Annealing is a critical heat treatment process used to alter the physical and mechanical properties of materials, primarily metals. It is required under specific conditions where the material needs to be softened, made more ductile, or relieved of internal stresses. This process is essential for improving machinability, facilitating cold working, enhancing mechanical or electrical properties, and ensuring dimensional stability. Annealing is particularly useful after fabrication processes like casting or cold working, where internal stresses and hardness can compromise the material's performance. By heating the material to its recrystallization temperature, holding it at that temperature, and then cooling it at a controlled rate, annealing helps achieve a more uniform and workable structure.
Key Points Explained:
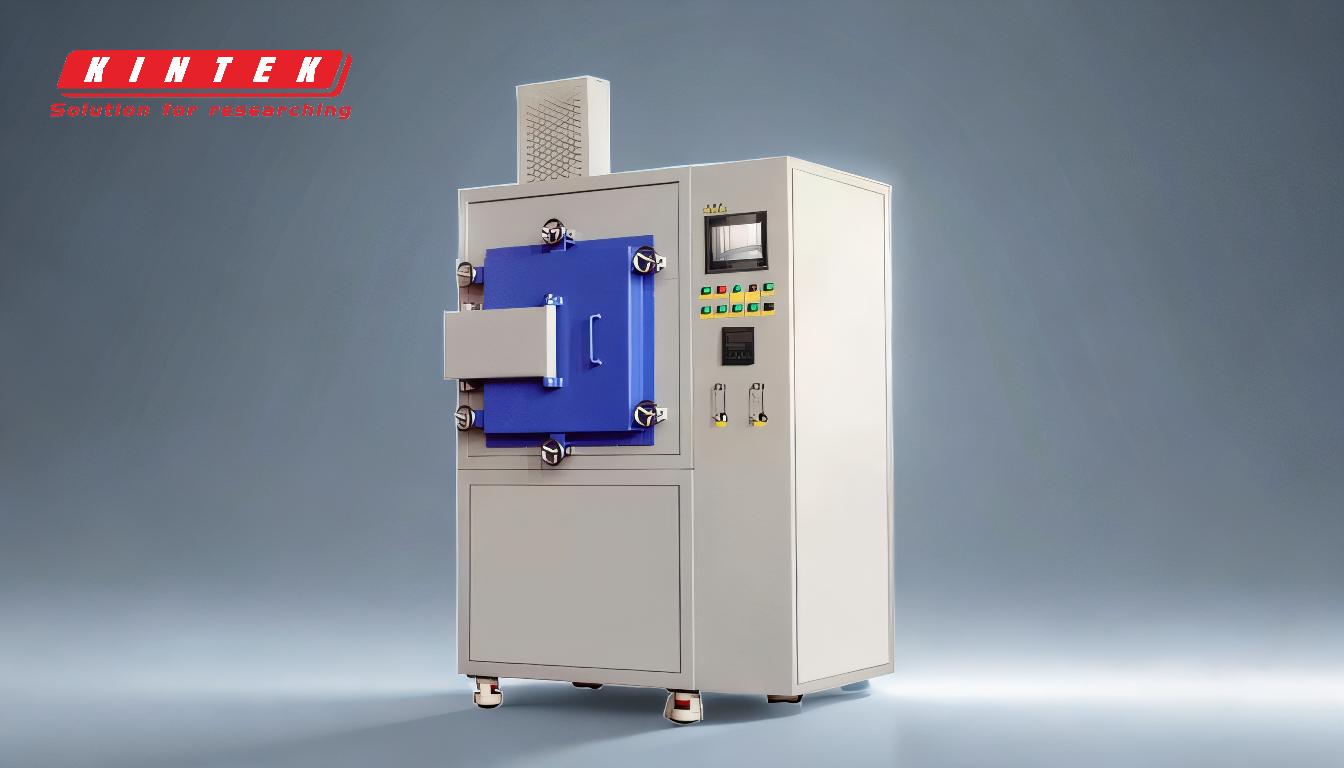
-
Reduction of Hardness and Increase in Ductility:
- Annealing is primarily used to reduce the hardness of a material, making it softer and more ductile. This is achieved by heating the material to a specific temperature (usually its recrystallization temperature) and then cooling it slowly. The process reduces the number of dislocations in the crystal structure, which in turn decreases hardness and increases ductility. This makes the material easier to machine, cold work, or shape without the risk of cracking or fracturing under stress.
