Refractory materials are essential in high-temperature industrial applications due to their ability to withstand extreme heat, chemical corrosion, and mechanical stress. They are widely used in industries like steelmaking, glass production, and cement manufacturing. The advantages of refractory materials include their high thermal resistance, durability, and ability to maintain structural integrity under harsh conditions. However, they also have disadvantages, such as high costs, brittleness, and susceptibility to thermal shock. Understanding these pros and cons is crucial for selecting the right refractory material for specific applications, ensuring optimal performance and cost-effectiveness.
Key Points Explained:
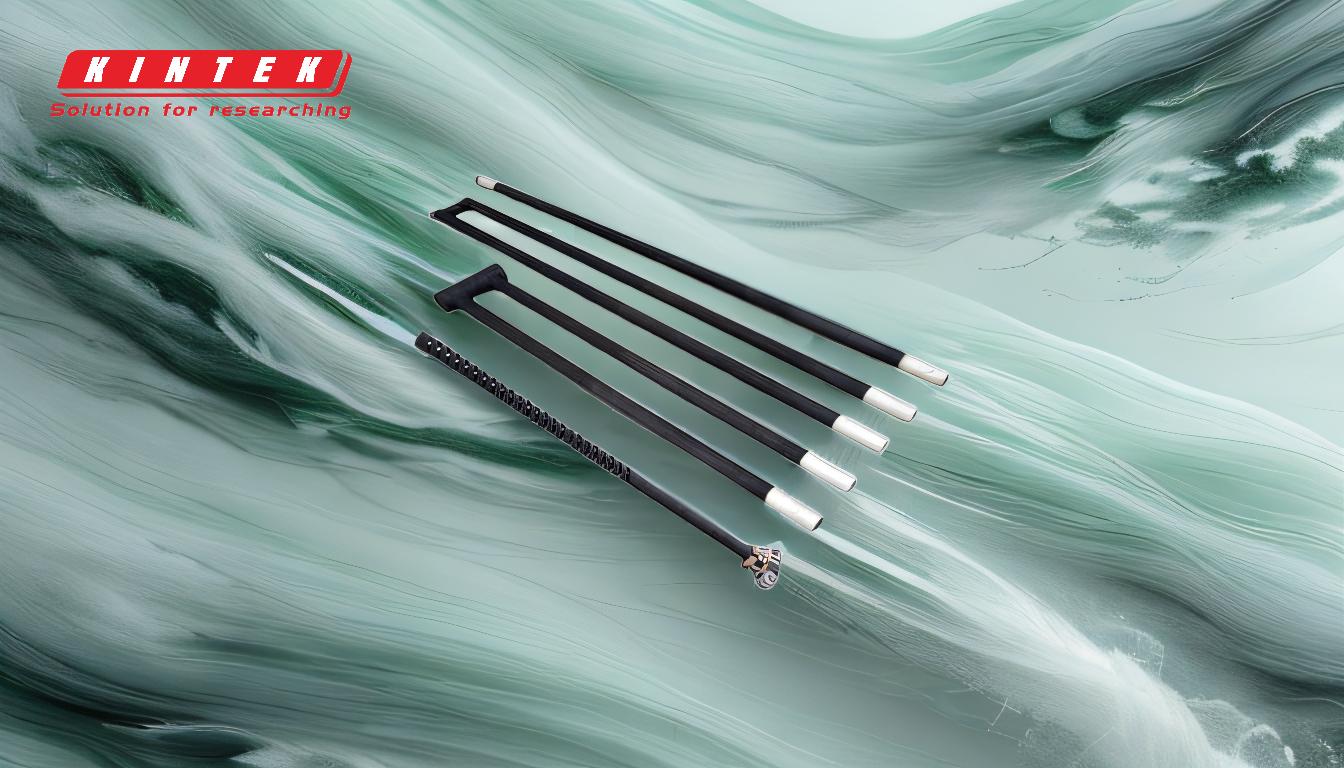
-
Advantages of Refractory Materials:
- High Thermal Resistance: Refractory materials are designed to withstand extremely high temperatures, often exceeding 1000°C, without melting or degrading. This makes them ideal for applications like furnaces, kilns, and reactors.
- Chemical Stability: They are resistant to chemical corrosion from molten metals, slags, and gases, which is critical in industries like steelmaking and glass production.
- Mechanical Strength: Refractories can endure mechanical stress, such as abrasion and impact, making them suitable for heavy industrial environments.
- Thermal Insulation: They provide excellent insulation, reducing heat loss and improving energy efficiency in high-temperature processes.
- Long Service Life: When properly selected and maintained, refractory materials can have a long operational lifespan, reducing the need for frequent replacements.
-
Disadvantages of Refractory Materials:
- High Cost: Refractory materials are often expensive due to the specialized raw materials and manufacturing processes required. This can increase the overall cost of industrial operations.
- Brittleness: Many refractory materials are brittle and prone to cracking or breaking under mechanical stress or thermal shock, which can lead to premature failure.
- Thermal Shock Susceptibility: Rapid temperature changes can cause thermal shock, leading to cracks and reduced performance. This is a significant limitation in processes with fluctuating temperatures.
- Limited Repairability: Once damaged, refractory linings can be challenging and costly to repair, often requiring partial or complete replacement.
- Weight and Installation Complexity: Refractory materials are often heavy, and their installation can be labor-intensive and time-consuming, requiring skilled technicians.
-
Applications and Selection Criteria:
- Steelmaking: Refractories are used in blast furnaces, ladles, and tundishes, where they must resist high temperatures and chemical corrosion from molten steel and slag.
- Glass Production: In glass furnaces, refractories must withstand high temperatures and resist corrosion from molten glass and alkali vapors.
- Cement Manufacturing: Rotary kilns in cement plants require refractories that can endure extreme heat and mechanical wear.
- Selection Criteria: The choice of refractory material depends on factors such as operating temperature, chemical environment, mechanical stress, and thermal cycling. Common materials include alumina, silica, magnesia, and zirconia, each with specific properties suited to different applications.
-
Future Trends and Innovations:
- Advanced Materials: Research is ongoing to develop new refractory materials with improved thermal shock resistance, lower costs, and enhanced durability.
- Recycling and Sustainability: Efforts are being made to recycle used refractories and develop more sustainable manufacturing processes to reduce environmental impact.
- Smart Refractories: Innovations like embedded sensors in refractory linings are being explored to monitor temperature and wear in real-time, improving maintenance and performance.
In conclusion, refractory materials offer significant advantages in high-temperature industrial applications, but their limitations must be carefully considered. By understanding their properties and selecting the right material for specific conditions, industries can optimize performance, reduce costs, and extend the lifespan of their equipment.
Summary Table:
Aspect | Details |
---|---|
Advantages | High thermal resistance, chemical stability, mechanical strength, insulation, long service life |
Disadvantages | High cost, brittleness, thermal shock susceptibility, limited repairability, weight and installation complexity |
Applications | Steelmaking, glass production, cement manufacturing |
Selection Criteria | Operating temperature, chemical environment, mechanical stress, thermal cycling |
Future Trends | Advanced materials, recycling and sustainability, smart refractories |
Need help selecting the right refractory material for your application? Contact our experts today for tailored solutions!