Yes, there is a significant difference between a kiln and a furnace, primarily in their design, purpose, and operating temperatures. A kiln is specifically designed for processes like drying ceramics, firing pottery, or adding glaze, and it operates at very high temperatures. On the other hand, a furnace is engineered to reach extreme temperatures and is typically used for industrial metal finishing, melting, or heat treatment. While both are high-temperature devices, their applications and construction differ to suit their specific uses.
Key Points Explained:
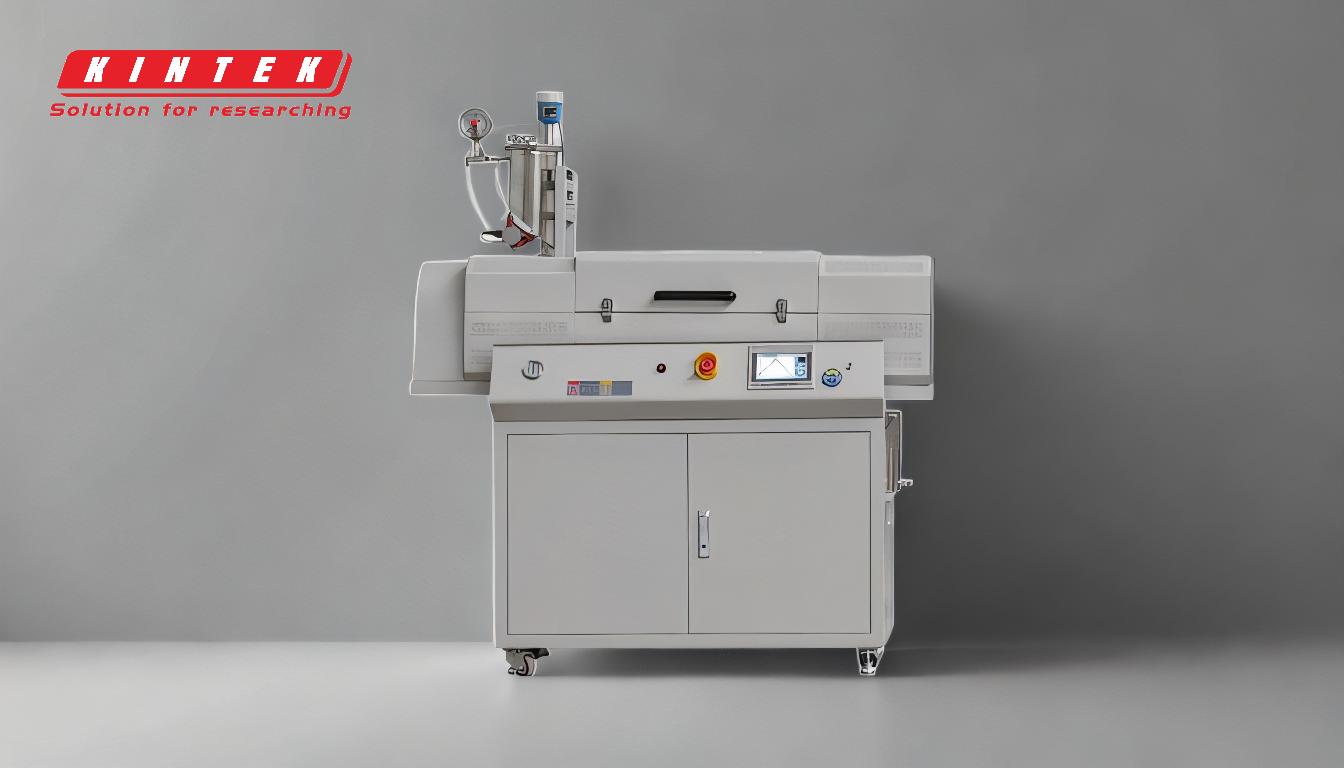
-
Purpose and Applications:
- Kiln: Primarily used for ceramics, pottery, and glasswork. It is designed to dry, fire, or glaze materials at high temperatures.
- Furnace: Used in industrial settings for metal-related processes such as melting, refining, or heat treatment. It is tailored for extreme temperatures required in metallurgy.
-
Design and Construction:
- Kiln: Typically an enclosed oven with precise temperature control, often insulated to maintain consistent heat for delicate processes like pottery firing.
- Furnace: Built to withstand extreme heat and often includes features like refractory linings to handle molten metals or high-temperature industrial processes.
-
Operating Temperatures:
- Kiln: Operates at very high temperatures but generally lower than those of a furnace. The temperature range is optimized for ceramics and glazes.
- Furnace: Capable of reaching much higher temperatures, often exceeding those of a kiln, to accommodate metal melting or refining.
-
Heat Source and Control:
- Kiln: Often uses electric, gas, or wood-fired heat sources, with precise controls to ensure even heating for artistic or craft purposes.
- Furnace: Typically uses gas, oil, or electric power, with robust controls to manage extreme heat for industrial applications.
-
Examples of Use:
- Kiln: Used by potters to fire clay creations or by glass artists to fuse glass pieces.
- Furnace: Employed in steel mills to melt iron ore or in foundries to cast metal components.
In summary, while both kilns and furnaces are high-temperature devices, they serve distinct purposes and are designed differently to meet the specific needs of their applications. A kiln is more suited for artistic and craft-related tasks, whereas a furnace is geared toward industrial metal processing.
Summary Table:
Aspect | Kiln | Furnace |
---|---|---|
Purpose | Ceramics, pottery, glasswork (drying, firing, glazing) | Industrial metal processing (melting, refining, heat treatment) |
Design | Enclosed oven with precise temperature control, insulated for consistency | Built to withstand extreme heat, often with refractory linings |
Operating Temperatures | High temperatures, optimized for ceramics and glazes | Extreme temperatures, often exceeding kiln ranges for metal processing |
Heat Source | Electric, gas, or wood-fired with precise controls | Gas, oil, or electric power with robust controls |
Examples of Use | Potters firing clay, glass artists fusing glass | Steel mills melting iron ore, foundries casting metal components |
Need help choosing the right high-temperature equipment for your needs? Contact our experts today!