Hot isostatic pressing (HIP) is a highly effective manufacturing process that enhances material properties by applying high temperature and pressure simultaneously. This process offers numerous advantages, including improved density, mechanical properties, and fatigue resistance, as well as the ability to repair defects and create metallurgical bonds between materials. HIP is particularly beneficial for reducing porosity, increasing structural integrity, and consolidating manufacturing steps, making it a versatile solution for industries such as aerospace, automotive, and additive manufacturing.
Key Points Explained:
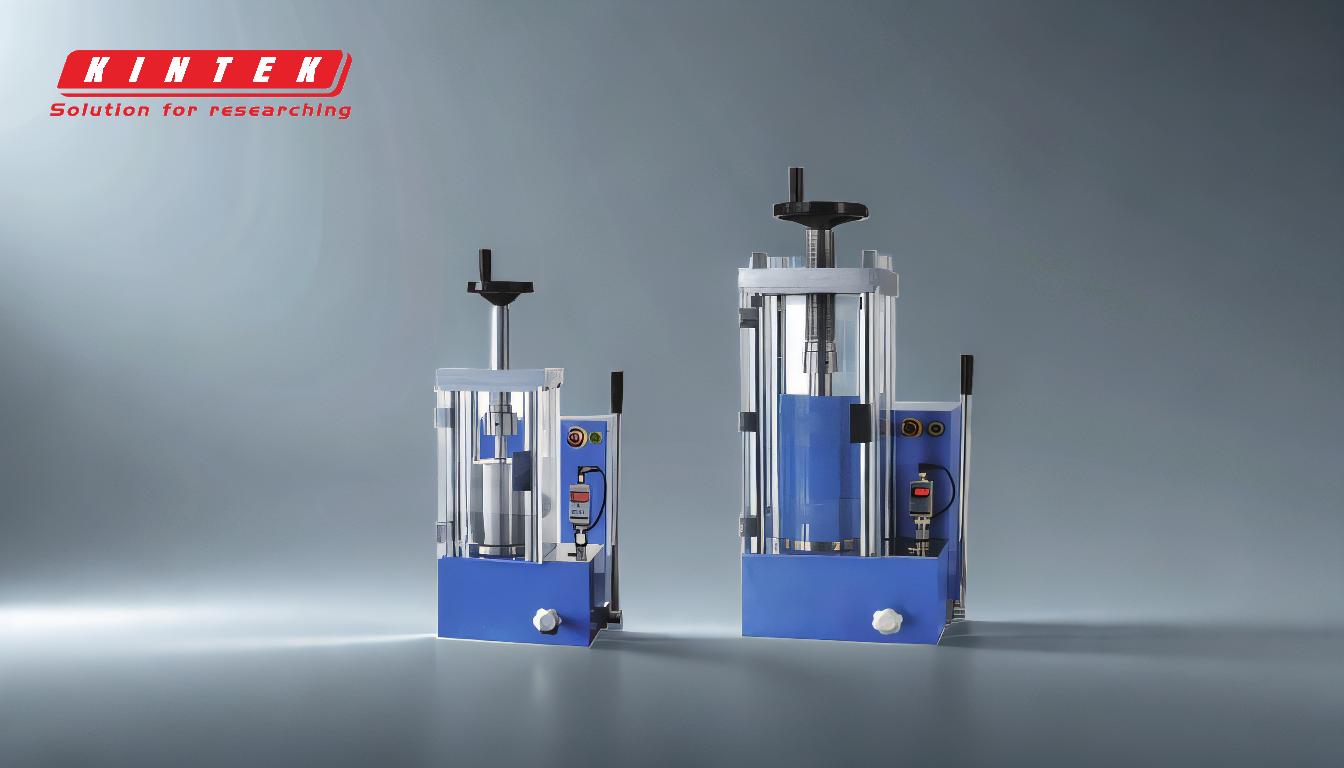
-
Improved Material Density and Structural Integrity
- HIP eliminates residual porosity in materials, achieving a density close to the theoretical maximum. This is especially important for sintered powder metallurgy (PM) parts, castings, and 3D-printed components.
