Furnace tubes are critical components in various types of furnaces, designed to withstand high temperatures, corrosive environments, and mechanical stress. They are typically made from materials like alumina, mullite, stainless steel, and quartz, depending on the specific application and operational requirements. These materials are chosen for their thermal stability, resistance to chemical corrosion, and mechanical strength. For instance, dense alumina or mullite tubes are ideal for high-pressure or reactive atmospheres, while stainless steel and quartz are preferred for their durability and versatility in different thermal environments. Understanding the material properties and their suitability for specific furnace applications is essential for optimizing performance and longevity.
Key Points Explained:
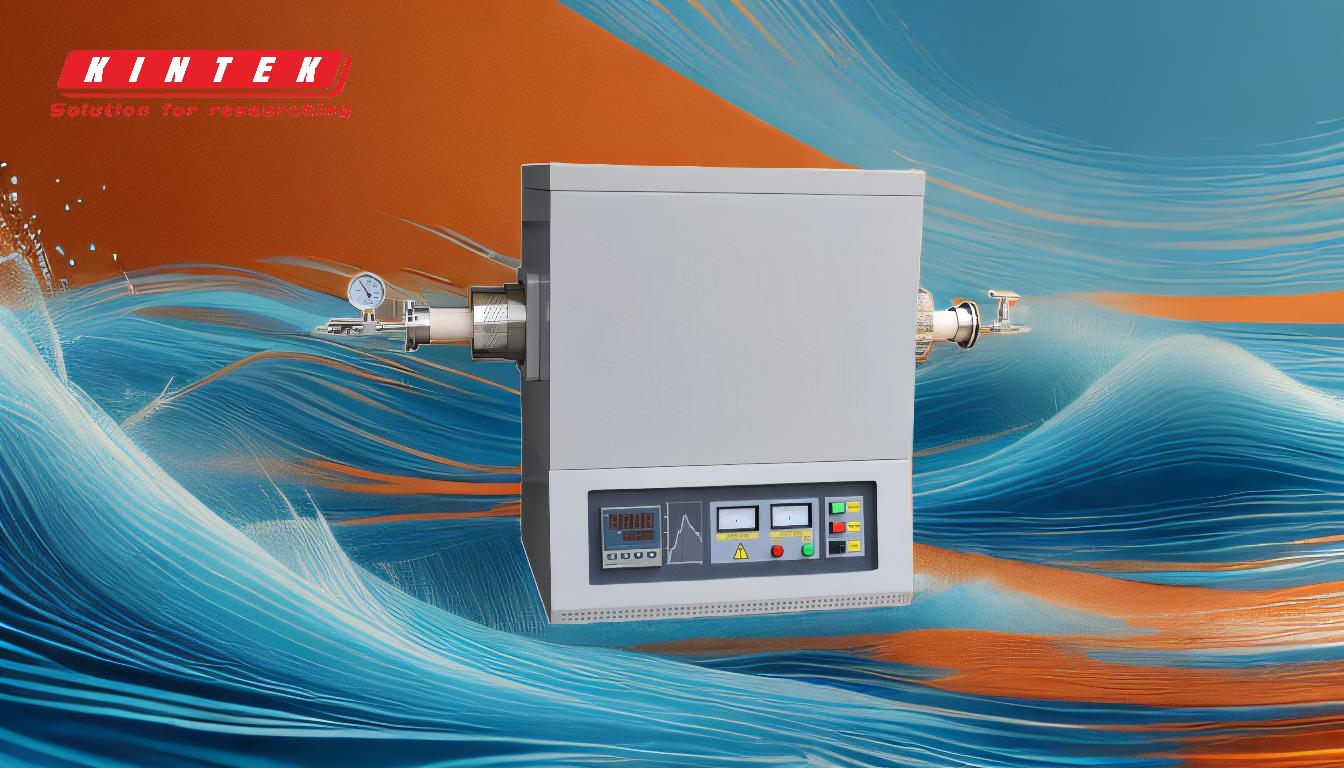
-
Materials Used in Furnace Tubes:
- Alumina and Mullite Tubes: These are dense ceramic materials known for their high thermal stability and resistance to chemical corrosion. They are commonly used in applications involving internal pressure or reactive atmospheres, such as in hydrogen furnaces or environments with corrosive gases. Their dense structure prevents gas permeation and ensures structural integrity under high temperatures.
- Stainless Steel Tubes: Stainless steel is widely used in furnace tubes due to its excellent mechanical strength, resistance to oxidation, and ability to withstand high temperatures. It is particularly suitable for sintering processes, such as hydrogen furnace sintering, where high-performance alloys like tungsten carbide are processed. Stainless steel tubes are also used in box-type atmosphere furnaces due to their corrosion resistance.
- Quartz Tubes: Quartz is favored for its transparency to infrared radiation and its ability to withstand rapid temperature changes. It is often used in laboratory tube furnaces where precise temperature control and visibility are required. Quartz tubes are also chemically inert, making them suitable for processes involving reactive gases.
-
Applications and Suitability:
- High-Pressure and Reactive Atmospheres: Dense alumina and mullite tubes are recommended for applications where the furnace operates under internal pressure or in reactive atmospheres. Their dense structure prevents gas leakage and ensures safety and efficiency.
- Sintering Processes: Stainless steel tubes are commonly used in sintering processes, such as hydrogen furnace sintering, where high temperatures and controlled atmospheres are required. They are also suitable for processing high-performance alloys and ceramic/metallic compositions.
- Laboratory and Precision Applications: Quartz tubes are ideal for laboratory tube furnaces, where precise temperature control and visibility are essential. They are also used in processes that require rapid heating or cooling.
-
Design and Construction:
- Furnace Shell and Structure: The furnace shell, such as in box furnaces, is typically constructed from high-quality steel plates and angle steel, welded together for durability. The furnace body of a box-type atmosphere furnace is often made from high-temperature alloy steel or stainless steel, providing resistance to high temperatures and corrosion.
- Integration of Components: Furnace tubes are often integrated with other components, such as flanges, electrode holes, and observation holes, all made of stainless steel. This ensures a seamless and robust design that can withstand operational stresses.
-
Operational Considerations:
- Temperature Control: Laboratory tube furnaces use heating coils and thermocouples for precise temperature control. The choice of tube material, such as quartz, ensures that the furnace can handle rapid temperature changes without compromising performance.
- Material Flow and Processing: Rotary tube furnaces are designed for granular or particulate materials that flow at high temperatures. Materials that become sticky at high temperatures are not suitable for these furnaces, highlighting the importance of selecting the right tube material for specific applications.
By carefully selecting the appropriate material for furnace tubes based on the operational requirements, users can ensure optimal performance, longevity, and safety in various high-temperature applications.
Summary Table:
Material | Properties | Applications |
---|---|---|
Alumina/Mullite | High thermal stability, resistance to chemical corrosion, dense structure | High-pressure or reactive atmospheres (e.g., hydrogen furnaces, corrosive gas environments) |
Stainless Steel | Excellent mechanical strength, oxidation resistance, high-temperature durability | Sintering processes (e.g., hydrogen furnace sintering), box-type atmosphere furnaces |
Quartz | Transparency to infrared radiation, rapid temperature change resistance | Laboratory tube furnaces, processes requiring precise temperature control and rapid heating/cooling |
Need help selecting the right furnace tube material for your application? Contact our experts today!