Crucibles are widely used in melting metals, alloys, glass, and ceramics due to their versatility, ease of operation, and ability to handle small batches. However, they also come with certain drawbacks, such as high energy consumption, low efficiency, and potential contamination issues. This analysis explores the advantages and disadvantages of crucibles, focusing on their operational efficiency, maintenance, cost-effectiveness, and suitability for specific applications. Key points include their ability to quickly change alloys, low oxidation losses, and compact size, as well as challenges like high emissions, energy inefficiency, and material limitations.
Key Points Explained:
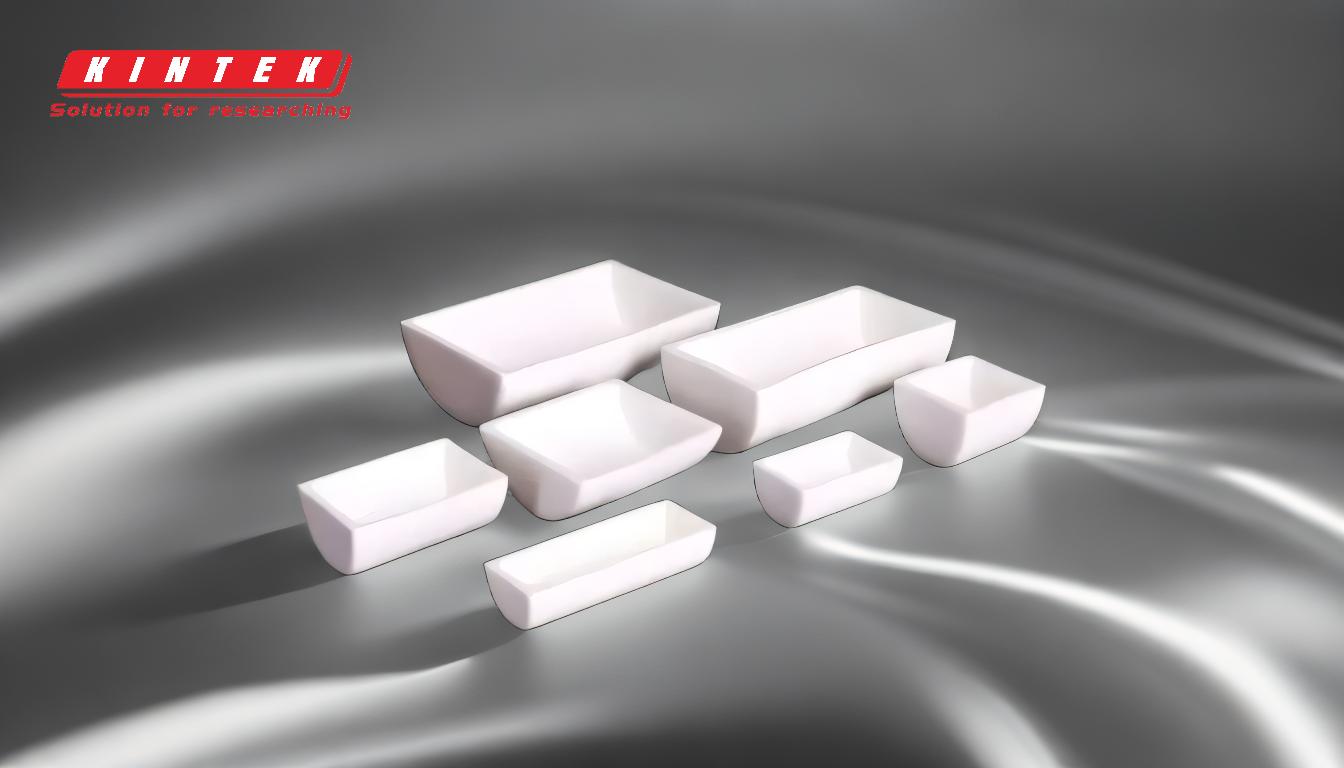
-
Versatility in Melting Various Materials
- Crucibles can melt a wide range of materials, including metals (e.g., aluminum, zinc), alloys, glass, and ceramics.
- They are suitable for small-scale or laboratory use due to their compact size.
- This versatility makes them ideal for applications requiring precise temperature control and high melting points.
-
Ease of Operation and Maintenance
- Crucible furnaces are user-friendly and do not require extensive training or specialized skills.
- Maintenance costs are relatively low, making them cost-effective for small-scale operations.
- The ability to treat the melt directly in the crucible simplifies processes like alloy replacement and material treatment.
-
Quick Alloy Change and Low Oxidation Losses
- Crucibles allow for rapid switching between different alloys, which is beneficial for applications requiring frequent material changes.
- Low oxidation losses ensure that the quality of the melt is preserved, reducing material waste.
-
High Energy Consumption and Low Efficiency
- One of the major disadvantages of crucible furnaces is their low efficiency, often as low as 12%.
- High energy consumption makes them less economical compared to other furnace types, especially for large-scale operations.
-
Emissions and Environmental Impact
- Traditional crucible furnaces can produce high emissions, contributing to environmental pollution.
- Electric crucible furnaces offer a solution by nearly eliminating emissions, but they come with increased fuel costs.
-
Material Contamination and Scaling Issues
- Steel crucibles, while suitable for melting metals like aluminum and zinc, may experience flaking (scaling) of the interior surface.
- This can contaminate the melt and thin the crucible walls, reducing its lifespan. Coating the crucible with materials like marcote-7 can mitigate this issue.
-
Size Limitations and Batch Processing
- Crucible furnaces are typically limited in size, making them less suitable for large-scale industrial applications.
- They are better suited for small batches, which can be a limitation for high-volume production needs.
-
Cost-Effectiveness and Investment
- Crucible furnaces have low initial investment costs, making them accessible for small businesses or laboratories.
- However, their high energy consumption and low efficiency can offset these savings over time, particularly in energy-intensive applications.
In summary, crucibles offer significant advantages in terms of versatility, ease of use, and cost-effectiveness for small-scale operations. However, their disadvantages, such as low efficiency, high energy consumption, and potential contamination issues, must be carefully considered when selecting them for specific applications. Coating solutions and electric variants can address some of these challenges, but size limitations and operational costs remain key factors to evaluate.
Summary Table:
Advantages | Disadvantages |
---|---|
Versatile for melting various materials | High energy consumption and low efficiency |
Easy operation and low maintenance costs | Emissions and environmental impact |
Quick alloy change and low oxidation losses | Material contamination and scaling issues |
Compact size for small-scale use | Limited size for large-scale applications |
Low initial investment costs | High operational costs over time |
Want to learn more about crucible furnaces and their applications? Contact our experts today!