Heat treatment is a critical process in metallurgy and material science, used to alter the physical and mechanical properties of metals and alloys. Common heat treatment methods include annealing, case hardening, precipitation strengthening, tempering, carburizing, normalizing, and quenching. Each method serves a specific purpose, such as improving ductility, increasing hardness, or relieving internal stresses. These processes are essential for achieving desired material characteristics in various industries, including automotive, aerospace, and manufacturing.
Key Points Explained:
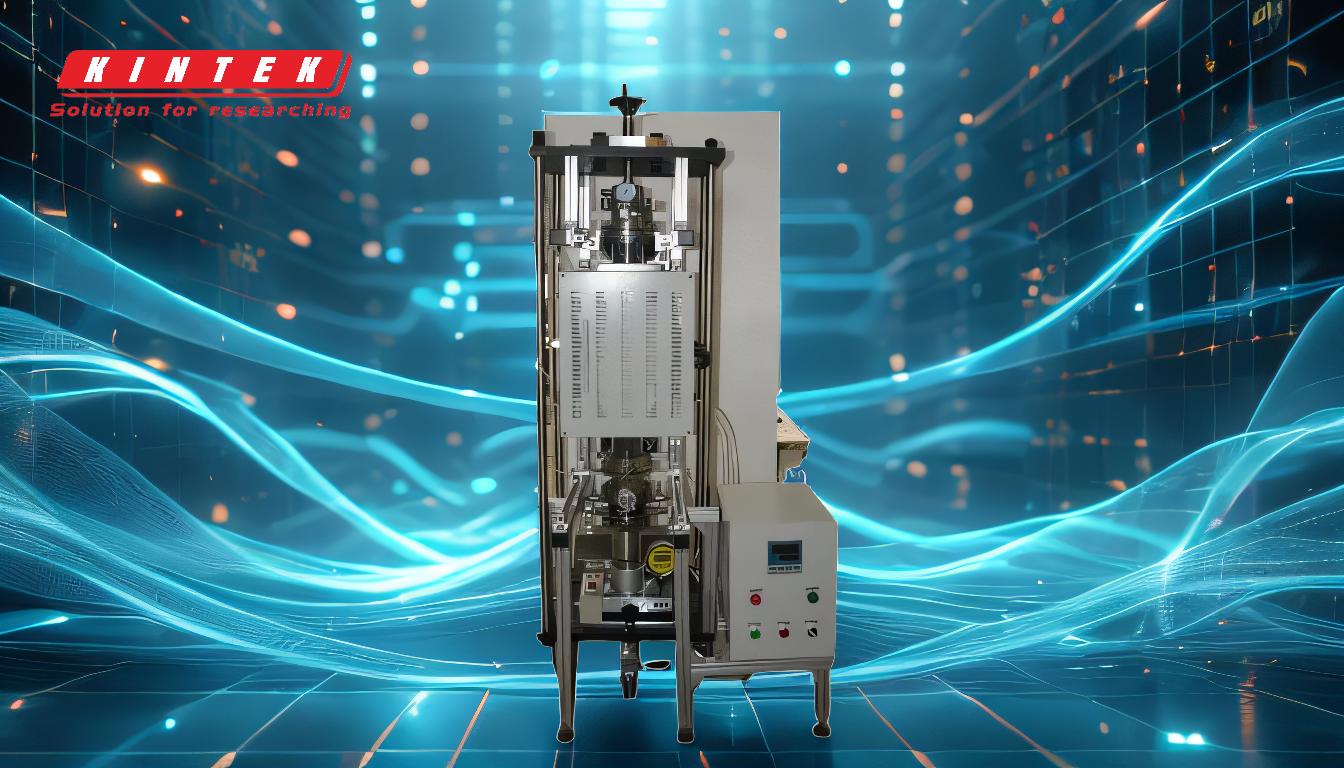
-
Annealing:
- Process: Heating the metal to a specific temperature, holding it there for a period, and then slowly cooling it.
- Purpose: To soften the metal, improve ductility, and relieve internal stresses.
- Applications: Used in manufacturing processes where metal needs to be more workable, such as in the production of wires or sheets.
-
Case Hardening:
- Process: Adding carbon or nitrogen to the surface of the metal to create a hard outer layer while maintaining a softer, more ductile core.
- Purpose: To increase surface hardness and wear resistance.
- Applications: Commonly used in gears, bearings, and other components that require a hard surface to withstand friction and wear.
-
Precipitation Strengthening:
- Process: Heating the metal to a temperature where certain elements dissolve, followed by rapid cooling and aging to form fine particles that strengthen the material.
- Purpose: To increase strength and hardness without significantly reducing ductility.
- Applications: Used in high-strength alloys, such as those found in aerospace components.
-
Tempering:
- Process: Reheating hardened steel to a temperature below its critical point, holding it, and then cooling it.
- Purpose: To reduce brittleness and improve toughness after hardening.
- Applications: Essential for tools and machinery parts that require a balance of hardness and toughness.
-
Carburizing:
- Process: Introducing carbon into the surface of low-carbon steel by heating it in a carbon-rich environment.
- Purpose: To increase surface hardness while maintaining a tough core.
- Applications: Used in automotive parts like crankshafts and camshafts.
-
Normalizing:
- Process: Heating the metal to a temperature above its critical range, holding it, and then cooling it in air.
- Purpose: To refine the grain structure, improve mechanical properties, and relieve internal stresses.
- Applications: Commonly used in the manufacturing of steel components to ensure uniformity in structure and properties.
-
Quenching:
- Process: Rapidly cooling the metal by immersing it in a liquid (water, oil, or brine) after heating it to a high temperature.
- Purpose: To increase hardness and strength by transforming the microstructure.
- Applications: Used in the production of high-strength tools and components.
-
Martensitic Transformation:
- Process: A rapid cooling process that transforms the microstructure of steel into martensite, a very hard and brittle form.
- Purpose: To achieve high hardness and strength.
- Applications: Used in the production of cutting tools, knives, and other high-strength applications.
Each of these heat treatment methods plays a crucial role in tailoring the properties of metals to meet specific application requirements. Understanding these processes allows for the selection of the appropriate method to achieve the desired material characteristics, ensuring optimal performance and longevity of the components.
Summary Table:
Method | Process | Purpose | Applications |
---|---|---|---|
Annealing | Heat, hold, and slowly cool metal | Soften metal, improve ductility, relieve stress | Wire, sheet production |
Case Hardening | Add carbon/nitrogen to surface | Increase surface hardness and wear resistance | Gears, bearings |
Precipitation Strengthening | Heat, rapid cool, and age metal | Increase strength and hardness | Aerospace components |
Tempering | Reheat hardened steel and cool | Reduce brittleness, improve toughness | Tools, machinery parts |
Carburizing | Heat in carbon-rich environment | Increase surface hardness, maintain tough core | Automotive parts (crankshafts, camshafts) |
Normalizing | Heat above critical range, cool in air | Refine grain structure, improve mechanical properties | Steel components |
Quenching | Rapidly cool in liquid (water, oil, brine) | Increase hardness and strength | High-strength tools, components |
Martensitic Transformation | Rapid cooling to form martensite | Achieve high hardness and strength | Cutting tools, knives |
Need help selecting the right heat treatment method for your materials? Contact our experts today!