-
Relief of Internal Stresses:
- Internal stresses can develop in materials during manufacturing processes such as casting, welding, or cold working. These stresses can lead to material failure or deformation over time. Annealing helps relieve these stresses by allowing the material to reach a more stable and uniform internal structure. This is particularly important for components that will be subjected to mechanical loads or thermal cycling in service.
-
Improvement of Machinability:
- Materials that are too hard can be difficult to machine, leading to increased tool wear and poor surface finishes. Annealing softens the material, making it easier to cut, drill, or shape. This is especially beneficial for metals that need to undergo extensive machining operations, as it reduces the risk of tool breakage and improves the efficiency of the machining process.
-
Facilitation of Cold Working:
- Cold working processes, such as rolling, drawing, or forging, can significantly increase the hardness and strength of a material but also make it more brittle. Annealing is often performed between cold working stages to restore ductility and reduce brittleness, allowing for further processing without the risk of cracking. This is crucial for producing complex shapes or thin sections that require multiple forming steps.
-
Enhancement of Mechanical and Electrical Properties:
- Annealing can improve the mechanical properties of a material, such as its tensile strength, toughness, and fatigue resistance, by refining its grain structure. Additionally, for electrical materials like copper or aluminum, annealing can enhance electrical conductivity by reducing defects in the crystal lattice. This makes the material more suitable for applications where both mechanical strength and electrical performance are critical.
-
Production of a Uniform and Homogeneous Structure:
- During manufacturing, materials can develop non-uniform microstructures due to uneven cooling or mechanical deformation. Annealing helps produce a more uniform and homogeneous internal structure by allowing the material to recrystallize and form equiaxed grains. This uniformity improves the material's overall performance and reliability, especially in applications where consistency is key.
-
Restoration of Material to a "Soft" Condition:
- After processes like cold working or heat treatment, materials may become too hard or brittle for further processing. Annealing restores the material to a softer condition, making it easier to perform additional machining, forming, or heat treatment operations. This is particularly important for materials that need to undergo multiple stages of processing to achieve the desired final properties.
-
Dimensional Stability:
- Annealing can help improve the dimensional stability of a material by reducing residual stresses that can cause warping or distortion over time. This is especially important for precision components that must maintain tight tolerances during their service life.
In summary, annealing is required under conditions where materials need to be softened, made more ductile, or relieved of internal stresses. It is a versatile process that enhances machinability, facilitates cold working, improves mechanical and electrical properties, and ensures dimensional stability, making it indispensable in various manufacturing and engineering applications.
Summary Table:
Key Benefits of Annealing | Description |
---|---|
Reduction of Hardness | Softens materials, making them more ductile and easier to machine or shape. |
Relief of Internal Stresses | Reduces internal stresses caused by manufacturing processes like casting or welding. |
Improved Machinability | Enhances ease of cutting, drilling, or shaping, reducing tool wear. |
Facilitation of Cold Working | Restores ductility between cold working stages, preventing cracking. |
Enhanced Mechanical Properties | Improves tensile strength, toughness, and fatigue resistance. |
Uniform Microstructure | Produces a homogeneous internal structure for better consistency. |
Restoration to Soft Condition | Prepares materials for further processing after hardening. |
Dimensional Stability | Reduces warping or distortion, ensuring tight tolerances. |
Need annealing solutions for your materials? Contact our experts today to learn more!