- By removing voids and pores, HIP enhances structural integrity, ensuring parts can withstand higher stress and load conditions.
- This process is particularly effective for addressing issues like microshrinkage and poor layer adhesion in additive manufacturing.
-
Enhanced Mechanical Properties
- HIP significantly improves mechanical properties such as wear resistance, corrosion resistance, ductility, and toughness.
- Fatigue life can be increased by 10 to 100 times, making HIP-treated parts ideal for high-performance applications.
- The process also reduces property fluctuations, ensuring consistent performance across batches.
-
Defect Repair and Porosity Elimination
- HIP can repair internal porosity defects in castings and sintered parts, which are often difficult to address through traditional methods.
- For 3D-printed parts, HIP addresses porosity and poor interlayer bonding, creating a uniform microstructure.
-
Uniform Density and Strength
- Unlike conventional pressing methods, HIP applies pressure uniformly in all directions, resulting in uniform density and strength throughout the part.
- This eliminates issues like die wall friction, which can cause uneven density in traditional pressing techniques.
-
Lightweight and Optimized Designs
- HIP enables the production of lighter components without compromising strength or durability. This is particularly valuable in industries like aerospace, where weight reduction is critical.
- The process allows for more complex and optimized designs, as it can handle intricate shapes and geometries.
-
Metallurgical Bonding and Material Compatibility
- HIP can create strong metallurgical bonds between dissimilar materials, enabling the production of hybrid components with unique properties.
- This is particularly useful for applications requiring materials with different thermal or mechanical characteristics.
-
Consolidated Manufacturing Steps
- HIP combines multiple manufacturing processes, such as heat treatment, quenching, and aging, into a single step. This reduces production time and costs.
- For example, in additive manufacturing, HIP can simultaneously densify and heat-treat parts, streamlining the production workflow.
-
Versatility Across Industries
- HIP is widely used in industries such as aerospace, automotive, medical, and energy due to its ability to enhance material performance and reliability.
- It is particularly valuable for critical components like turbine blades, engine parts, and medical implants, where failure is not an option.
-
Comparison with Warm Isostatic Pressing
- While HIP operates at high temperatures, warm isostatic press (WIP) is performed at lower temperatures, making it suitable for materials that cannot withstand extreme heat.
- WIP is often used as a preliminary step before HIP to compact the product, followed by sintering and HIP for final densification.
-
Economic and Environmental Benefits
- By reducing scrap and losses, HIP improves material utilization and lowers production costs.
- The process also extends the service life of components, reducing the need for frequent replacements and contributing to sustainability efforts.
In summary, hot isostatic pressing is a transformative technology that offers a wide range of benefits, from improving material properties to enabling innovative designs and reducing production costs. Its ability to address porosity, enhance mechanical performance, and consolidate manufacturing steps makes it an indispensable tool for modern manufacturing.
Summary Table:
Advantage | Description |
---|---|
Improved Density | Eliminates porosity, achieving near-theoretical maximum density. |
Enhanced Mechanical Properties | Increases wear resistance, fatigue life, and toughness. |
Defect Repair | Repairs internal porosity and poor interlayer bonding in 3D-printed parts. |
Uniform Density and Strength | Applies pressure uniformly, ensuring consistent material properties. |
Lightweight Designs | Enables lighter components without compromising strength. |
Metallurgical Bonding | Creates strong bonds between dissimilar materials. |
Consolidated Manufacturing | Combines heat treatment, quenching, and aging into a single step. |
Versatility Across Industries | Used in aerospace, automotive, medical, and energy sectors. |
Economic and Environmental Benefits | Reduces scrap, lowers costs, and extends component lifespan. |
Unlock the full potential of hot isostatic pressing for your applications—contact us today!