Isostatic pressing, particularly hot isostatic pressing (HIP), offers numerous advantages in material processing and manufacturing. This method applies uniform pressure in all directions, enabling the production of high-density, high-performance materials with superior structural integrity. It is highly effective for creating complex shapes, improving mechanical properties, and enhancing material utilization, especially for difficult-to-compact and expensive materials like superalloys, titanium, and stainless steel. HIP combines compaction and sintering under high heat and pressure, which eliminates internal defects, improves material properties, and reduces production time by consolidating multiple manufacturing steps. Overall, isostatic pressing is a versatile and efficient process for achieving uniform density, strength, and shape flexibility in advanced materials.
Key Points Explained:
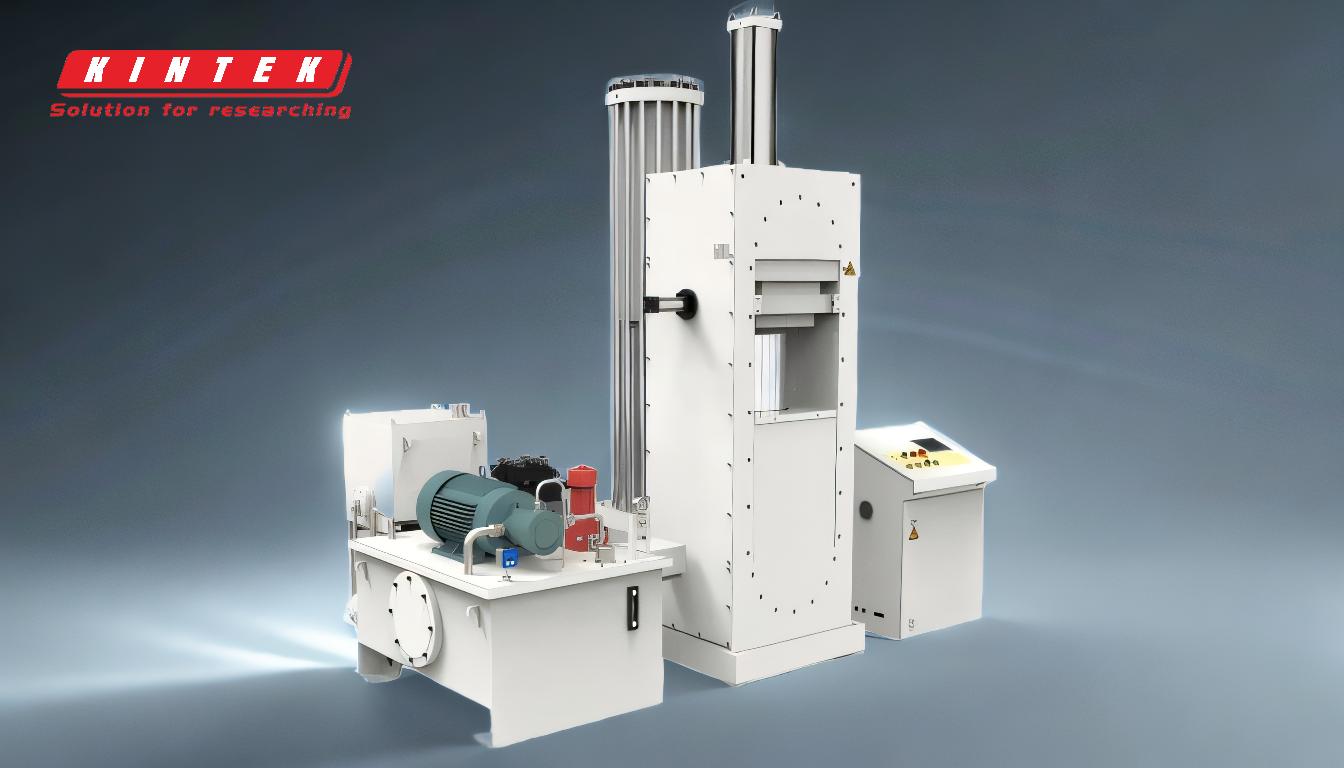
-
Uniform Pressure Application
- Isostatic pressing applies uniform pressure in all directions, ensuring consistent material properties throughout the part. This eliminates the geometric constraints and density variations often seen in unidirectional pressing methods.
