Powder metallurgy (PM) is a versatile and efficient manufacturing process that offers numerous advantages, making it a preferred choice for producing high-performance parts across various industries. Key benefits include cost-effectiveness, material efficiency, and the ability to create complex shapes with precise properties. PM parts are known for their exceptional wear resistance, durability, and ability to withstand high temperatures, making them ideal for applications in automotive, aerospace, and machinery. Additionally, the process is environmentally friendly, with minimal waste and high material utilization. Below, we explore the advantages of powder metallurgy in detail, focusing on its applications, material properties, and economic and environmental benefits.
Key Points Explained:
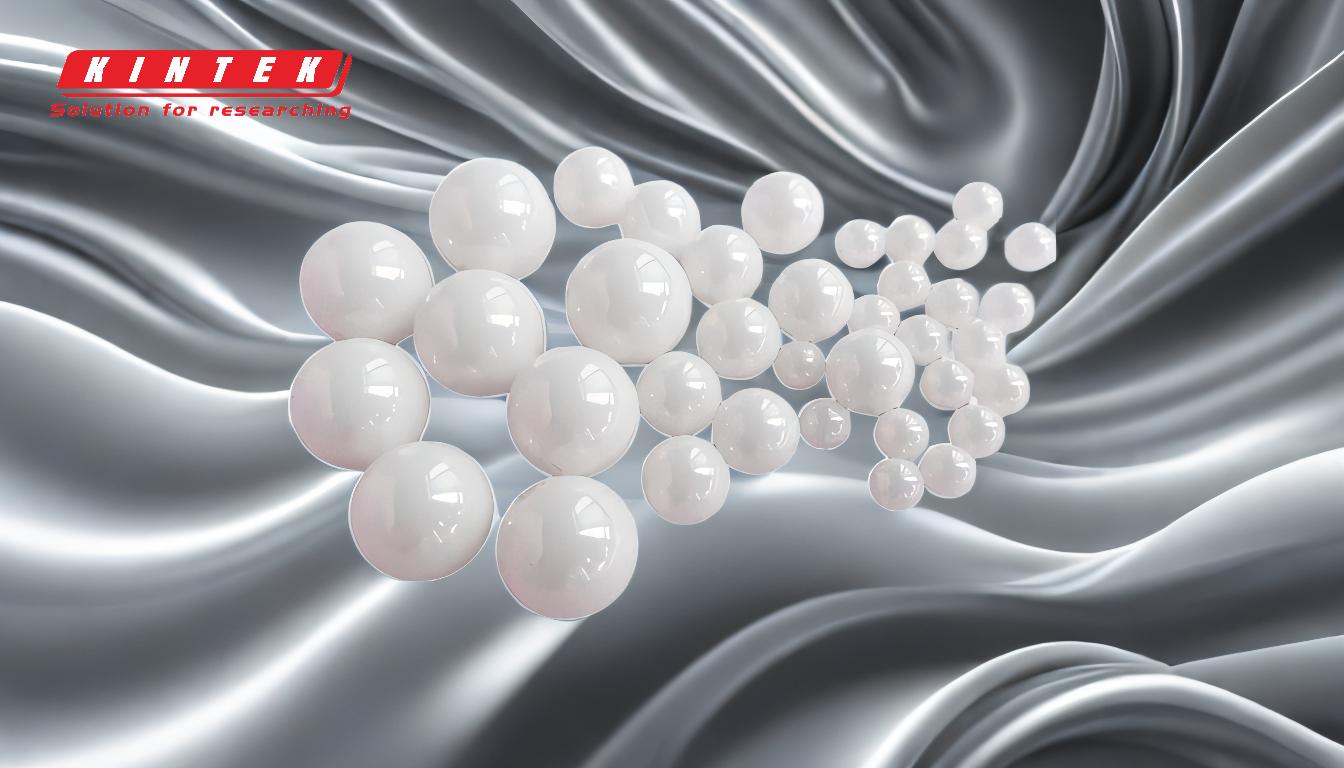
-
Cost-Effectiveness and Efficiency
- Powder metallurgy is a short and energy-efficient process, reducing production costs significantly.
- It eliminates the need for extensive machining, as parts are often produced in near-net shape, saving labor and material costs.
- High production rates for complex parts make it suitable for mass production, particularly in industries like automotive manufacturing.
-
Material Versatility and Control
- PM allows for the combination of materials with vastly different properties, such as metals with high melting points or varying densities. This is particularly useful for creating PTFE parts and other composite materials.
- Properties like electrical conductivity, magnetic characteristics, density, and hardness can be precisely controlled, enabling the production of parts tailored to specific applications.
- High-temperature sintering enhances mechanical properties, such as tensile strength and impact energy, making PM parts highly durable.
-
Complex Geometries and Precision
- The process can produce intricate shapes and configurations that are difficult or impossible to achieve with traditional manufacturing methods.
- Parts produced through PM have exceptional tolerances and uniformity, ensuring consistent performance in demanding applications.
-
Wear Resistance and Durability
- PM parts exhibit superior wear resistance and favorable friction coefficients, extending their lifespan in high-stress environments like automotive and aerospace systems.
- Hand tools made using PM, for example, last up to five times longer than those produced by other methods, showcasing the durability of PM components.
-
Environmental Benefits
- Powder metallurgy is an eco-friendly process, with 97% of the material used becoming part of the final product. This results in minimal waste and no scrap, aligning with sustainable manufacturing practices.
- The ability to recycle and reuse materials further reduces the environmental impact of PM production.
-
Applications in High-Performance Industries
- PM is widely used in the production of automotive components, where it offers higher densities and strength without the need for finishing or machining.
- It is also the preferred method for manufacturing refractory metal sputtering targets, which are critical in industries like electronics and coatings.
-
Advantages in Sintering
- PM sintering operates at lower temperatures compared to traditional methods, reducing energy consumption.
- The process achieves high sintering compactness and short sintering times, making it ideal for producing high-value-added materials, such as alloys with high melting points or poor castability.
In conclusion, powder metallurgy stands out as a highly efficient, versatile, and sustainable manufacturing process. Its ability to produce complex, high-performance parts with precise properties makes it indispensable in modern industries. Whether for PTFE parts or high-strength automotive components, PM continues to drive innovation and cost savings while minimizing environmental impact.
Summary Table:
Advantage | Description |
---|---|
Cost-Effectiveness | Reduces production costs with near-net shape parts and high production rates. |
Material Versatility | Combines materials with different properties for tailored applications. |
Complex Geometries | Produces intricate shapes with exceptional precision and uniformity. |
Wear Resistance & Durability | Offers superior wear resistance and longer lifespan in high-stress environments. |
Environmental Benefits | Minimizes waste with 97% material utilization and recyclable processes. |
High-Performance Applications | Ideal for automotive, aerospace, and machinery components. |
Efficient Sintering | Operates at lower temperatures, reducing energy consumption and sintering time. |
Unlock the potential of powder metallurgy for your industry—contact us today to learn more!