When deciding whether to braze or weld aluminum, it’s essential to consider the specific application, joint strength requirements, and the challenges associated with each method. Brazing is particularly useful for joining aluminum in situations where maintaining the integrity of the base material is critical, as it minimizes the risk of cracking and metallurgical changes. However, brazed joints are generally weaker and less heat-resistant than welded joints. Welding, on the other hand, provides stronger joints but requires careful control of heat input to avoid distortion and damage to the aluminum. The choice ultimately depends on the intended use of the joint, the materials involved, and the desired mechanical properties.
Key Points Explained:
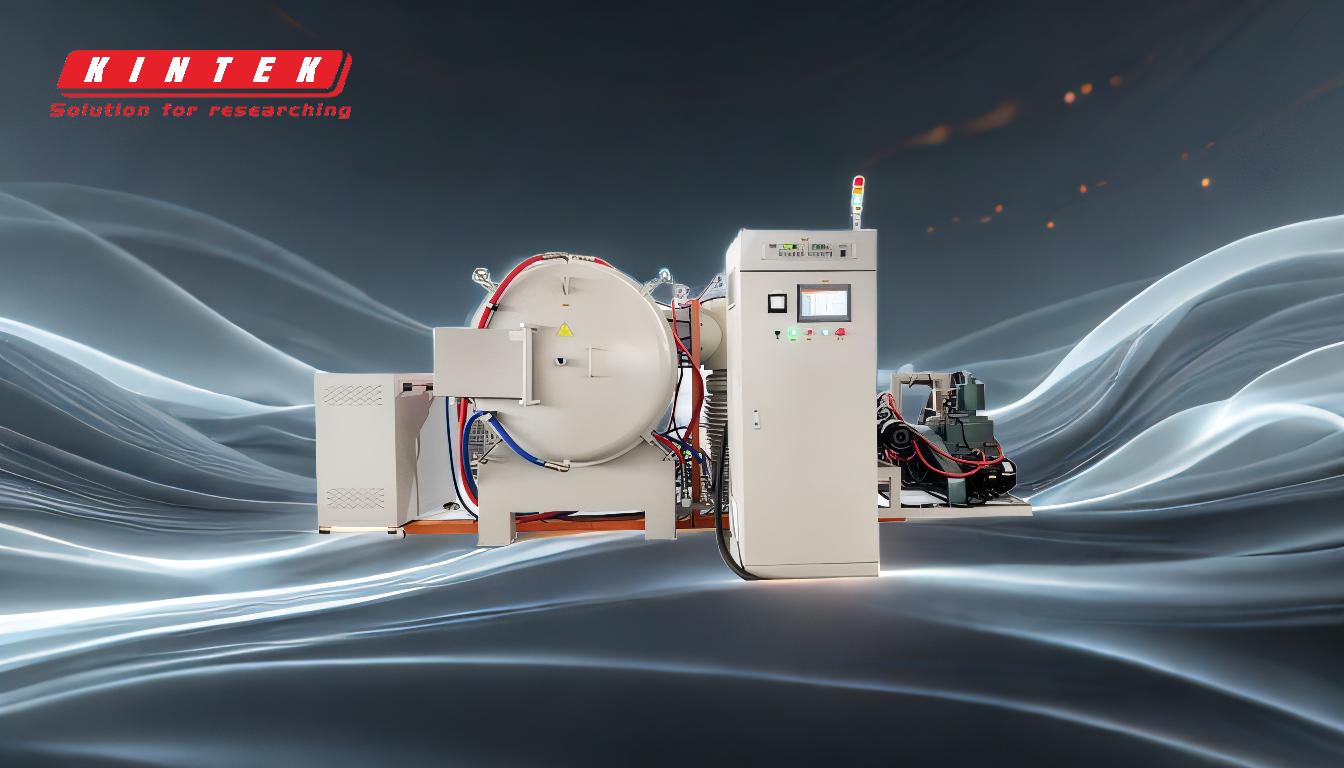
-
Brazing Aluminum:
- Process Overview: Brazing involves joining aluminum parts using a filler metal that melts at a lower temperature than the base material. The two main types are flux brazing and fluxless brazing (e.g., vacuum brazing).
-
Advantages:
- Reduced risk of cracking and metallurgical changes in the heat-affected zone (HAZ).
- Suitable for small repairs or intricate assemblies where welding might be impractical.
- In vacuum brazing, the aluminum oxide layer cracks under heat, allowing the brazing alloy to reach the base material, and oxidation is prevented by maintaining a high vacuum and using getter materials.
-
Limitations:
- Brazed joints have lower strength and heat resistance compared to welded joints.
- Requires precise control of temperature uniformity (±5.5°C) and vacuum levels (10⁻⁵ mbar or better) for optimal results.
-
Welding Aluminum:
- Process Overview: Welding involves melting the base aluminum material to form a joint, often with the addition of a filler metal. Common methods include TIG (Tungsten Inert Gas) and MIG (Metal Inert Gas) welding.
-
Advantages:
- Produces stronger joints with higher heat resistance, making it suitable for structural applications.
- Can handle thicker materials and higher stress loads compared to brazing.
-
Limitations:
- Higher risk of cracking and distortion due to the high heat input required.
- Requires skilled operators and precise control of welding parameters to avoid defects.
-
Application Considerations:
- Joint Strength: If the joint will be subjected to high stress or heat, welding is generally the better choice. For less demanding applications, brazing may suffice.
- Material Thickness: Welding is better suited for thicker materials, while brazing works well for thinner sections or delicate components.
- Complexity of Assembly: Brazing is often preferred for complex or multi-part assemblies where welding might be challenging.
-
Process Requirements:
- Brazing: Requires careful control of temperature, vacuum levels, and cycle times. Multiple-zone temperature-controlled furnaces are often used to ensure uniformity.
- Welding: Requires skilled operators, proper shielding gases, and precise control of heat input to prevent defects like porosity and cracking.
-
Cost and Efficiency:
- Brazing: Generally more cost-effective for small-scale repairs or assemblies due to lower equipment and labor costs. However, the process can be time-consuming, especially for vacuum brazing.
- Welding: May involve higher initial costs due to the need for specialized equipment and skilled labor, but it is often more efficient for large-scale or high-strength applications.
In summary, the decision to braze or weld aluminum depends on the specific requirements of the application, including joint strength, material thickness, and the complexity of the assembly. Brazing offers advantages in terms of reduced risk of cracking and suitability for intricate designs, while welding provides stronger, more heat-resistant joints for demanding applications.
Summary Table:
Aspect | Brazing Aluminum | Welding Aluminum |
---|---|---|
Process Overview | Uses a filler metal with a lower melting point than the base material. | Melts the base material, often with a filler metal, to form a joint. |
Advantages | - Reduced risk of cracking and metallurgical changes. | - Stronger joints with higher heat resistance. |
- Suitable for intricate assemblies or small repairs. | - Ideal for structural applications and thicker materials. | |
Limitations | - Lower joint strength and heat resistance. | - Higher risk of cracking and distortion. |
- Requires precise temperature and vacuum control. | - Requires skilled operators and precise heat input control. | |
Best Applications | - Thin materials, delicate components, or complex assemblies. | - Thicker materials, high-stress, or high-heat applications. |
Cost and Efficiency | - Cost-effective for small-scale repairs but can be time-consuming. | - Higher initial costs but efficient for large-scale or high-strength applications. |
Still unsure whether to braze or weld your aluminum project? Contact our experts today for personalized guidance!