Brazing is a versatile joining process that utilizes various heating techniques to achieve strong and durable bonds between materials. The four primary heating techniques used in brazing are torch brazing, furnace brazing, induction brazing, and dip brazing. Each method has unique advantages and is suited for specific applications, depending on factors such as material type, joint design, and production volume. Torch brazing is manual and flexible, furnace brazing is ideal for high-volume production, induction brazing offers precision and speed, and dip brazing is effective for complex geometries. These techniques ensure efficient heat application, enabling the filler metal to flow and create robust joints.
Key Points Explained:
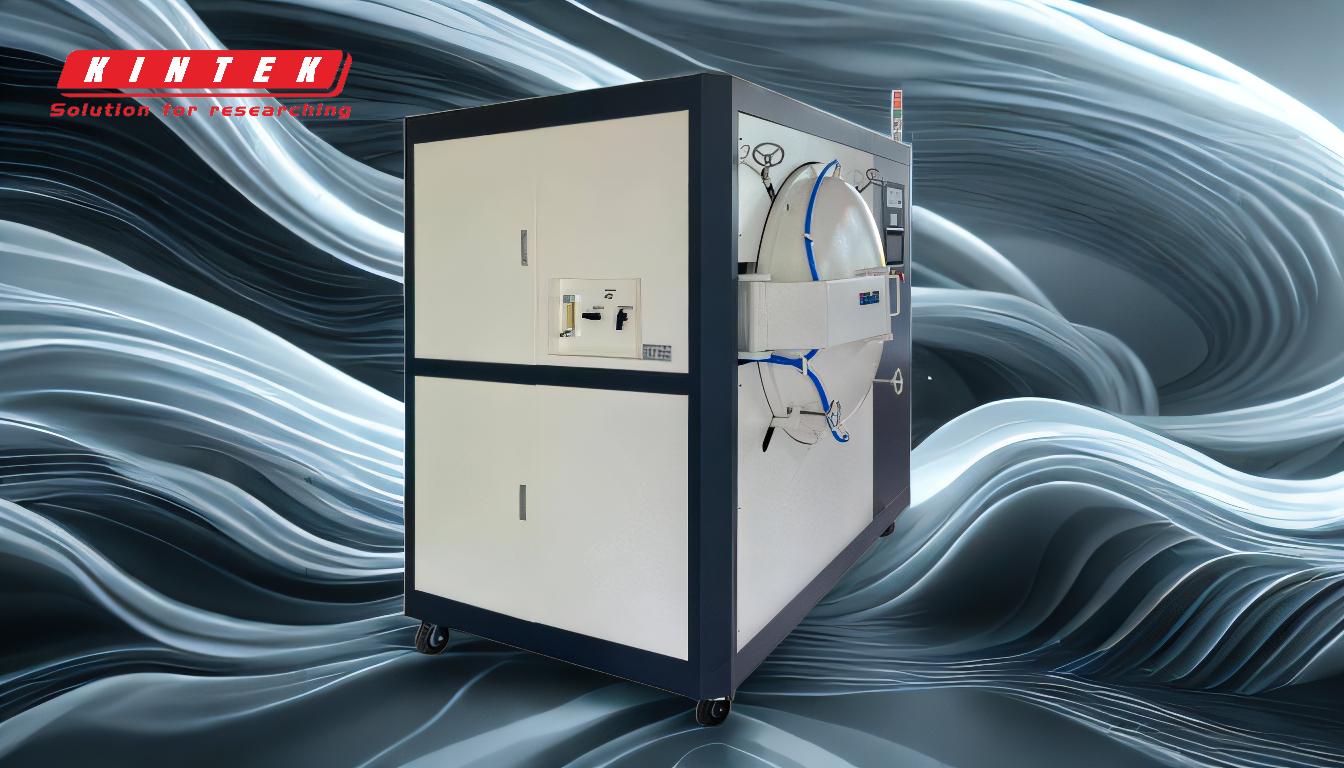
-
Torch Brazing:
- Torch brazing involves using a handheld torch to apply heat directly to the joint area. The heat source can be a gas flame (e.g., oxy-acetylene, propane, or natural gas).
- This method is highly flexible and suitable for small-scale or repair work. It allows for precise control over the heating process, making it ideal for intricate or hard-to-reach joints.
- The operator must carefully manage the heat to avoid overheating or underheating the materials, ensuring proper flow of the filler metal.
-
Furnace Brazing:
- Furnace brazing involves placing the assembled parts into a furnace, where they are heated uniformly to the brazing temperature. The furnace can operate in various atmospheres, such as exothermic, hydrogen, argon, or vacuum, to prevent oxidation and ensure clean joints.
- This technique is highly efficient for high-volume production and is suitable for complex assemblies with multiple joints. It provides consistent heating and excellent control over the brazing environment.
- Furnace brazing is often used in industries like aerospace and automotive, where precision and repeatability are critical.
-
Induction Brazing:
- Induction brazing uses electromagnetic induction to generate heat within the materials. An induction coil creates an alternating magnetic field, which induces eddy currents in the conductive base materials, heating them rapidly.
- This method is fast, energy-efficient, and provides localized heating, minimizing thermal distortion. It is ideal for applications requiring high precision and repeatability, such as electronics and medical devices.
- Induction brazing is also suitable for joining dissimilar materials, as it allows precise control over the heat application.
-
Dip Brazing:
- Dip brazing involves immersing the assembled parts into a molten salt bath or a bath of molten filler metal. The heat from the bath melts the filler metal, which flows into the joints by capillary action.
- This technique is particularly effective for complex geometries and assemblies with multiple joints, as the entire part is heated uniformly. It also provides excellent oxidation protection due to the molten salt or metal bath.
- Dip brazing is commonly used in industries like plumbing and HVAC, where strong, leak-proof joints are essential.
Each of these heating techniques offers distinct advantages, making them suitable for different applications. By selecting the appropriate method based on the specific requirements of the project, manufacturers can achieve high-quality, reliable brazed joints.
Summary Table:
Technique | Key Advantages | Best Applications |
---|---|---|
Torch Brazing | Flexible, manual, precise control over heat | Small-scale or repair work, intricate joints |
Furnace Brazing | Uniform heating, high-volume production, clean joints | Aerospace, automotive, complex assemblies |
Induction Brazing | Fast, energy-efficient, localized heating, minimal distortion | Electronics, medical devices, dissimilar materials |
Dip Brazing | Uniform heating, effective for complex geometries, oxidation protection | Plumbing, HVAC, assemblies with multiple joints |
Need help choosing the right brazing technique for your project? Contact our experts today for personalized advice!