A muffle furnace is a versatile and widely used heating device in industries, research labs, and educational institutions. It offers several advantages, such as precise temperature control, uniform heating, and protection of samples from contamination, making it ideal for applications like heat treatment, sintering, and chemical analysis. However, it also has drawbacks, including low heating efficiency and high energy consumption in some models. Despite these limitations, its robust design, cost-effectiveness, and compatibility with various heating media make it a practical choice for many high-temperature processes.
Key Points Explained:
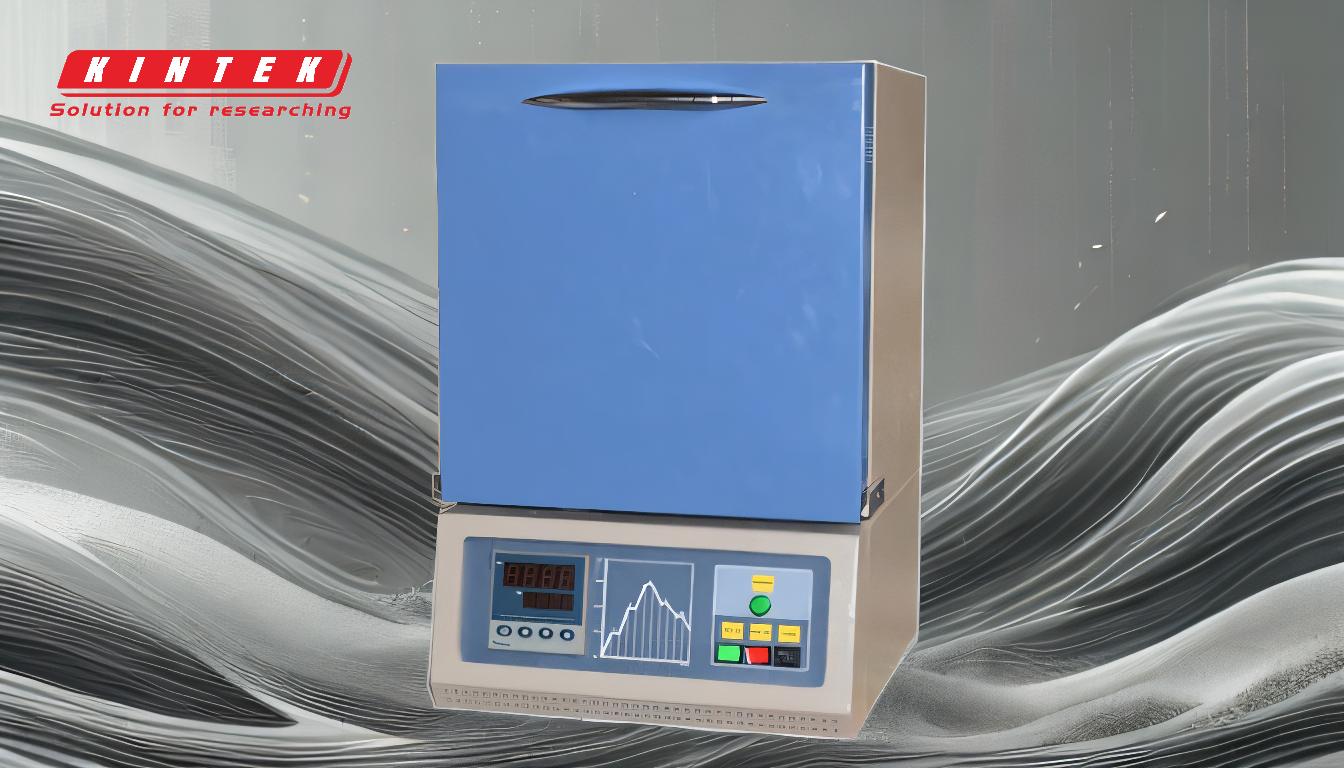
-
Advantages of Muffle Furnaces:
- Precise Temperature Control: Muffle furnaces are designed to maintain accurate and consistent temperatures, which is critical for processes like annealing, tempering, and sintering.
- Uniform Heating: They provide even heat distribution, ensuring that materials are heated uniformly, which is essential for consistent results in experiments and industrial processes.
- Controlled Atmosphere: Muffle furnaces can operate in a controlled environment, reducing oxidation and carbonization of samples, which is particularly useful for sensitive materials.
- Protection from Contamination: The enclosed design prevents external contaminants from affecting the samples, making it suitable for high-purity applications.
- Robust and Durable Construction: These furnaces are built to withstand high temperatures and harsh conditions, ensuring a long service life.
- Cost-Effectiveness: Compared to other high-temperature furnaces, muffle furnaces are relatively affordable, making them accessible for small-scale operations and educational institutions.
- Ease of Operation: Their simple structure and user-friendly controls make them easy to operate, even for beginners.
- Compatibility with Various Heating Media: Muffle furnaces can work with different atmospheres, such as air, hydrogen, nitrogen, or a mixture, providing flexibility for diverse applications.
-
Disadvantages of Muffle Furnaces:
- Low Heating Efficiency: Some muffle furnaces may have lower heating efficiency, leading to longer heating times and higher operational costs.
- High Energy Consumption: Due to their design and heating mechanisms, certain models may consume more energy, which can be a concern for cost-sensitive operations.
- Limited Capacity: Muffle furnaces are generally designed for small-scale processes, making them less suitable for large-scale industrial applications.
- Maintenance Requirements: While durable, they may require regular maintenance to ensure optimal performance, especially when used frequently.
-
Applications of Muffle Furnaces:
- Heat Treatment: Used for processes like annealing, quenching, and tempering of metals and alloys.
- Chemical Analysis: Ideal for ashing, sintering, and other laboratory procedures requiring precise temperature control.
- Material Testing: Commonly used in electronics, automotive, and mechanical engineering for testing components under high temperatures.
- Research and Education: Widely used in universities and research labs for experiments and teaching purposes.
-
Design and Operational Features:
- High-Performance Heating System: Equipped with durable heating elements that ensure consistent performance at high temperatures.
- Safety Features: Includes safety mechanisms to prevent overheating and ensure safe operation.
- Insulation: Efficient heat insulation minimizes heat loss, improving energy efficiency in some models.
- Compact Design: Their compact size makes them suitable for use in laboratories and small workspaces.
-
Considerations for Purchasers:
- Energy Efficiency: Evaluate the energy consumption of the furnace to ensure it aligns with operational budgets.
- Capacity and Size: Choose a furnace that meets the scale of your operations, whether for small-scale lab work or larger industrial processes.
- Temperature Range: Ensure the furnace can achieve the required temperatures for your specific applications.
- Atmosphere Compatibility: Consider the types of heating media the furnace can accommodate, especially if your processes require specific atmospheres.
- Maintenance and Durability: Opt for models with a reputation for durability and low maintenance requirements to minimize long-term costs.
In summary, muffle furnaces are a practical and versatile tool for high-temperature applications, offering precise control, uniform heating, and protection from contamination. However, their energy efficiency and capacity limitations should be carefully considered when selecting a model for specific needs.
Summary Table:
Aspect | Details |
---|---|
Advantages | Precise temperature control, uniform heating, contamination protection |
Disadvantages | Low heating efficiency, high energy consumption, limited capacity |
Applications | Heat treatment, chemical analysis, material testing, research & education |
Key Features | High-performance heating, safety mechanisms, compact design, insulation |
Considerations | Energy efficiency, capacity, temperature range, atmosphere compatibility |
Discover the ideal muffle furnace for your needs—contact our experts today!