Induction furnaces, while highly efficient for melting metals, come with several disadvantages that can impact their suitability for certain applications. One of the primary drawbacks is their lack of refining capacity, which means the charge materials must be free of oxides and of a known composition. Additionally, some alloying elements may be lost due to oxidation, necessitating their re-addition to the melt. These limitations can affect the overall efficiency and cost-effectiveness of using induction furnaces in metal melting processes.
Key Points Explained:
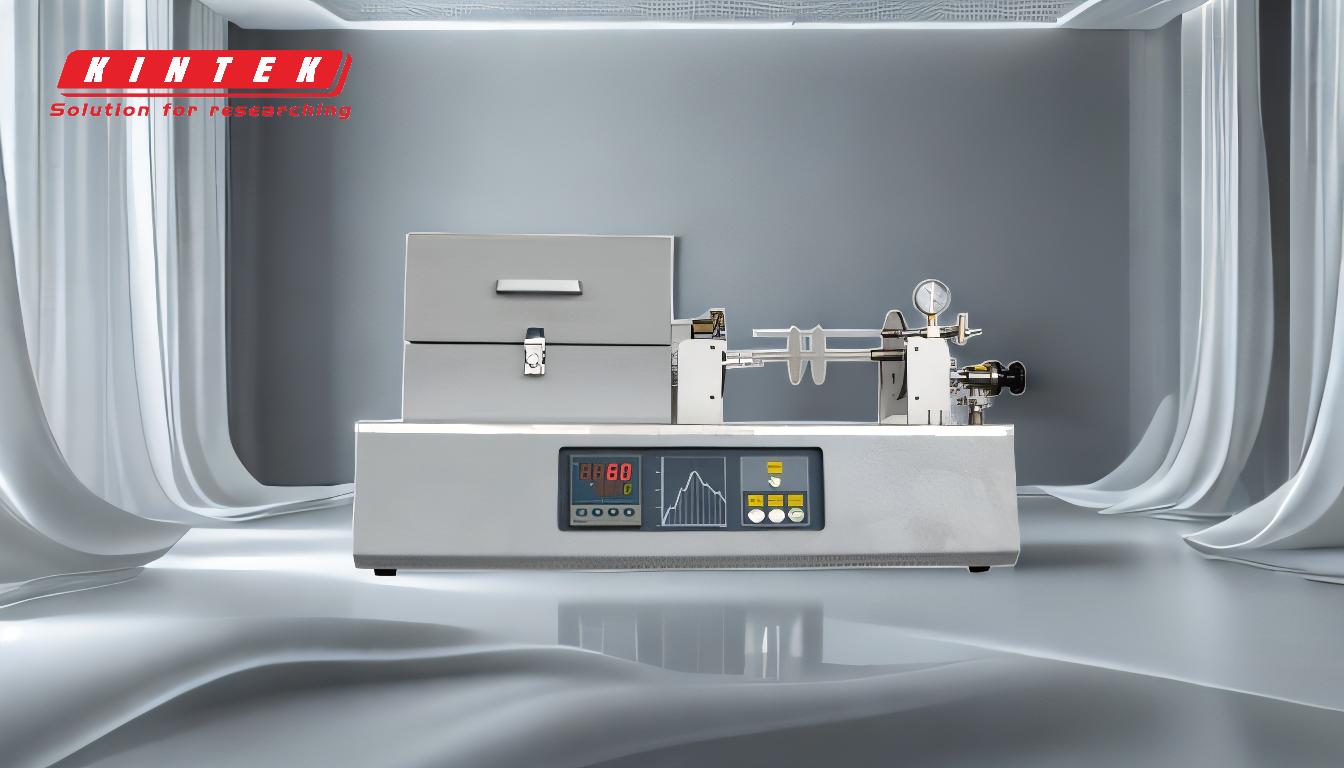
-
Lack of Refining Capacity:
- Induction furnaces do not have the capability to refine metals. This means that the charge materials used must already be free of oxides and other impurities. For industries requiring high-purity metals, this can be a significant limitation.
- The absence of refining capacity can lead to the need for additional processing steps, increasing both time and cost.
-
Requirement for Known Composition:
- The charge materials must be of a known composition to ensure the desired quality of the final product. This requirement can complicate the sourcing and preparation of materials, especially when dealing with complex alloys.
- Any deviation in the composition of the charge materials can result in inconsistencies in the final product, affecting its performance and reliability.
-
Loss of Alloying Elements:
- During the melting process, some alloying elements may be lost due to oxidation. This loss can alter the composition of the final product, potentially compromising its properties.
- To counteract this, these elements must be re-added to the melt, which can increase material costs and complicate the melting process.
-
Energy Efficiency and Cost:
- While induction furnaces are generally energy-efficient, the need for high-quality charge materials and the potential loss of alloying elements can offset these savings. The overall cost-effectiveness of using an induction furnace must be carefully evaluated based on specific application requirements.
- The initial investment in an igbt induction furnace can be high, and the operational costs associated with maintaining the required material quality can add to the total expense.
-
Operational Complexity:
- The need for precise control over the charge materials and the melting process can increase the operational complexity. Skilled personnel are required to manage these processes effectively, adding to labor costs.
- The potential for material loss and the need for re-addition of alloying elements can also introduce variability into the production process, requiring additional quality control measures.
In summary, while induction furnaces offer several advantages, including energy efficiency and precise temperature control, their disadvantages—such as the lack of refining capacity, the requirement for known composition, and the potential loss of alloying elements—must be carefully considered. These factors can impact the overall efficiency, cost, and suitability of induction furnaces for specific applications.
Summary Table:
Disadvantage | Impact |
---|---|
Lack of Refining Capacity | Requires high-purity charge materials; increases time and cost. |
Requirement for Known Composition | Complicates material sourcing; deviations affect product quality. |
Loss of Alloying Elements | Oxidation leads to material loss; re-addition increases costs. |
Energy Efficiency and Cost | High initial investment; operational costs may offset energy savings. |
Operational Complexity | Requires skilled personnel; variability may necessitate quality control. |
Need help choosing the right furnace for your application? Contact our experts today!