Maintaining hydraulic systems is crucial for ensuring their longevity, efficiency, and safety. Proper maintenance involves regular inspections, fluid management, component checks, and adherence to operational best practices. By following a structured maintenance routine, potential issues can be identified early, preventing costly repairs and downtime. Key aspects include monitoring hydraulic fluid quality, inspecting hoses and seals, ensuring proper filtration, and addressing leaks promptly. Additionally, understanding the system's operating conditions and scheduling preventive maintenance can significantly enhance performance and reliability.
Key Points Explained:
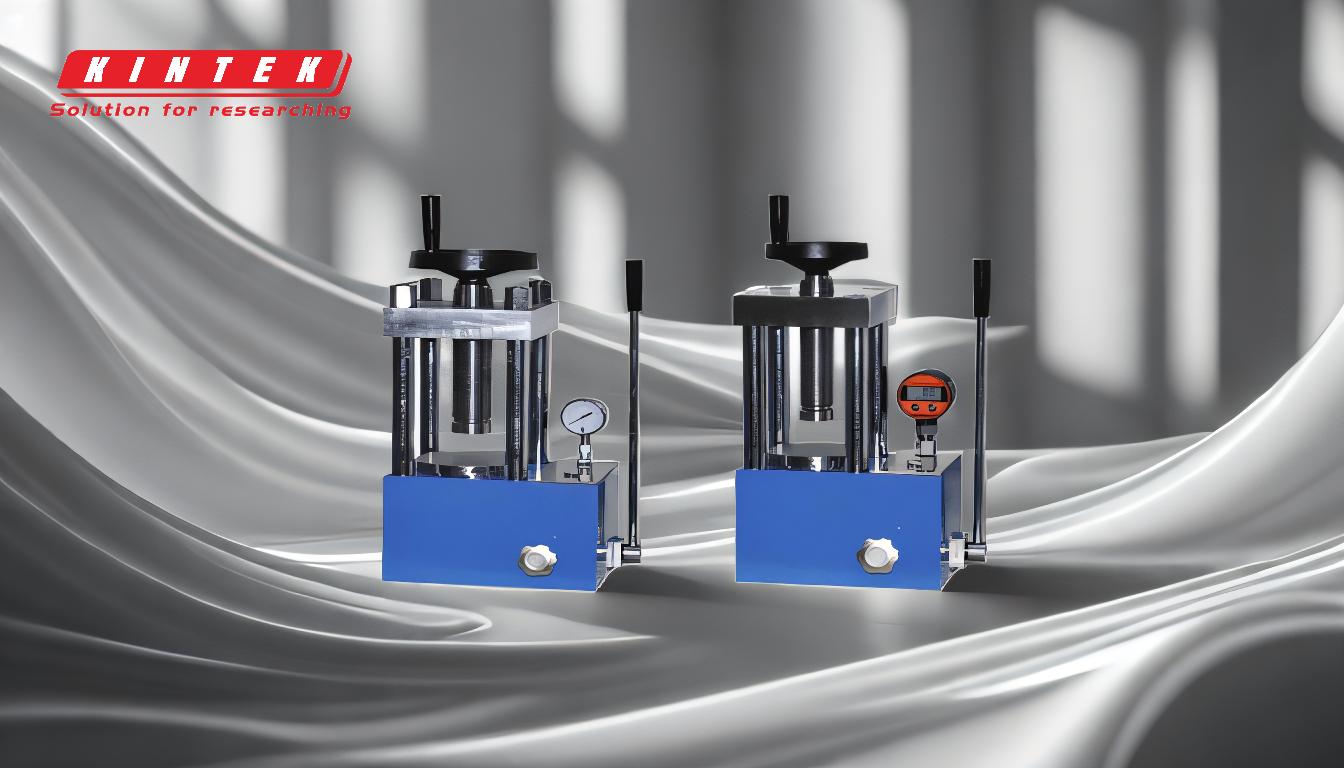
-
Regular Fluid Checks and Maintenance
- Hydraulic fluid is the lifeblood of the system, and its quality directly impacts performance.
