Cold working and hot working are two fundamental metal forming processes, each with distinct advantages and disadvantages. Cold working involves shaping metals below their recrystallization temperature, which enhances strength and hardness but may reduce ductility. Hot working, on the other hand, occurs above the recrystallization temperature, allowing for easier deformation and better ductility but often resulting in lower strength. The choice between these methods depends on the desired material properties, cost considerations, and the specific application. Below, we explore the key advantages and disadvantages of cold working compared to hot working.
Key Points Explained:
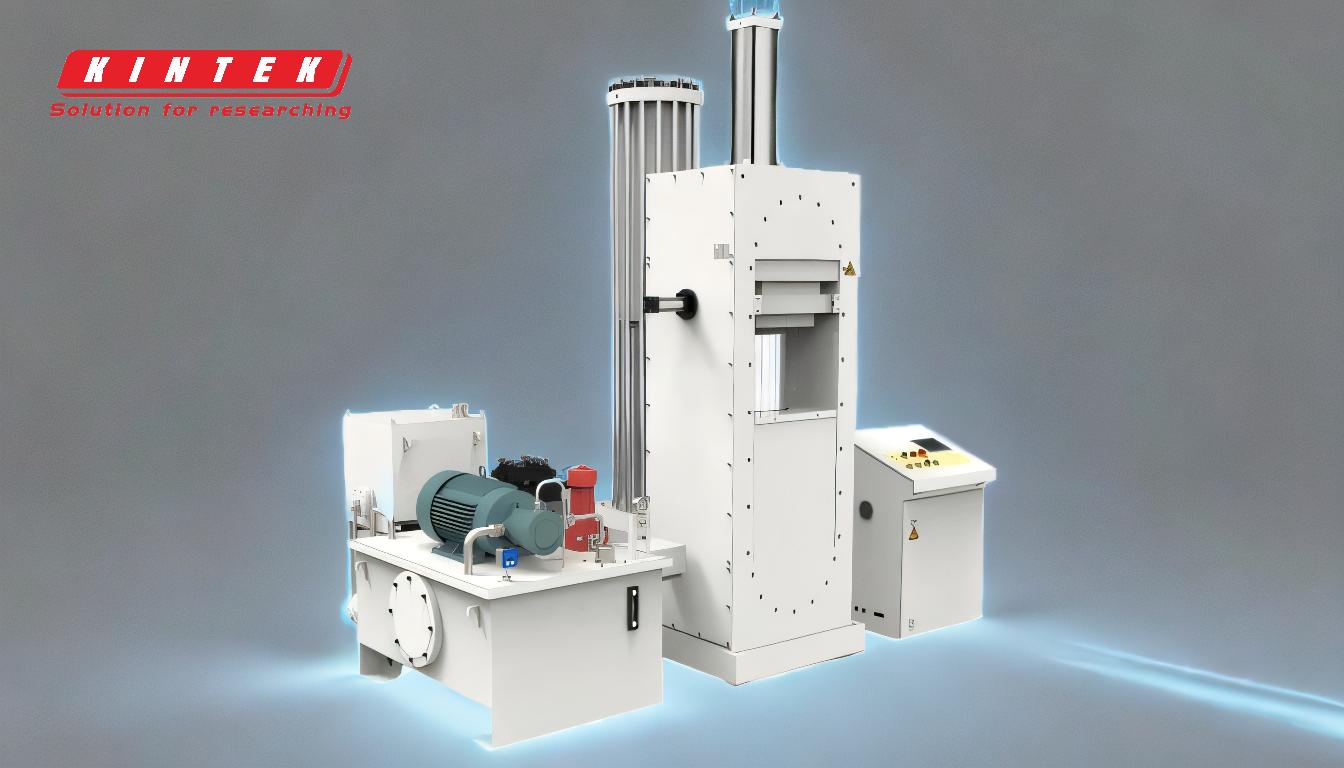
-
Advantages of Cold Working:
-
Improved Mechanical Properties:
- Cold working increases the strength and hardness of metals due to strain hardening. This makes the material more suitable for applications requiring high strength.
