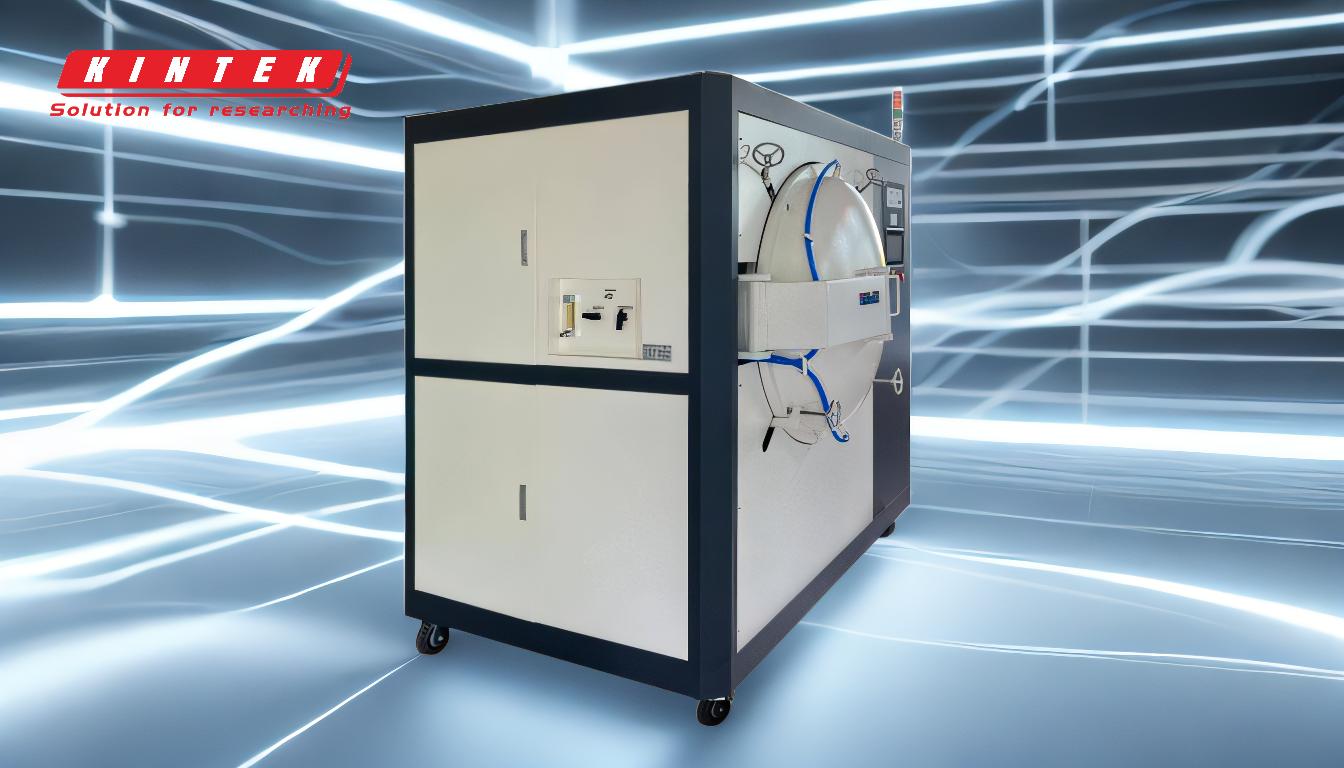
-
What is Sintering?
- Sintering is a powder metallurgy process where metal powders are compacted into a desired shape and then heated below their melting point in a controlled atmosphere. This causes the particles to bond through diffusion, improving the material's mechanical properties.
- The process involves three main steps: blending, compaction, and sintering. Blending ensures a uniform mixture of powdered metals, alloying elements, and lubricants. Compaction shapes the powder into a "green" part, and sintering bonds the particles to create a dense, strong material.
-
How Sintering Enhances Strength:
- During sintering, the diffusion of particles increases the material's density, leading to improved strength and hardness. The controlled heating and cooling rates allow for fine-tuning of mechanical properties.
- For example, increasing sintering time can transform phases within the material, such as α-SI3N4 to β-SI3N4, increasing hardness. However, excessive sintering time can lead to abnormal grain growth and defects, reducing strength.
-
Advantages of Sintered Metals:
- Sintered metals offer high dimensional precision, making them ideal for complex shapes and large-scale production.
- The process is energy-efficient, cost-effective, and environmentally friendly, with no harmful emissions.
- Sintering can produce unique isotropic materials with consistent properties in all directions, as well as parts with self-lubricating and vibration-damping properties.
-
Factors Affecting Strength:
- Sintering Time and Temperature: Proper control is crucial. Over-sintering can cause defects, while insufficient sintering may result in weak bonds.
- Cooling Rate: Adjusting the cooling rate can optimize properties like hardness and toughness.
- Material Composition: The choice of powdered metals, alloying elements, and additives determines the final properties.
-
Applications and Limitations:
- Sintering is particularly useful for materials with high melting points or complex compositions that are difficult to process through melting and casting.
- While sintered metals are strong, their strength may not match that of fully melted and cast metals in some applications. However, the ability to create complex shapes and conserve material often outweighs this limitation.
In summary, sintered metals can be stronger, but their strength depends on careful control of the sintering process. The method offers numerous advantages, including material conservation, energy efficiency, and the ability to produce complex, high-precision parts.
Summary Table:
Key Aspect | Details |
---|---|
What is Sintering? | A powder metallurgy process bonding metal particles through diffusion. |
Strength Factors | Sintering time, temperature, cooling rate, and material composition. |
Advantages | High precision, energy efficiency, and ability to create complex shapes. |
Applications | Ideal for high-melting-point materials and complex compositions. |
Limitations | Strength may not match fully melted metals in some cases. |
Learn how sintered metals can enhance your projects—contact our experts today!