Screw extruders, particularly single screw extruders, offer a range of advantages that make them highly effective and efficient in various industrial applications. These advantages include advanced design, good plasticization, high quality output, low energy consumption, low noise levels, large bearing capacity, stable operation, and long life. These features collectively contribute to their widespread use in industries requiring precise and consistent material processing.
Key Points Explained:
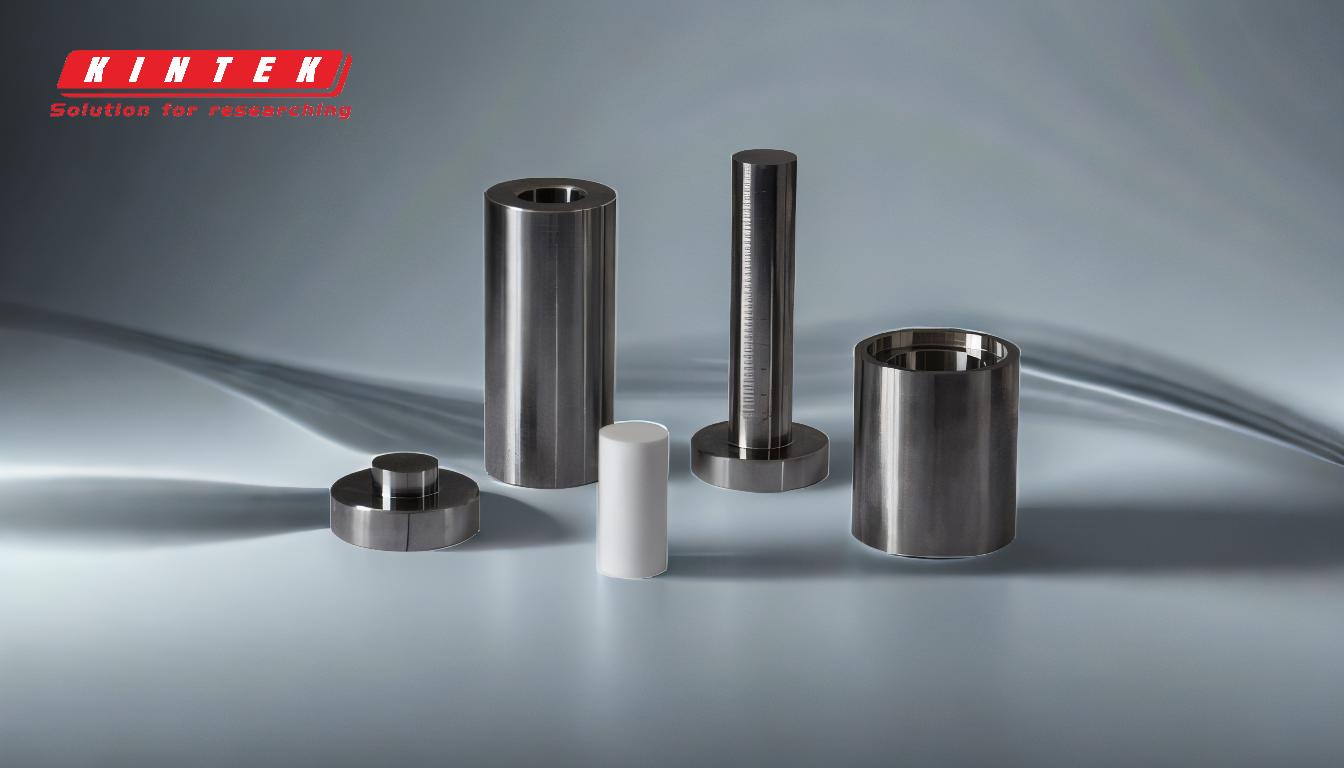
-
Advanced Design:
- Explanation: Single screw extruders are engineered with modern technology, ensuring they meet the demands of complex industrial processes. Their design often incorporates features that enhance performance, such as optimized screw geometry and robust construction materials. This advanced design allows for better control over the extrusion process, leading to more consistent and high-quality outputs.
-
Good Plasticization:
- Explanation: Plasticization refers to the process of melting and mixing materials to achieve a uniform consistency. Single screw extruders excel in this area due to their efficient screw design, which ensures thorough mixing and melting of materials. This results in a homogeneous product with consistent properties, which is crucial for applications requiring precise material characteristics.
-
High Quality:
- Explanation: The combination of advanced design and good plasticization leads to the production of high-quality extruded products. The consistent and uniform material processing ensures that the final products meet stringent quality standards, making them suitable for high-performance applications.
-
Low Energy Consumption:
- Explanation: Single screw extruders are designed to be energy-efficient. Their optimized screw design and efficient motor systems reduce the amount of energy required to operate the extruder. This not only lowers operational costs but also makes them more environmentally friendly by reducing energy consumption.
-
Low Noise:
- Explanation: The operation of single screw extruders is relatively quiet compared to other types of machinery. This is due to their stable and smooth operation, which minimizes vibrations and noise. Low noise levels are beneficial in creating a more comfortable and safer working environment.
-
Large Bearing Capacity:
- Explanation: Single screw extruders are capable of handling large volumes of material due to their robust construction and high load-bearing capacity. This makes them suitable for heavy-duty applications where large quantities of material need to be processed continuously.
-
Stable Operation:
- Explanation: Stability in operation is a key advantage of single screw extruders. Their design ensures consistent performance over long periods, reducing the likelihood of operational disruptions. This stability is crucial for maintaining productivity and ensuring the quality of the extruded products.
-
Long Life:
- Explanation: The durability and robust construction of single screw extruders contribute to their long operational life. High-quality materials and precision engineering ensure that these machines can withstand the rigors of continuous use, reducing the need for frequent maintenance and replacement. This longevity translates to lower long-term costs and greater reliability.
In summary, the advantages of screw extruders, particularly single screw extruders, make them an excellent choice for a wide range of industrial applications. Their advanced design, efficient plasticization, high-quality output, energy efficiency, low noise, large bearing capacity, stable operation, and long life collectively contribute to their effectiveness and reliability in material processing tasks.
Summary Table:
Advantage | Description |
---|---|
Advanced Design | Engineered with modern technology for precise control and consistent high-quality outputs. |
Good Plasticization | Ensures thorough mixing and melting, resulting in uniform and consistent material properties. |
High Quality Output | Produces extruded products that meet stringent quality standards for high-performance applications. |
Low Energy Consumption | Optimized design reduces energy use, lowering operational costs and environmental impact. |
Low Noise Levels | Smooth operation minimizes vibrations and noise, creating a safer and more comfortable workspace. |
Large Bearing Capacity | Robust construction handles heavy-duty applications and large material volumes. |
Stable Operation | Ensures consistent performance, reducing disruptions and maintaining productivity. |
Long Life | Durable materials and precision engineering ensure extended operational life and reliability. |
Ready to enhance your material processing with single screw extruders? Contact us today to learn more! For more information on related equipment, check out our precision cutting machine .