Hot Isostatic Pressing (HIP) offers significant advantages over conventional Powder Metallurgy (PM) processes, primarily due to its ability to enhance material properties, reduce defects, and improve structural integrity. HIP combines high temperature and isostatic pressure to densify materials, eliminate porosity, and improve mechanical properties such as fatigue life and tensile strength. Unlike conventional PM, which relies on compaction and sintering, HIP achieves near-theoretical density by uniformly applying pressure in all directions, resulting in superior material performance. Additionally, HIP is eco-friendly, reduces scrap material, and can be integrated with other heat treatment processes to streamline production. These benefits make HIP a preferred choice for industries requiring high-performance materials, such as aerospace, automotive, and medical sectors.
Key Points Explained:
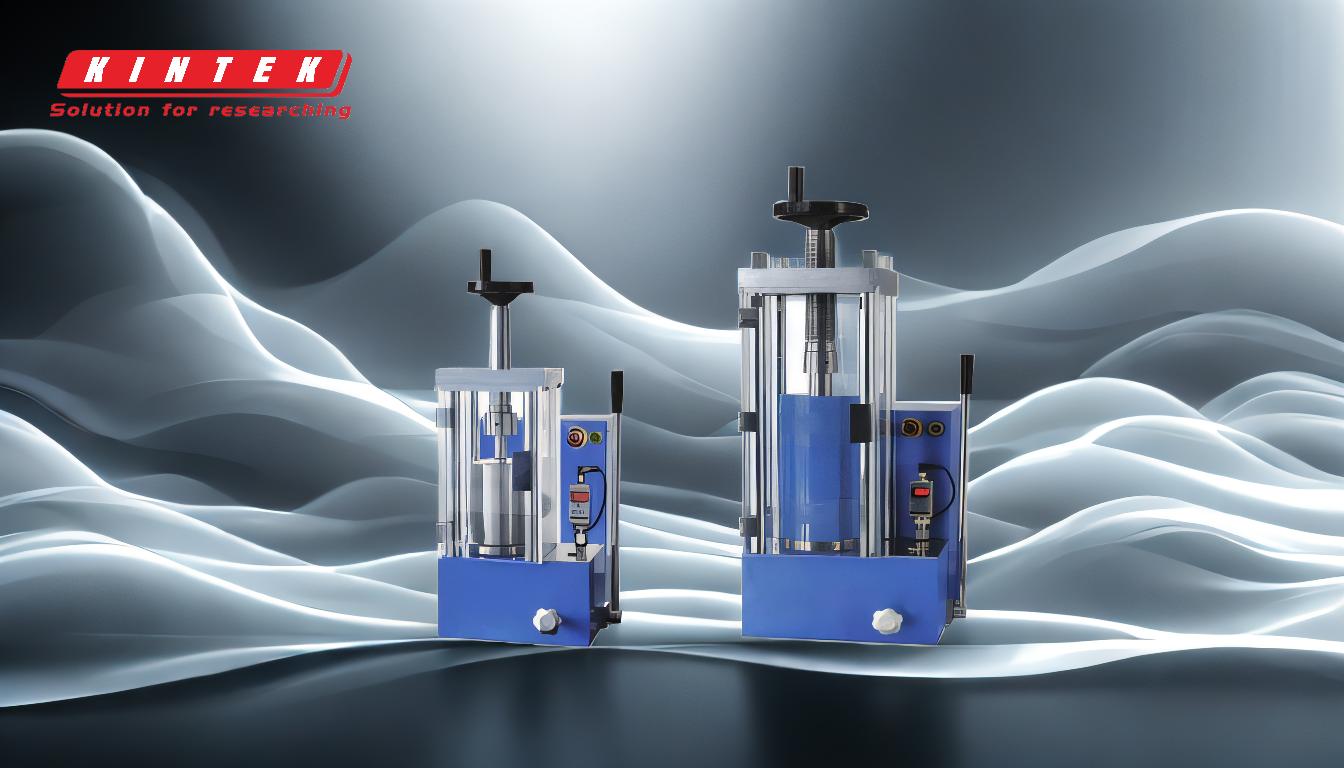
-
Superior Material Density and Mechanical Properties:
- HIP achieves near-theoretical density by eliminating voids and porosity through the application of uniform isostatic pressure and high temperature. This results in materials with enhanced mechanical properties, such as improved tensile strength, fatigue life, and fracture toughness.
- Unlike conventional PM, which may leave residual porosity, HIP ensures a fully dense microstructure, making it ideal for critical applications where material integrity is paramount.
-
Defect Elimination and Structural Integrity:
- HIP effectively eliminates internal defects such as microshrinkage, voids, and cracks by diffusion bonding the surfaces of these defects under high pressure and temperature. This enhances the structural integrity of the material, making it more reliable for high-stress applications.
- Conventional PM processes may not fully address these defects, leading to potential weaknesses in the final product.
-
Improved Fatigue Life and Weldability:
- HIP significantly improves fatigue life, often by 1.5 to 8 times compared to conventional PM. This is particularly beneficial for components subjected to cyclic loading, such as turbine blades and aerospace parts.
- The process also enhances weldability by homogenizing the microstructure and reducing segregation, making it easier to join materials without compromising strength.
-
Eco-Friendly and Reduced Scrap Production:
- HIP minimizes material waste by treating raw materials with pressure and heat before subsequent manufacturing steps. This reduces the need for additional machining and lowers scrap production.
- Conventional PM, while efficient, may still generate more waste during post-processing steps like machining and finishing.
-
Integration with Heat Treatment Processes:
- HIP can be combined with other heat treatment processes in a single unit, reducing energy consumption and delivery times. This integration eliminates the need for multiple handling and transportation steps, streamlining production.
- Conventional PM typically requires separate processes for compaction, sintering, and heat treatment, which can be less efficient.
-
Versatility in Material Utilization:
- HIP is capable of processing a wide range of materials, including metals, ceramics, and composites. It is particularly effective for utilizing powder materials and producing net or near-net shape parts with complex geometries.
- Conventional PM is limited in its ability to handle certain materials and geometries, making HIP a more versatile option for advanced manufacturing.
-
Cost-Effectiveness in High-Performance Applications:
- While HIP may have higher initial costs compared to conventional PM, its ability to produce high-performance materials with minimal post-processing can lead to long-term cost savings. This is especially true for industries where material performance is critical, such as aerospace and medical devices.
- Conventional PM, though cost-effective for simpler applications, may require additional steps to achieve comparable performance, increasing overall costs.
In summary, HIP offers a range of advantages over conventional PM, including superior material properties, defect elimination, improved fatigue life, and eco-friendly production. Its ability to integrate with other processes and handle diverse materials makes it a highly effective and versatile manufacturing solution for high-performance applications.
Summary Table:
Advantage | HIP | Conventional PM |
---|---|---|
Material Density | Near-theoretical density, fully dense microstructure | Residual porosity may remain |
Defect Elimination | Eliminates microshrinkage, voids, and cracks | May leave internal defects |
Fatigue Life Improvement | 1.5 to 8 times improvement | Limited improvement |
Eco-Friendliness | Reduces scrap and material waste | Generates more waste during post-processing |
Integration with Heat Treatment | Combines processes in a single unit, streamlining production | Requires separate compaction, sintering, and heat treatment steps |
Material Versatility | Processes metals, ceramics, and composites; handles complex geometries | Limited material and geometry handling capabilities |
Cost-Effectiveness | Higher initial cost but long-term savings in high-performance sectors | Cost-effective for simpler applications but may require additional performance steps |
Ready to enhance your material performance with HIP? Contact us today to learn more!