- This uniformity is particularly beneficial for achieving high and uniform density in complex shapes, which are difficult to produce using conventional techniques.
-
High-Density and High-Performance Materials
- The process enables the production of materials with high density and superior structural integrity. This is crucial for applications requiring high-performance materials, such as aerospace, medical, and energy sectors.
- By eliminating internal microporosity and voids, isostatic pressing enhances mechanical properties like hardness, wear resistance, and thermal stability.
-
Complex and Intricate Shapes
- Isostatic pressing allows for the manufacturing of complex and intricate shapes that are challenging to achieve with traditional methods. This is made possible by using elastomeric molds, which can be engineered to accommodate detailed geometries.
- This capability is especially valuable for industries requiring precision components, such as additive manufacturing and advanced engineering.
-
Improved Mechanical Properties
- The process significantly improves material properties, including fatigue resistance, ductility, impact strength, and toughness. These enhancements are achieved through the elimination of internal defects and the creation of a fine, uniform grain structure.
- For 3D-printed parts, HIP addresses issues like porosity and poor layer adhesion, resulting in a uniform microstructure and improved performance.
-
Efficient Material Utilization
- Isostatic pressing is highly efficient for processing difficult-to-compact and expensive materials, such as superalloys, titanium, and stainless steel. It minimizes material waste and ensures optimal use of resources.
- This efficiency is particularly important for industries where material costs are a significant factor.
-
Combination of Compaction and Sintering
- HIP combines compaction and sintering under high heat and pressure, which solidifies powder particles and repairs voids and pores. This results in a high-strength, dense structure as the part shrinks and densifies.
- The process can be performed without a die, but cold isostatic pressing (CIP) is often used first to compact the product, followed by sintering and then HIP.
-
Consolidation of Manufacturing Steps
- HIP consolidates multiple manufacturing steps, such as heat treatment, quenching, and aging, into a single process. This reduces overall production time and costs while improving material properties.
- This consolidation is particularly beneficial for industries looking to streamline production processes and enhance efficiency.
-
Relief of Thermal Stresses
- HIP relieves thermal stresses in cast, sintered, and additively manufactured parts. This improves the overall quality and reliability of the components, making them suitable for demanding applications.
- The process ensures that parts have a uniform microstructure, free from residual stresses that could compromise performance.
-
Isotropic Structure and Uniform Strength
- The isotropic structure created by isostatic pressing ensures uniform strength in all directions. This is critical for components subjected to multidirectional stresses in service.
- The uniform density and strength achieved through this process make it ideal for high-stress applications, such as turbine blades and medical implants.
-
Shape Flexibility
- Isostatic pressing offers unparalleled shape flexibility, allowing for the production of parts with complex geometries that cannot be achieved using uniaxial presses.
- This flexibility is particularly advantageous for custom or specialized components, where traditional manufacturing methods fall short.
In summary, isostatic pressing is a highly advantageous process for producing advanced materials with superior properties, complex shapes, and efficient material utilization. Its ability to apply uniform pressure, eliminate defects, and consolidate manufacturing steps makes it a preferred choice for industries requiring high-performance components.
Summary Table:
Advantage | Description |
---|---|
Uniform Pressure Application | Ensures consistent material properties and high density in complex shapes. |
High-Density Materials | Produces materials with superior structural integrity, ideal for aerospace and medical sectors. |
Complex Shape Production | Enables manufacturing of intricate geometries using elastomeric molds. |
Improved Mechanical Properties | Enhances fatigue resistance, ductility, and toughness by eliminating internal defects. |
Efficient Material Utilization | Minimizes waste and optimizes use of expensive materials like superalloys and titanium. |
Combination of Compaction & Sintering | Combines steps to create high-strength, dense structures. |
Consolidation of Manufacturing Steps | Reduces production time and costs by combining multiple processes. |
Relief of Thermal Stresses | Improves reliability by relieving stresses in cast, sintered, and 3D-printed parts. |
Isotropic Structure | Ensures uniform strength in all directions for high-stress applications. |
Shape Flexibility | Allows production of complex geometries unachievable with traditional methods. |
Ready to enhance your material performance with isostatic pressing? Contact our experts today to learn more!