Hot isostatic pressing (HIP) is a versatile manufacturing process that offers significant advantages in improving material properties such as wear resistance, corrosion resistance, and mechanical performance. It can increase fatigue life by 10 to 100 times and achieve material densities close to theoretical values. However, it also has limitations, including lower accuracy of pressed surfaces, the need for expensive spray-dried powders, and lower production rates compared to other methods like extrusion or die compaction. HIP is widely used in industries such as aerospace, automotive, oil and gas, medical devices, and energy storage technologies like lithium-ion batteries and fuel cells. The process is divided into three main applications: densification, diffusion connection, and powder metallurgy products, chosen based on the specific needs of the products being processed.
Key Points Explained:
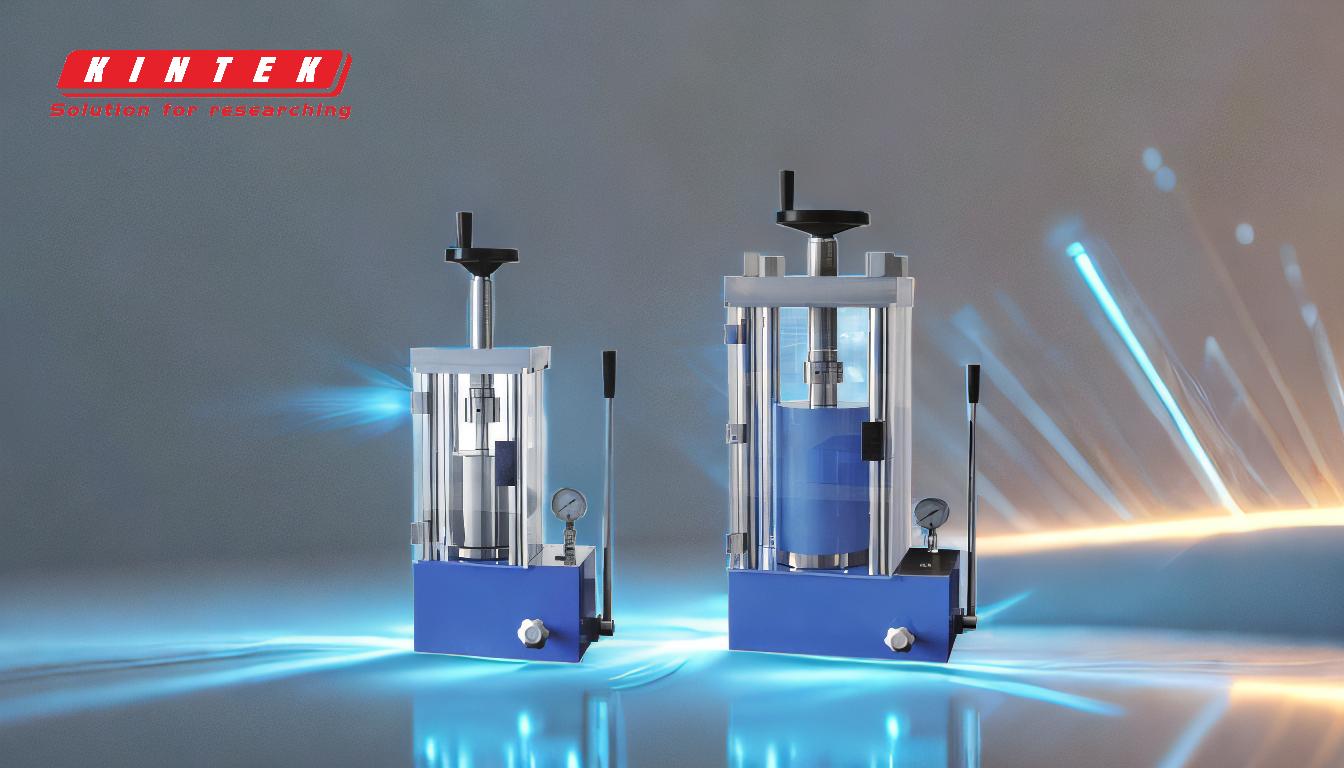
-
Advantages of Hot Isostatic Pressing (HIP):
- Improved Material Properties: HIP enhances wear resistance, corrosion resistance, and mechanical performance. It significantly increases fatigue life by 10 to 100 times and achieves material densities close to theoretical values.
- Uniform Density and Strength: The process provides uniform strength in all directions and uniform density, which is crucial for high-performance components.
- Shape Flexibility: HIP allows for complex shapes and geometries, making it suitable for a wide range of applications.
- Consolidation of Manufacturing Steps: HIP combines heat treatment, quenching, and aging processes, reducing overall production time and costs.
- Defect Healing: HIP is effective in healing defects in castings and additively manufactured parts, addressing issues like porosity and poor layer adhesion, resulting in a uniform microstructure.
-
Limitations of Hot Isostatic Pressing (HIP):
- Lower Accuracy: Pressed surfaces adjacent to the flexible bag may have lower accuracy compared to mechanical pressing or extrusion, often requiring subsequent machining.
- Cost of Materials: The process requires relatively expensive spray-dried powders for fully automatic dry bag presses.
- Production Rates: HIP generally has lower production rates compared to extrusion or die compaction, which can be a limitation for high-volume manufacturing.
-
Applications of Hot Isostatic Pressing:
- Densification: HIP is used to achieve high-density materials, which is essential for applications requiring high strength and durability.
- Diffusion Connection: The process is used to join dissimilar materials through diffusion bonding, creating strong, seamless joints.
- Powder Metallurgy Products: HIP is widely used in powder metallurgy to produce high-performance components with complex shapes and uniform properties.
-
Industry Applications:
- Aerospace and Automotive: HIP is used to manufacture advanced ceramics and high-performance components that require superior mechanical properties and durability.
- Oil and Gas: The process is applied to produce components that can withstand harsh environments and high pressures.
- Medical Devices: HIP is used to create medical implants and devices with high biocompatibility and mechanical strength.
- Energy Storage: The process is applied in the production of lithium-ion batteries and fuel cells, where uniform density and high performance are critical.
-
Process Optimization:
- Time, Temperature, and Pressure: The effectiveness of HIP depends on the optimization of these three key variables. Proper control ensures uniform density and strength in the final product.
- Reduction of Die Wall Interaction: HIP reduces die wall interaction, enhancing the uniformity of the sample and improving overall material properties.
In summary, hot isostatic pressing offers significant advantages in improving material properties and achieving uniform density and strength, making it suitable for a wide range of high-performance applications. However, it also has limitations such as lower accuracy, higher material costs, and lower production rates. The process is widely used in industries requiring high-performance components and is optimized through careful control of time, temperature, and pressure. For more detailed information on the process, you can refer to the warm isostatic press topic.
Summary Table:
Aspect | Details |
---|---|
Advantages | - Enhanced wear resistance and corrosion resistance |
- Increased fatigue life (10-100x) | |
- Uniform density and strength | |
- Shape flexibility for complex geometries | |
- Consolidation of manufacturing steps | |
- Defect healing in castings and additive manufacturing | |
Limitations | - Lower accuracy of pressed surfaces |
- Requires expensive spray-dried powders | |
- Lower production rates compared to extrusion or die compaction | |
Applications | - Densification, diffusion connection, powder metallurgy |
Industries | - Aerospace, automotive, oil and gas, medical devices, energy storage |
Optimization | - Control of time, temperature, and pressure |
- Reduction of die wall interaction |
Unlock the full potential of hot isostatic pressing for your applications—contact our experts today!