Thin film fabrication involves a variety of methods that can be broadly categorized into chemical and physical deposition techniques. These methods enable precise control over the thickness, composition, and properties of the films, making them suitable for a wide range of applications, from semiconductors to flexible electronics. The primary techniques include physical vapor deposition (PVD), chemical vapor deposition (CVD), and solution-based methods like spin coating and dip coating. Each method has its own advantages and is chosen based on the specific requirements of the application, such as film uniformity, material compatibility, and scalability.
Key Points Explained:
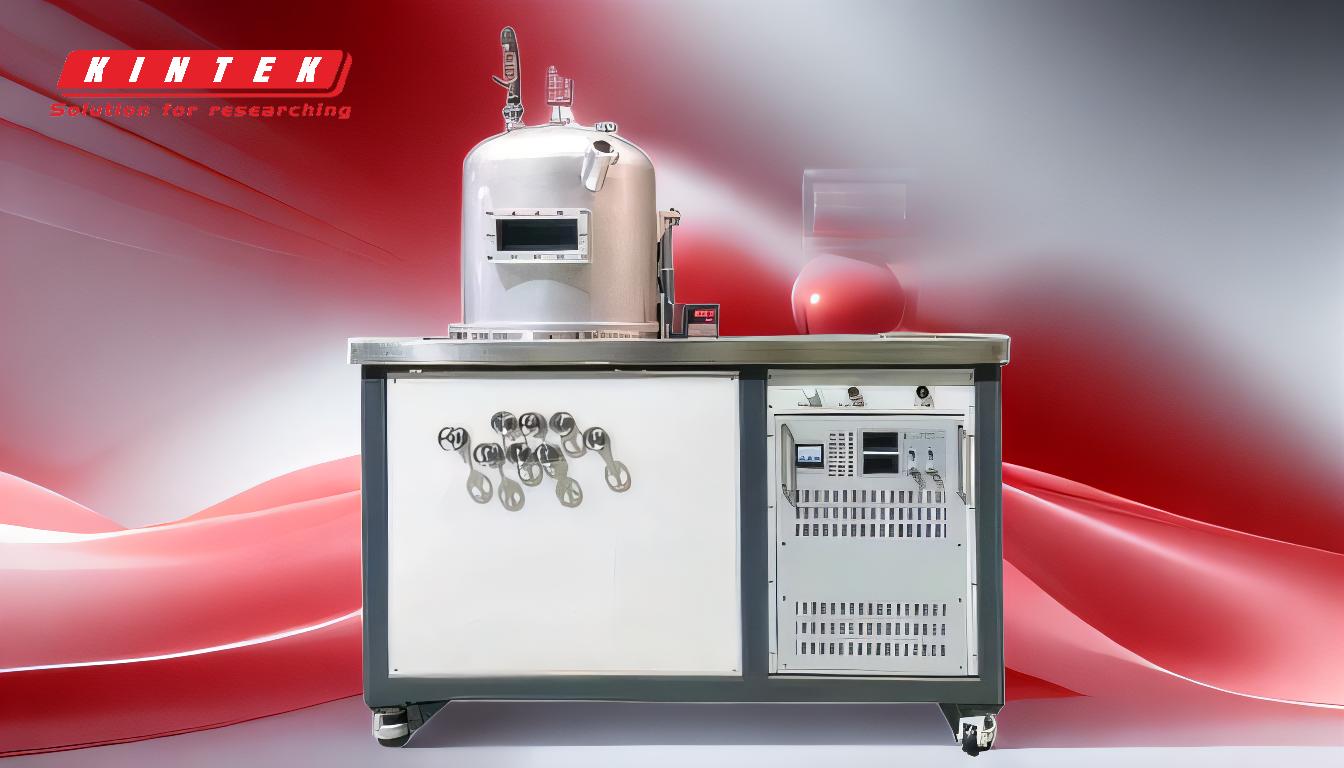
-
Physical Vapor Deposition (PVD):
- Sputtering: This technique involves bombarding a target material with high-energy ions to eject atoms, which then deposit onto a substrate. It is widely used for creating uniform and high-quality thin films, especially in the semiconductor industry.
- Thermal Evaporation: In this method, the material is heated in a vacuum until it vaporizes and then condenses onto a substrate. It is commonly used for depositing metals and simple compounds.
- Electron Beam Evaporation: Similar to thermal evaporation, but the material is heated using an electron beam, allowing for higher melting point materials to be deposited.
- Molecular Beam Epitaxy (MBE): This is a highly controlled form of PVD used for growing high-purity, single-crystal thin films, particularly in the fabrication of semiconductor devices.
- Pulsed Laser Deposition (PLD): A laser is used to vaporize material from a target, which then deposits onto a substrate. This method is useful for complex materials like oxides and superconductors.
-
Chemical Vapor Deposition (CVD):
- Chemical Vapor Deposition (CVD): This process involves the reaction of gaseous precursors on a heated substrate to form a solid thin film. It is widely used for depositing high-purity, uniform films, such as silicon dioxide and silicon nitride.
- Plasma-Enhanced CVD (PECVD): This variant of CVD uses plasma to enhance the chemical reaction, allowing for lower deposition temperatures and faster growth rates.
- Atomic Layer Deposition (ALD): ALD is a precise form of CVD where the film is grown one atomic layer at a time, providing excellent control over thickness and uniformity. It is ideal for applications requiring ultra-thin films, such as in microelectronics.
-
Solution-Based Methods:
- Spin Coating: A liquid precursor is applied to a substrate, which is then spun at high speed to spread the material into a thin, uniform layer. This method is commonly used for creating polymer thin films in applications like flexible solar cells and OLEDs.
- Dip Coating: The substrate is dipped into a liquid precursor and then withdrawn at a controlled speed, leaving a thin film on the surface. This method is simple and cost-effective, suitable for large-area coatings.
- Sol-Gel: This involves the transition of a solution (sol) into a gel-like state, which is then dried and annealed to form a thin film. It is used for creating oxide films and is particularly useful for coatings on complex geometries.
-
Other Methods:
- Electroplating: This involves the deposition of a metal film onto a conductive substrate using an electric current. It is commonly used for creating metallic coatings and is cost-effective for large-scale production.
- Langmuir-Blodgett Film Formation: This technique involves transferring monolayers of amphiphilic molecules from a liquid surface onto a solid substrate. It is used for creating highly ordered thin films for research applications.
- Drop Casting: A simple method where a solution is dropped onto a substrate and allowed to dry, forming a thin film. It is less controlled but useful for quick prototyping.
Each of these methods has its own set of advantages and limitations, and the choice of technique depends on factors such as the desired film properties, substrate material, and application requirements. For example, PVD methods are preferred for high-purity, uniform films in semiconductor manufacturing, while solution-based methods like spin coating are ideal for creating polymer films in flexible electronics.
Summary Table:
Method | Key Techniques | Applications |
---|---|---|
Physical Vapor Deposition (PVD) | Sputtering, Thermal Evaporation, Electron Beam Evaporation, MBE, PLD | High-purity, uniform films for semiconductors and superconductors |
Chemical Vapor Deposition (CVD) | CVD, Plasma-Enhanced CVD (PECVD), Atomic Layer Deposition (ALD) | High-purity films like silicon dioxide and silicon nitride for microelectronics |
Solution-Based Methods | Spin Coating, Dip Coating, Sol-Gel | Polymer films for flexible electronics and large-area coatings |
Other Methods | Electroplating, Langmuir-Blodgett Film Formation, Drop Casting | Metallic coatings, research films, and quick prototyping |
Ready to choose the best thin film fabrication method for your project? Contact our experts today for tailored solutions!