Sintering, as a manufacturing process, has both eco-friendly and environmentally concerning aspects depending on the materials used, the specific sintering method, and the implementation of safety and sustainability measures. While certain sintering processes, such as metal sintering and Selective Laser Sintering (SLS), are considered green due to minimal emissions and efficient material usage, other processes involving high temperatures and nanoparticles can release harmful emissions or pose health risks. The eco-friendliness of sintering is further influenced by adherence to governmental regulations and the adoption of proper ventilation and safety protocols.
Key Points Explained:
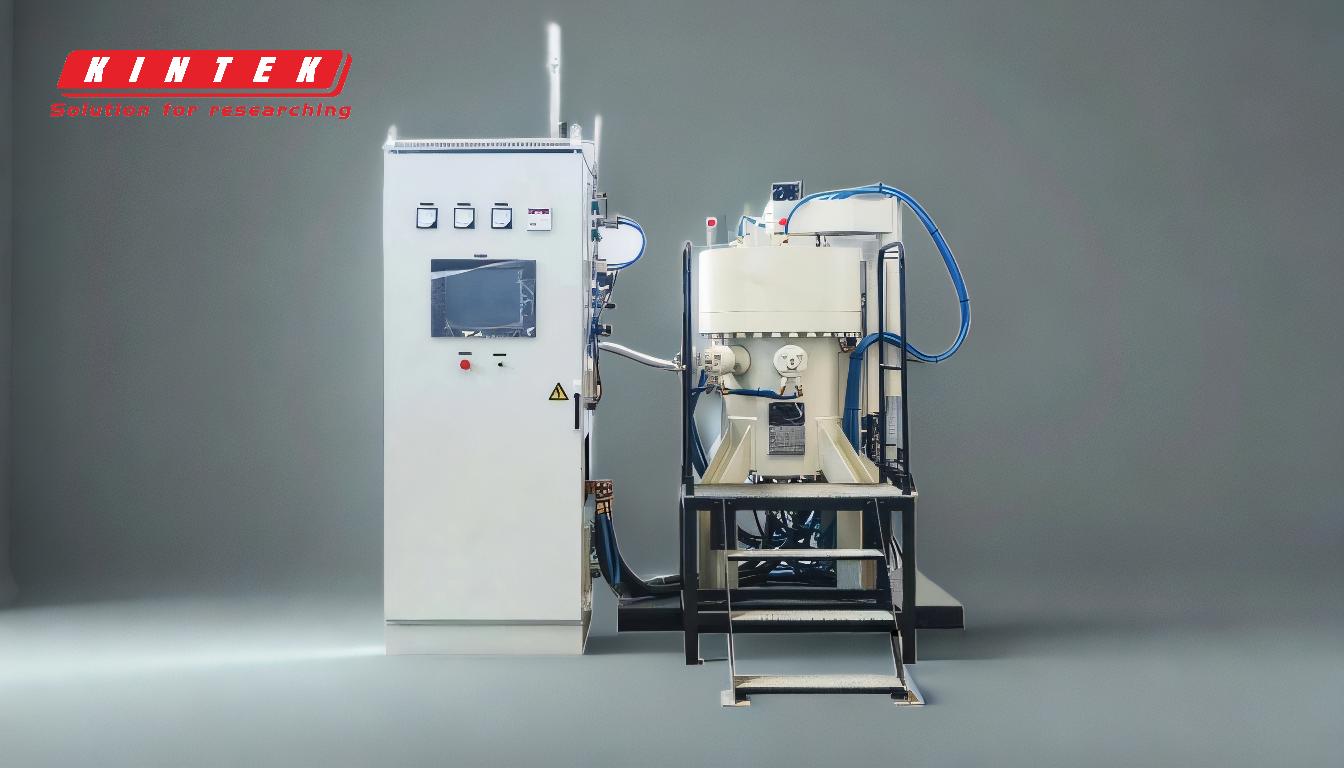
-
High-Temperature Processing and Emissions:
- Sintering often involves processing materials at high temperatures, which can release harmful emissions into the environment. These emissions may include toxic fumes, irritants, or particulate matter, depending on the materials being sintered.
- For example, ceramic or metal nanoparticles used in sintering can produce fumes that require proper ventilation and safety precautions to mitigate health risks.
-
Material-Dependent Environmental Impact:
- The eco-friendliness of sintering largely depends on the materials used. Some materials, such as certain metals, are considered environmentally benign during sintering, while others, like nanoparticles, may have medical or environmental consequences if not handled carefully.
- For instance, metal sintering is often labeled a "green technology" because it typically does not produce harmful emissions, making it a preferred choice for companies aiming to reduce their environmental footprint.
-
Sustainability of Selective Laser Sintering (SLS):
- SLS is a form of sintering that stands out for its sustainability. Unlike subtractive manufacturing methods, which generate significant material waste, SLS builds parts layer by layer using only the required amount of material. This efficient use of resources minimizes waste and contributes to its eco-friendly reputation.
-
Governmental Regulations and Policies:
- The environmental impact of sintering has led to the implementation of governmental norms and policies aimed at controlling emissions and ensuring safe practices. Compliance with these regulations can affect production rates and operational costs but is essential for minimizing environmental harm.
-
Safety and Ventilation Requirements:
- Processes involving high temperatures and potentially hazardous materials require stringent safety measures, such as proper ventilation systems and protective equipment. These precautions help mitigate the release of toxic fumes and ensure a safer working environment.
-
Balancing Eco-Friendliness and Practicality:
- While some sintering processes are inherently more eco-friendly than others, the overall environmental impact can be managed through careful material selection, adherence to regulations, and the adoption of sustainable practices like SLS. This balance allows companies to leverage the benefits of sintering while minimizing its ecological footprint.
By considering these factors, companies can make informed decisions about sintering processes that align with their sustainability goals while ensuring compliance with environmental and safety standards.
Summary Table:
Aspect | Details |
---|---|
High-Temperature Emissions | Releases toxic fumes or particulate matter; requires proper ventilation. |
Material Impact | Metals: eco-friendly; nanoparticles: potential environmental/health risks. |
SLS Sustainability | Minimizes waste by using only required material, making it eco-friendly. |
Regulations | Government policies control emissions and ensure safe practices. |
Safety Measures | Ventilation and protective equipment mitigate health risks. |
Eco-Friendly Balance | Material selection, regulations, and sustainable practices reduce impact. |
Learn how to make sintering more sustainable for your business—contact our experts today!