- Regularly check fluid levels and top up as needed to avoid air ingress and cavitation.
- Monitor fluid contamination by using particle counters or visual inspections. Contaminated fluid can lead to component wear and system failure.
- Replace hydraulic fluid at recommended intervals or when it shows signs of degradation, such as discoloration or increased viscosity.
- Use the correct type of hydraulic fluid specified by the manufacturer to ensure compatibility with system components.
-
Inspection of Hoses, Seals, and Fittings
- Inspect hydraulic hoses for cracks, abrasions, or bulges, as these can lead to leaks or bursts.
- Check seals and O-rings for wear or damage, as compromised seals can cause fluid leaks and reduce system efficiency.
- Tighten loose fittings and connections to prevent leaks and ensure proper pressure levels.
- Replace damaged components immediately to avoid further system damage.
-
Filtration System Maintenance
- Hydraulic systems rely on filters to remove contaminants from the fluid.
- Regularly inspect and replace filters according to the manufacturer's recommendations or when pressure differentials indicate clogging.
- Ensure that the filtration system is appropriately sized for the system's flow rate and contamination levels.
- Clean or replace breather caps and air filters to prevent external contaminants from entering the system.
-
Leak Detection and Prevention
- Hydraulic fluid leaks are a common issue that can lead to reduced efficiency, environmental hazards, and increased operating costs.
- Regularly inspect the system for visible leaks, especially around joints, seals, and hoses.
- Use leak detection tools, such as ultrasonic detectors, to identify internal or hard-to-find leaks.
- Address leaks promptly by repairing or replacing faulty components.
-
Temperature and Pressure Monitoring
- Excessive heat can degrade hydraulic fluid and damage system components.
- Monitor system temperature using sensors and ensure that cooling systems, such as heat exchangers or fans, are functioning correctly.
- Maintain proper operating pressure levels to prevent overloading components and ensure smooth operation.
- Use pressure gauges and relief valves to monitor and control system pressure.
-
Preventive Maintenance Scheduling
- Develop a preventive maintenance schedule based on the system's operating hours, workload, and manufacturer recommendations.
- Regularly inspect and service critical components, such as pumps, valves, and actuators, to identify wear or damage early.
- Keep detailed maintenance records to track the system's performance and identify recurring issues.
- Train operators and maintenance personnel on proper system operation and maintenance procedures.
-
System Flushing and Cleaning
- Over time, hydraulic systems can accumulate sludge, varnish, and other deposits that reduce efficiency.
- Periodically flush the system with a cleaning solution to remove contaminants and restore performance.
- Ensure that the flushing process is thorough and that all contaminants are removed before refilling with fresh hydraulic fluid.
-
Operational Best Practices
- Avoid overloading the system, as this can lead to excessive wear and component failure.
- Operate the system within its specified temperature and pressure ranges.
- Use proper start-up and shut-down procedures to minimize stress on components.
- Regularly inspect and maintain auxiliary components, such as reservoirs, accumulators, and coolers, to ensure overall system health.
By following these maintenance requirements, hydraulic systems can operate efficiently and reliably, minimizing downtime and extending their service life. A proactive approach to maintenance not only reduces operational costs but also enhances safety and performance.
Summary Table:
Maintenance Task | Key Actions |
---|---|
Fluid Checks | Monitor levels, contamination, and replace fluid as needed. |
Hose, Seal, and Fitting Checks | Inspect for damage, tighten connections, and replace worn components. |
Filtration System | Replace filters, clean breather caps, and ensure proper sizing. |
Leak Detection | Inspect for leaks, use ultrasonic tools, and repair promptly. |
Temperature & Pressure Monitoring | Monitor heat levels, ensure cooling systems work, and maintain proper pressure. |
Preventive Maintenance | Schedule regular inspections, service critical components, and keep records. |
System Flushing | Periodically flush the system to remove contaminants and restore performance. |
Operational Best Practices | Avoid overloading, follow start-up/shut-down procedures, and maintain auxiliary components. |
Ensure your hydraulic systems run smoothly—contact our experts today for tailored maintenance solutions!