Brazing, particularly vacuum brazing, is a versatile joining process with significant applications across various industries, including aerospace, automotive, and medical sectors. This process is highly valued for its ability to create strong, clean, and precise joints, making it ideal for manufacturing complex components that require durability, resistance to thermal distortion, and high performance. In the aerospace industry, vacuum brazing is extensively used to manufacture critical components such as honeycomb sealing rings, engine fuel main pipes, and stainless steel heat exchangers. These applications highlight the importance of brazing in producing reliable and efficient aerospace systems. Additionally, vacuum brazing's cost-effectiveness and suitability for high-volume production further enhance its appeal in industrial manufacturing.
Key Points Explained:
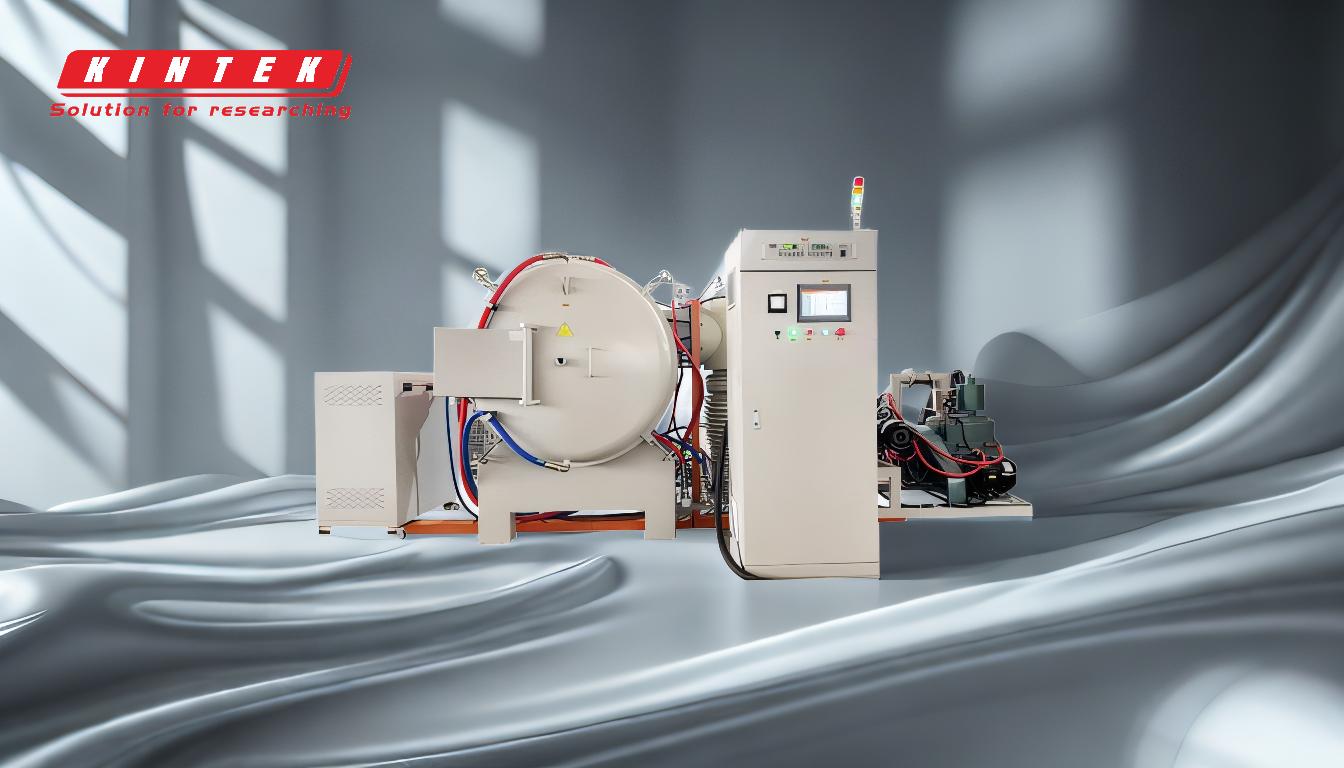
-
Applications in Aerospace Industry:
- Honeycomb Sealing Rings: Vacuum brazing is used to manufacture honeycomb sealing rings, which are essential components in aero engines. These rings are constructed by joining a ring piece and a honeycomb sandwich core, ensuring a strong and durable seal.
- Engine Fuel Main Pipes: The process is also employed to construct engine fuel main pipes, which involve joining a main pipe with multiple branch pipes and nozzles. This ensures a reliable fuel delivery system within the engine.
- Stainless Steel Heat Exchangers: Vacuum brazing is crucial for assembling stainless steel heat exchangers, which consist of more than 300 stainless steel tubes, partitions, and casings. These heat exchangers are vital for maintaining optimal engine temperatures.
-
Importance of Vacuum Heat Treatment:
- Aircraft Structures: Vacuum heat treatment is critical for enhancing the properties of aerospace components. The choice of alloy and the specific type of vacuum heat treatment (such as age hardening, natural aging, and artificial aging) are essential for achieving the desired grain structure, which directly impacts the aircraft's lifespan.
- NASA Standards: NASA has defined nine types of vacuum heat treatments, emphasizing their importance in building aircraft with higher strength materials, better functionality, fewer repairs, and longer lifespans.
-
Benefits of Vacuum Brazing:
- High-Quality Joints: Vacuum brazing produces high-quality, strong, and clean joints, making it suitable for precision components that require durability and resistance to thermal distortion.
- Cost-Effectiveness: The process is cost-effective and suitable for high-volume production, making it an attractive option for industries that require large quantities of reliable components.
-
Versatility Across Industries:
- Automotive and Medical Sectors: Beyond aerospace, vacuum brazing is also widely used in the automotive and medical industries. Its ability to produce precise and durable joints makes it ideal for manufacturing components that require high performance and reliability.
In summary, vacuum brazing is a critical process in the manufacturing of high-performance components across various industries. Its applications in the aerospace sector, particularly in the production of honeycomb sealing rings, engine fuel main pipes, and stainless steel heat exchangers, underscore its importance in ensuring the reliability and efficiency of aerospace systems. The process's ability to produce strong, clean, and precise joints, combined with its cost-effectiveness and suitability for high-volume production, makes it an invaluable tool in modern industrial manufacturing.
Summary Table:
Industry | Applications |
---|---|
Aerospace | Honeycomb sealing rings, engine fuel main pipes, stainless steel heat exchangers |
Automotive | High-performance components requiring durability and precision |
Medical | Reliable and precise joints for medical devices |
General Manufacturing | Cost-effective, high-volume production of durable components |
Learn how brazing can enhance your manufacturing process—contact our experts today!