Annealing is a heat treatment process effective on a variety of metals, including steel, alloy steel, aluminum, brass, and copper. The process involves heating the metal to a specific temperature, holding it at that temperature, and then cooling it in a controlled manner. This treatment softens the metal, increases its ductility, relieves internal stresses, and improves workability, machinability, and mechanical or electrical properties. Annealing is particularly useful for reversing work hardening caused by cold forming, drawing, or bending, and for removing stresses from welding. Each metal requires specific annealing conditions to achieve optimal results.
Key Points Explained:
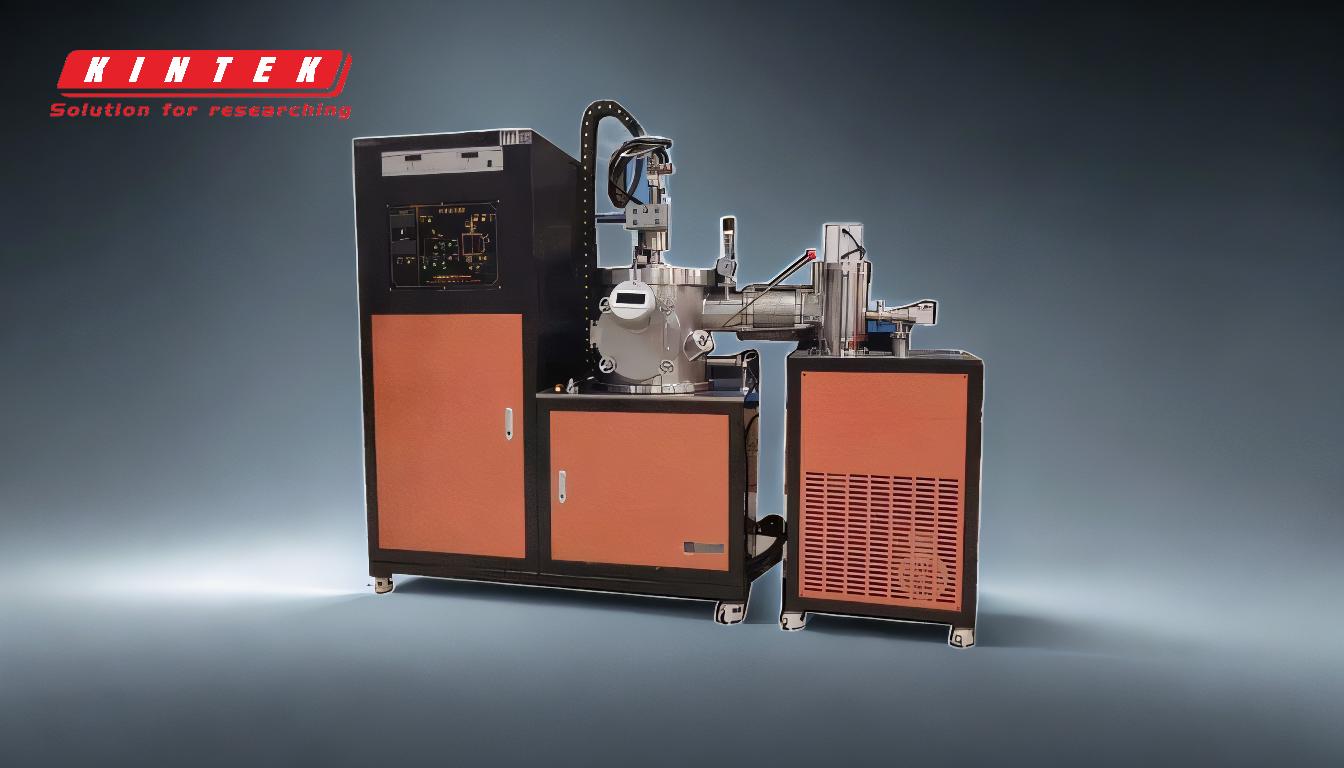
-
Metals Suitable for Annealing:
- Steel and Alloy Steel: These are the most commonly annealed metals due to their widespread use in industrial applications. Annealing improves their ductility and machinability.
- Aluminum: Annealing aluminum enhances its workability and reduces hardness, making it easier to form and shape.
- Brass: This alloy of copper and zinc benefits from annealing by becoming more ductile and easier to work with, especially after cold working.
- Copper: Annealing copper increases its ductility and electrical conductivity, making it ideal for electrical applications and further forming processes.
-
Purpose of Annealing:
- Softening the Metal: Annealing reduces the hardness of the metal, making it easier to cut, shape, or form.
- Increasing Ductility: The process makes the metal more pliable, allowing it to be stretched or bent without breaking.
- Relieving Internal Stresses: Annealing eliminates stresses that occur during manufacturing processes like welding, cold working, or machining.
- Improving Workability: By enhancing ductility and reducing hardness, annealing makes the metal easier to work with in subsequent processes.
-
Applications of Annealing:
- Reversing Work Hardening: Cold working processes like drawing, bending, or rolling can harden metals, making them brittle. Annealing reverses this effect, restoring ductility.
- Stress Relief After Welding: Welding can introduce internal stresses in metals. Annealing helps to relieve these stresses, improving the structural integrity of the welded joint.
- Enhancing Machinability: Annealed metals are easier to machine, reducing tool wear and improving surface finish.
- Improving Mechanical and Electrical Properties: For some metals, annealing can enhance properties like tensile strength, toughness, or electrical conductivity.
-
Annealing Process:
- Heating: The metal is heated to a specific temperature, which varies depending on the type of metal. For example, steel is typically heated to around 700–900°C, while aluminum is heated to 300–400°C.
- Holding: The metal is held at the annealing temperature for a set period to ensure uniform heating and structural changes.
- Cooling: The metal is cooled slowly, often in a furnace or by burying it in an insulating material, to prevent the reintroduction of stresses.
-
Benefits of Annealing:
- Improved Formability: Annealed metals can be shaped more easily without cracking or breaking.
- Enhanced Performance: The process improves the mechanical and electrical properties of the metal, making it suitable for demanding applications.
- Cost Efficiency: By reducing tool wear and improving workability, annealing can lower manufacturing costs.
-
Considerations for Purchasers:
- Material Selection: Choose metals that benefit from annealing based on the intended application (e.g., copper for electrical components, aluminum for lightweight structures).
- Process Specifications: Ensure the annealing process is tailored to the specific metal and desired outcomes (e.g., temperature, cooling rate).
- Quality Control: Verify that the annealing process is performed correctly to achieve the desired properties and avoid defects.
By understanding the types of metals that benefit from annealing and the specific advantages it offers, purchasers can make informed decisions about material selection and processing to meet their project requirements.
Summary Table:
Aspect | Details |
---|---|
Metals Suitable | Steel, alloy steel, aluminum, brass, copper |
Key Benefits | Softens metal, increases ductility, relieves stress, improves workability |
Applications | Reverses work hardening, stress relief after welding, enhances machinability |
Process Steps | Heating, holding, slow cooling |
Considerations | Material selection, process specifications, quality control |
Optimize your metal processing with annealing—contact our experts today for tailored solutions!