Wet ashing is a widely used technique for determining ash content in food samples, offering advantages such as speed and simplicity. However, it also comes with limitations, including potential sample loss and the need for careful handling of corrosive chemicals. Below is a detailed exploration of the advantages and disadvantages of using the wet ashing technique.
Key Points Explained:
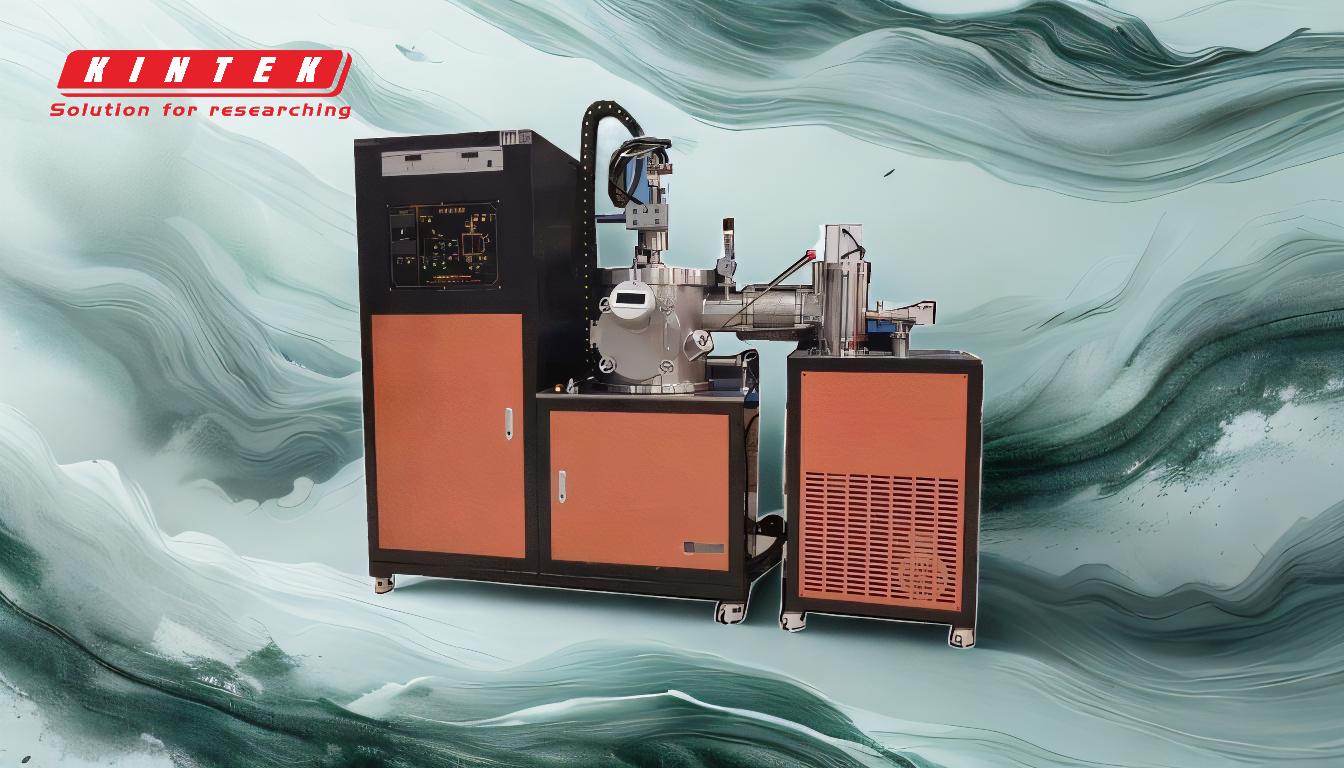
-
Advantages of Wet Ashing:
- Speed: Wet ashing is significantly faster than dry ashing, typically taking between 10 minutes to a few hours. This makes it suitable for laboratories requiring quick results.
- Efficiency: The method involves heating the sample at a controlled temperature (e.g., 350°C), which ensures thorough decomposition of organic matter, leaving behind inorganic residues (ash).
- Versatility: Wet ashing can be applied to a wide range of food samples, making it a flexible technique for ash content determination.
- Minimized Volatile Loss: Compared to dry ashing, wet ashing reduces the risk of losing volatile elements, ensuring more accurate results for certain types of samples.
-
Disadvantages of Wet Ashing:
- Use of Corrosive Chemicals: The process requires strong acids (e.g., nitric acid, sulfuric acid), which are hazardous and require careful handling, storage, and disposal.
- Risk of Sample Contamination: The use of acids and other chemicals increases the likelihood of introducing contaminants, which can affect the accuracy of results.
- Potential Sample Loss: Wet ashing can lead to partial loss of the sample due to spattering or incomplete digestion, especially if the process is not carefully controlled.
- Equipment Requirements: The technique demands specialized equipment, such as fume hoods and acid-resistant containers, which may not be readily available in all laboratories.
- Limited Applicability for Certain Samples: Wet ashing may not be suitable for samples with high fat or sugar content, as these can interfere with the digestion process.
-
Comparison with Dry Ashing:
- Wet ashing is generally faster but requires more attention to safety and chemical handling compared to dry ashing, which is slower but less hazardous.
- Dry ashing is better suited for samples that are sensitive to acid digestion, while wet ashing is preferred for samples that require rapid decomposition.
-
Practical Considerations for Equipment and Consumables Purchasers:
- Ensure the laboratory is equipped with proper safety measures, such as fume hoods and personal protective equipment (PPE), to handle corrosive chemicals.
- Invest in high-quality, acid-resistant containers and digestion apparatus to minimize sample loss and contamination.
- Consider the specific requirements of the samples being tested when choosing between wet ashing and other methods.
In summary, wet ashing offers a fast and efficient way to determine ash content in food samples, but it requires careful handling of hazardous chemicals and specialized equipment. Laboratories must weigh these advantages and disadvantages based on their specific needs and capabilities.
Summary Table:
Aspect | Advantages | Disadvantages |
---|---|---|
Speed | Faster than dry ashing (10 minutes to a few hours) | Requires careful handling of corrosive chemicals |
Efficiency | Thorough decomposition of organic matter at controlled temperatures | Risk of sample contamination due to chemical use |
Versatility | Applicable to a wide range of food samples | Potential sample loss from spattering or incomplete digestion |
Minimized Volatile Loss | Reduces loss of volatile elements, ensuring accurate results | Demands specialized equipment (e.g., fume hoods, acid-resistant containers) |
Applicability | Preferred for rapid decomposition | Limited suitability for samples with high fat or sugar content |
Need help choosing the right ashing method for your lab? Contact our experts today for personalized advice!