Air quenching is a heat treatment process where hot metal is cooled rapidly using air, rather than liquids like oil or water. This method offers several advantages, including reduced risk of distortion, improved surface finish, and environmental benefits due to the absence of quenching oils. It is particularly suitable for materials that require controlled cooling rates to achieve desired mechanical properties. Additionally, air quenching is cost-effective, as it eliminates the need for expensive quenching media and reduces maintenance requirements. The process is also safer, as it avoids the hazards associated with handling hot oils or water. Overall, air quenching provides a reliable and efficient solution for heat treatment in various industrial applications.
Key Points Explained:
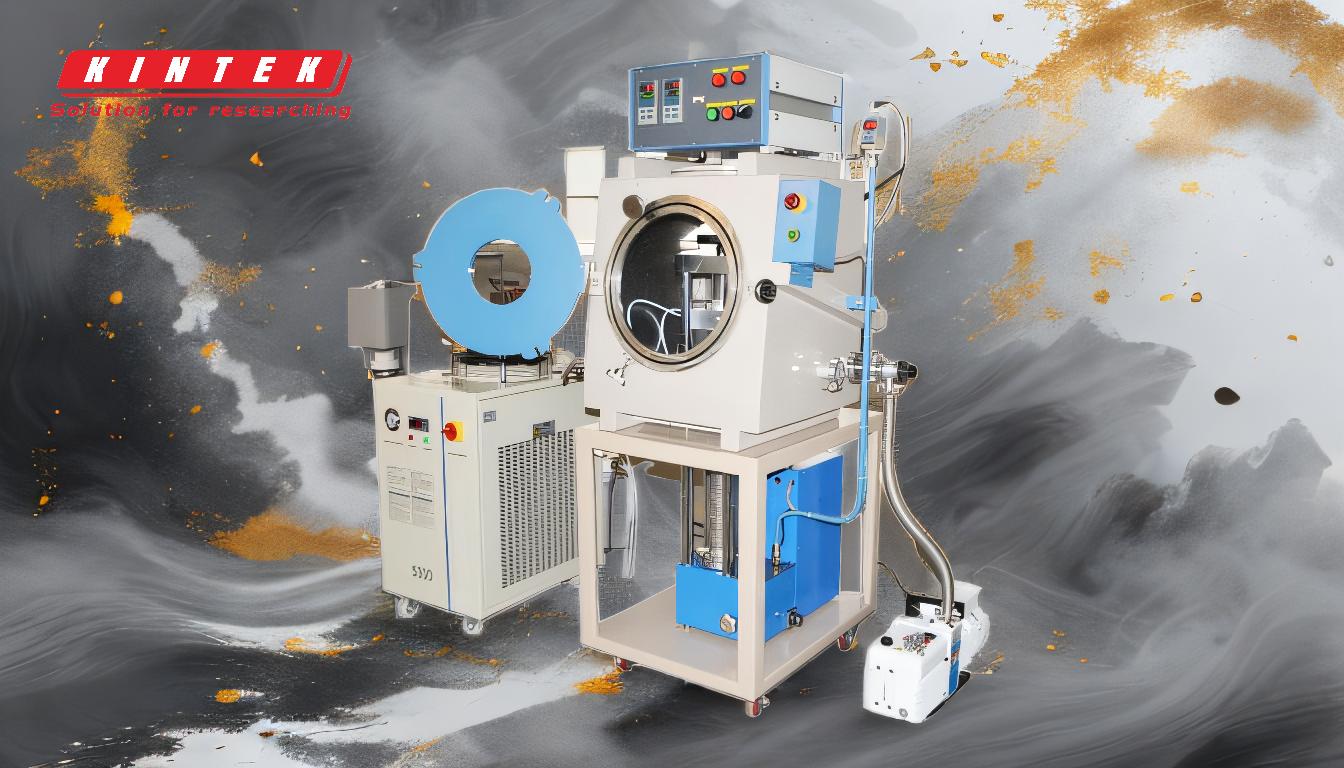
-
Reduced Risk of Distortion:
- Air quenching involves cooling the metal at a slower and more controlled rate compared to liquid quenching methods. This reduces thermal stress and minimizes the risk of warping or distortion, which is especially important for complex or precision-engineered components.
-
Improved Surface Finish:
- Since air quenching does not involve contact with liquids, it avoids issues like surface oxidation or contamination that can occur with oil or water quenching. This results in a cleaner and smoother surface finish, which is critical for applications requiring high aesthetic or functional standards.
-
Environmental Benefits:
- Air quenching is an eco-friendly alternative to oil or water quenching. It eliminates the need for quenching oils, which can be hazardous to the environment and require proper disposal. This makes air quenching a more sustainable option for heat treatment processes.
-
Cost-Effectiveness:
- The absence of quenching oils or other liquids reduces operational costs. There is no need to purchase, store, or dispose of quenching media, and maintenance requirements are lower since there is no risk of oil degradation or contamination.
-
Safety:
- Air quenching is inherently safer than liquid quenching methods. It eliminates the risks associated with handling hot oils or water, such as burns, fires, or spills. This makes the process more suitable for environments where safety is a priority.
-
Versatility:
- Air quenching can be used for a wide range of materials, including steels, alloys, and other metals that require controlled cooling rates. It is particularly effective for materials that are prone to cracking or distortion when exposed to rapid cooling.
-
Consistency and Reliability:
- The controlled cooling rate of air quenching ensures consistent results, making it a reliable method for achieving desired mechanical properties such as hardness, strength, and toughness. This consistency is crucial for industries like aerospace, automotive, and tool manufacturing.
-
Energy Efficiency:
- Air quenching systems often require less energy compared to liquid quenching systems, as there is no need to heat or circulate quenching media. This contributes to lower energy consumption and operational costs.
By leveraging these advantages, air quenching provides a practical and efficient solution for heat treatment, meeting the needs of modern industrial applications while addressing environmental and safety concerns.
Summary Table:
Advantage | Description |
---|---|
Reduced Risk of Distortion | Controlled cooling minimizes thermal stress, reducing warping and distortion. |
Improved Surface Finish | No liquid contact prevents oxidation or contamination, ensuring a cleaner finish. |
Environmental Benefits | Eliminates hazardous quenching oils, making it eco-friendly and sustainable. |
Cost-Effectiveness | No need for expensive quenching media or disposal, lowering operational costs. |
Safety | Avoids risks of burns, fires, or spills associated with hot oils or water. |
Versatility | Suitable for a wide range of materials requiring controlled cooling rates. |
Consistency and Reliability | Ensures uniform mechanical properties like hardness, strength, and toughness. |
Energy Efficiency | Requires less energy compared to liquid quenching systems, reducing energy consumption. |
Ready to optimize your heat treatment process? Contact us today to learn how air quenching can benefit your operations!