Ceramics that can withstand high temperatures are called refractory ceramics or high-temperature ceramics. These materials are engineered to maintain their structural integrity and performance under extreme heat, often exceeding 1,000°C (1,832°F). They are widely used in industries such as metallurgy, aerospace, and energy due to their exceptional thermal stability, resistance to thermal shock, and chemical inertness. Examples include alumina, silicon carbide, zirconia, and mullite. These ceramics are critical in applications like furnace linings, kiln furniture, and thermal barriers, where ordinary materials would fail.
Key Points Explained:
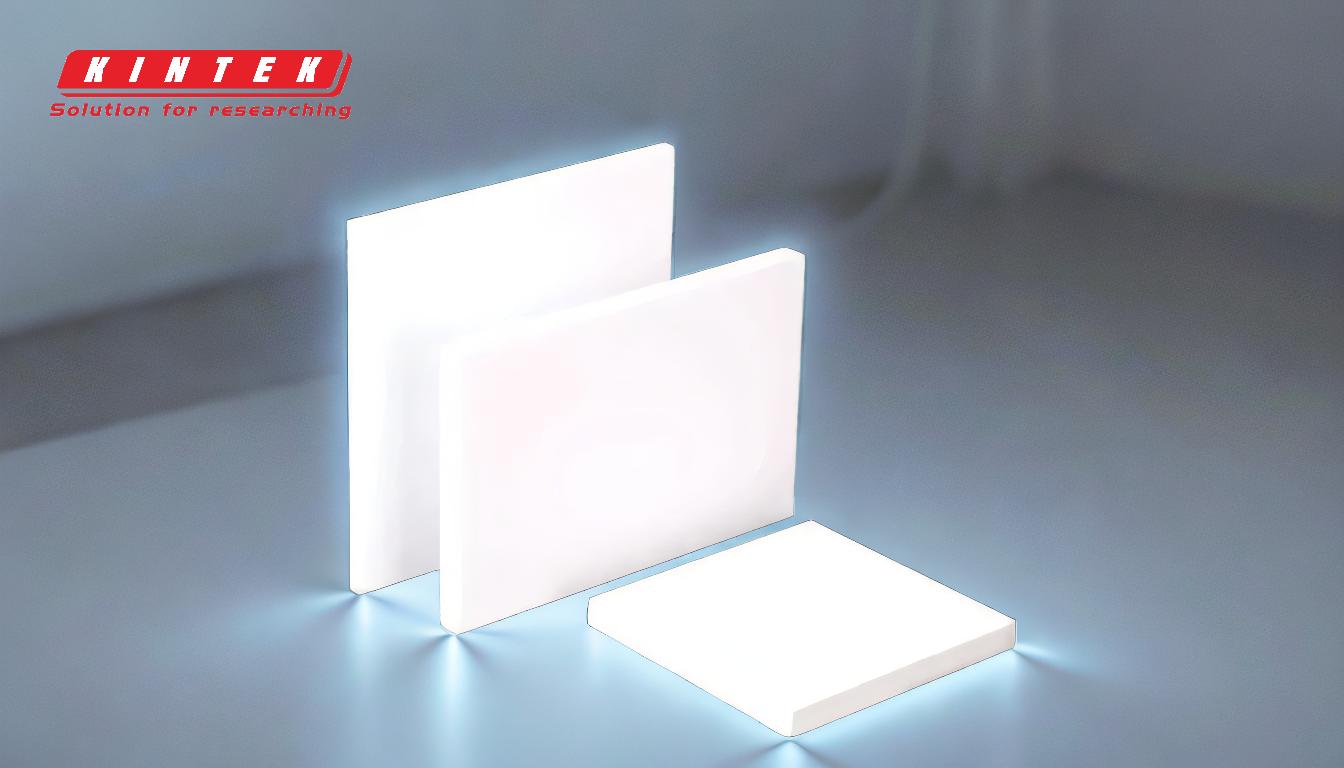
-
Definition of High-Temperature Ceramics
- High-temperature ceramics, also known as refractory ceramics, are materials specifically designed to withstand extreme heat without degrading.
- They exhibit properties such as high melting points, low thermal expansion, and resistance to thermal shock, making them ideal for high-temperature environments.
-
Key Properties of High-Temperature Ceramics
- Thermal Stability: These ceramics can maintain their mechanical strength and structural integrity at temperatures exceeding 1,000°C.
- Thermal Shock Resistance: They can withstand rapid temperature changes without cracking or breaking.
- Chemical Inertness: They resist reactions with corrosive substances, making them suitable for harsh environments.
- Low Thermal Conductivity: This property helps in insulating heat and reducing energy loss.
-
Common Types of High-Temperature Ceramics
- Alumina (Al₂O₃): Widely used for its high melting point (2,072°C) and excellent electrical insulation properties.
- Silicon Carbide (SiC): Known for its exceptional thermal conductivity and resistance to wear and corrosion.
- Zirconia (ZrO₂): Valued for its toughness and ability to withstand thermal cycling.
- Mullite (3Al₂O₃·2SiO₂): Combines high thermal stability with low thermal expansion, making it ideal for furnace linings.
-
Applications of High-Temperature Ceramics
- Industrial Furnaces: Used as linings and components in furnaces for metal smelting and glass manufacturing.
- Aerospace: Utilized in thermal protection systems for spacecraft and jet engines.
- Energy Sector: Employed in gas turbines, nuclear reactors, and solar energy systems.
- Kiln Furniture: Supports and protects items during high-temperature firing processes.
-
Advantages Over Other Materials
- Compared to metals and polymers, high-temperature ceramics offer superior performance in extreme heat, with minimal degradation over time.
- They are lightweight, durable, and resistant to oxidation, making them cost-effective for long-term use.
-
Challenges and Considerations
- Brittleness: While strong under compression, ceramics can be brittle and prone to cracking under tension.
- Cost: High-temperature ceramics can be expensive to produce and process.
- Design Limitations: Their brittleness requires careful engineering to avoid stress concentrations.
-
Future Trends in High-Temperature Ceramics
- Research is focused on developing new ceramic composites with enhanced properties, such as increased toughness and reduced brittleness.
- Advances in additive manufacturing (3D printing) are enabling the production of complex ceramic components with improved performance.
By understanding the properties, types, and applications of high-temperature ceramics, purchasers can make informed decisions when selecting materials for demanding thermal environments.
Summary Table:
Property | Description |
---|---|
Thermal Stability | Maintains strength at temperatures exceeding 1,000°C. |
Thermal Shock Resistance | Withstands rapid temperature changes without cracking. |
Chemical Inertness | Resists reactions with corrosive substances. |
Low Thermal Conductivity | Insulates heat and reduces energy loss. |
Common Types | Alumina, Silicon Carbide, Zirconia, Mullite. |
Applications | Industrial furnaces, aerospace, energy sector, kiln furniture. |
Need high-temperature ceramics for your project? Contact our experts today for tailored solutions!