Spark Plasma Sintering (SPS) is a cutting-edge sintering technology that offers numerous advantages over traditional sintering methods. Its key benefits include significantly shorter cycle times, lower sintering temperatures, and the ability to densify a wide range of materials, from low melting point metals to ultra-high temperature ceramics. SPS also provides high-precision process control, enabling finely tuned sintering parameters for optimal outcomes. Additionally, the technology leverages high heating and cooling rates, adjustable sintering pressure, and multi-field coupling (electricity-mechanical-thermal) to enhance densification and improve material properties. These features make SPS a versatile and efficient solution for advanced material processing.
Key Points Explained:
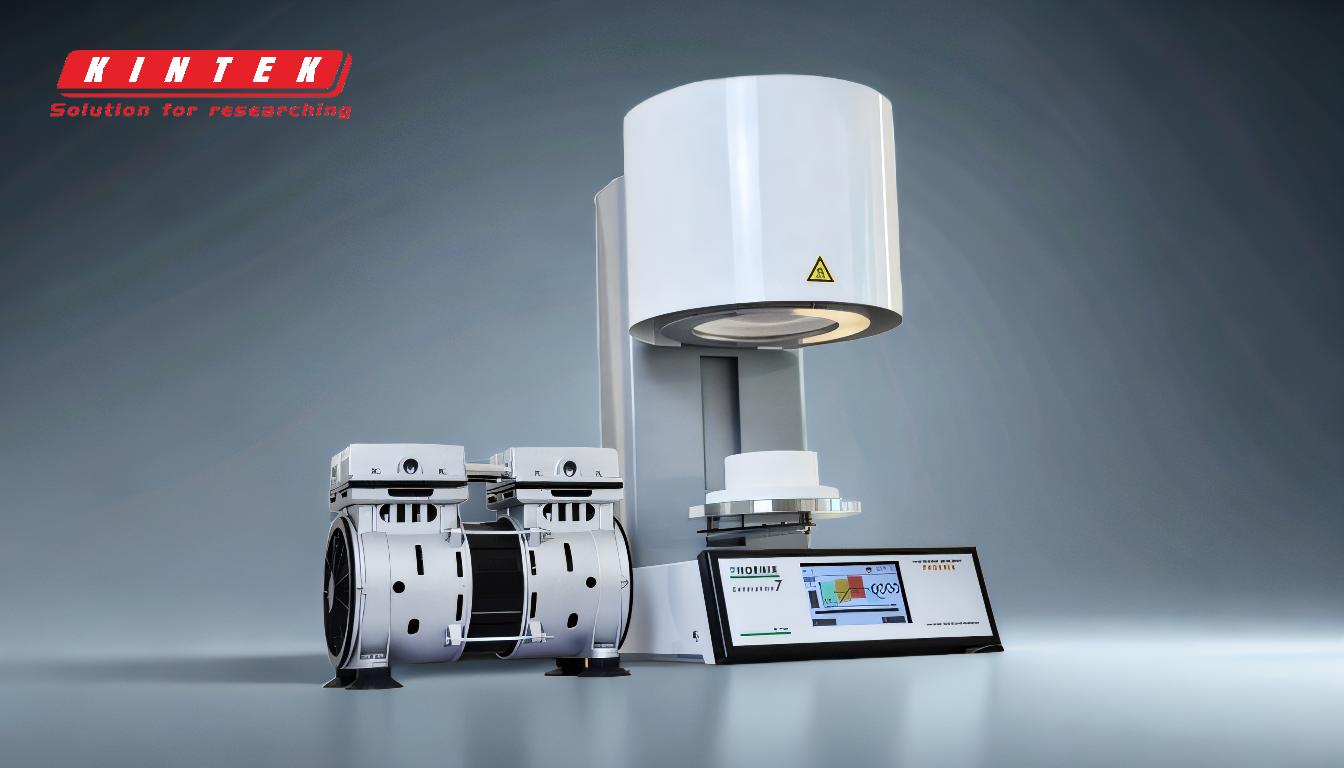
-
Shorter Cycle Times:
- SPS drastically reduces sintering times compared to conventional methods, with cycles taking minutes instead of hours or days. This efficiency is due to the rapid heating and cooling rates enabled by the high pulsed current, which accelerates the sintering process without compromising material quality.
-
Lower Sintering Temperatures:
- SPS operates at lower temperatures than traditional sintering techniques, which is particularly advantageous for materials sensitive to high temperatures. This feature helps preserve the microstructure and properties of the material, reducing the risk of thermal degradation.
-
Versatility in Material Densification:
- SPS can densify a wide range of materials, including low melting point metals, ultra-high temperature ceramics, and composites. This versatility makes it suitable for diverse applications in industries such as aerospace, electronics, and energy.
-
High-Precision Process Control:
- The technology allows for precise control over sintering parameters, such as temperature, pressure, and heating rate. This level of control ensures consistent and optimal outcomes, making it ideal for producing high-performance materials with tailored properties.
-
High Heating and Cooling Rates:
- The rapid heating and cooling rates in SPS not only shorten processing times but also enhance material densification. This is particularly beneficial for electrically conductive materials, where the high pulsed current promotes better particle bonding and densification.
-
Adjustable Sintering Pressure:
- SPS enables adjustable sintering pressure, which can be fine-tuned to suit specific material requirements. This flexibility helps achieve higher densities and improved mechanical properties in the final product.
-
Multi-Field Coupling (Electricity-Mechanical-Thermal):
- The integration of electrical, mechanical, and thermal fields in SPS creates a synergistic effect that enhances the sintering process. This multi-field coupling improves material densification and microstructure development, leading to superior material performance.
These advantages collectively make SPS a highly efficient, versatile, and precise sintering technology, well-suited for advanced material processing and innovation.
Summary Table:
Advantage | Description |
---|---|
Shorter Cycle Times | Reduces sintering times to minutes, enabled by rapid heating and cooling rates. |
Lower Sintering Temperatures | Operates at lower temperatures, preserving material microstructure. |
Versatility in Densification | Densifies a wide range of materials, from metals to ceramics and composites. |
High-Precision Process Control | Ensures optimal outcomes with precise control over sintering parameters. |
High Heating/Cooling Rates | Enhances densification and reduces processing times. |
Adjustable Sintering Pressure | Fine-tunes pressure for higher densities and improved mechanical properties. |
Multi-Field Coupling | Integrates electrical, mechanical, and thermal fields for superior performance. |
Ready to revolutionize your material processing? Contact us today to learn more about Spark Plasma Sintering!