-
Better Surface Finish:
- The process results in a smoother and more precise surface finish, which is often desirable for aesthetic or functional purposes.
-
Dimensional Accuracy:
- Cold working allows for tighter tolerances and more precise control over dimensions, making it ideal for applications requiring high precision.
-
No Heating Required:
- Since cold working is performed at room temperature, it eliminates the need for heating, reducing energy consumption and costs associated with high-temperature processing.
-
Improved Mechanical Properties:
-
Disadvantages of Cold Working:
-
Reduced Ductility:
- The process significantly reduces the ductility of the metal, making it more brittle and prone to cracking under stress.
-
Higher Force Requirements:
- Cold working requires more force and energy to deform the metal compared to hot working, which can increase machinery wear and tear.
-
Limited Shape Complexity:
- The process is less effective for forming complex shapes, as the metal's reduced ductility limits its ability to undergo extensive deformation.
-
Residual Stresses:
- Cold working can introduce residual stresses in the material, which may lead to distortion or failure over time.
-
Reduced Ductility:
-
Advantages of Hot Working:
-
Enhanced Ductility:
- Hot working allows metals to be deformed more easily, making it suitable for shaping complex geometries and large components.
-
Lower Force Requirements:
- The process requires less force compared to cold working, reducing the strain on machinery and energy consumption.
-
Grain Refinement:
- Hot working can refine the grain structure of the metal, improving its mechanical properties and overall performance.
-
Elimination of Residual Stresses:
- The high temperatures involved in hot working help relieve internal stresses, resulting in a more stable and uniform material.
-
Enhanced Ductility:
-
Disadvantages of Hot Working:
-
Lower Strength and Hardness:
- Metals processed through hot working generally have lower strength and hardness compared to cold-worked metals.
-
Poor Surface Finish:
- The high temperatures can lead to oxidation and scaling, resulting in a rougher surface finish that may require additional processing.
-
Dimensional Inaccuracy:
- Hot working is less precise, often resulting in wider tolerances and less control over final dimensions.
-
Energy Consumption:
- The need to heat the metal to high temperatures increases energy consumption and operational costs.
-
Lower Strength and Hardness:
-
Application Considerations:
-
Material Selection:
- The choice between cold and hot working depends on the material's properties and the desired end-use characteristics. For example, cold working is preferred for high-strength applications, while hot working is better suited for complex shapes.
-
Cost and Efficiency:
- Cold working may be more cost-effective for small-scale production or when high precision is required, whereas hot working is often more efficient for large-scale manufacturing.
-
Environmental Impact:
- Cold working has a lower environmental impact due to the absence of high-temperature processing, making it a more sustainable option in some cases.
-
Material Selection:
In conclusion, both cold working and hot working have their unique advantages and disadvantages, and the choice between them depends on the specific requirements of the application. Cold working offers improved strength, precision, and surface finish but at the cost of reduced ductility and higher force requirements. Hot working, on the other hand, provides better ductility and easier deformation but may result in lower strength and a rougher surface finish. Understanding these trade-offs is crucial for selecting the most appropriate metal forming process.
Summary Table:
Aspect | Cold Working | Hot Working |
---|---|---|
Strength & Hardness | Increased due to strain hardening | Generally lower |
Ductility | Reduced, making the metal more brittle | Enhanced, allowing for easier deformation |
Surface Finish | Smoother and more precise | Rougher due to oxidation and scaling |
Dimensional Accuracy | Tighter tolerances and better precision | Less precise, wider tolerances |
Energy Consumption | Lower, as no heating is required | Higher due to high-temperature processing |
Shape Complexity | Limited due to reduced ductility | Better suited for complex shapes |
Residual Stresses | Can introduce residual stresses | Eliminates residual stresses |
Need help choosing the right metal forming process? Contact our experts today for tailored solutions!