The sintering process is a highly advantageous manufacturing technique that offers a wide range of benefits, making it a popular choice in various industries. It enables the production of components with complex shapes and intricate designs, while also improving mechanical properties such as strength, conductivity, and corrosion resistance. Sintering is cost-effective, versatile in material selection, and environmentally friendly, as it reduces material waste and often eliminates the need for additional machining. Additionally, it allows for high production efficiency, excellent surface finishes, and precise tolerance control, making it suitable for both low- and high-volume production. Overall, sintering is a versatile and efficient process that meets the demands of modern manufacturing.
Key Points Explained:
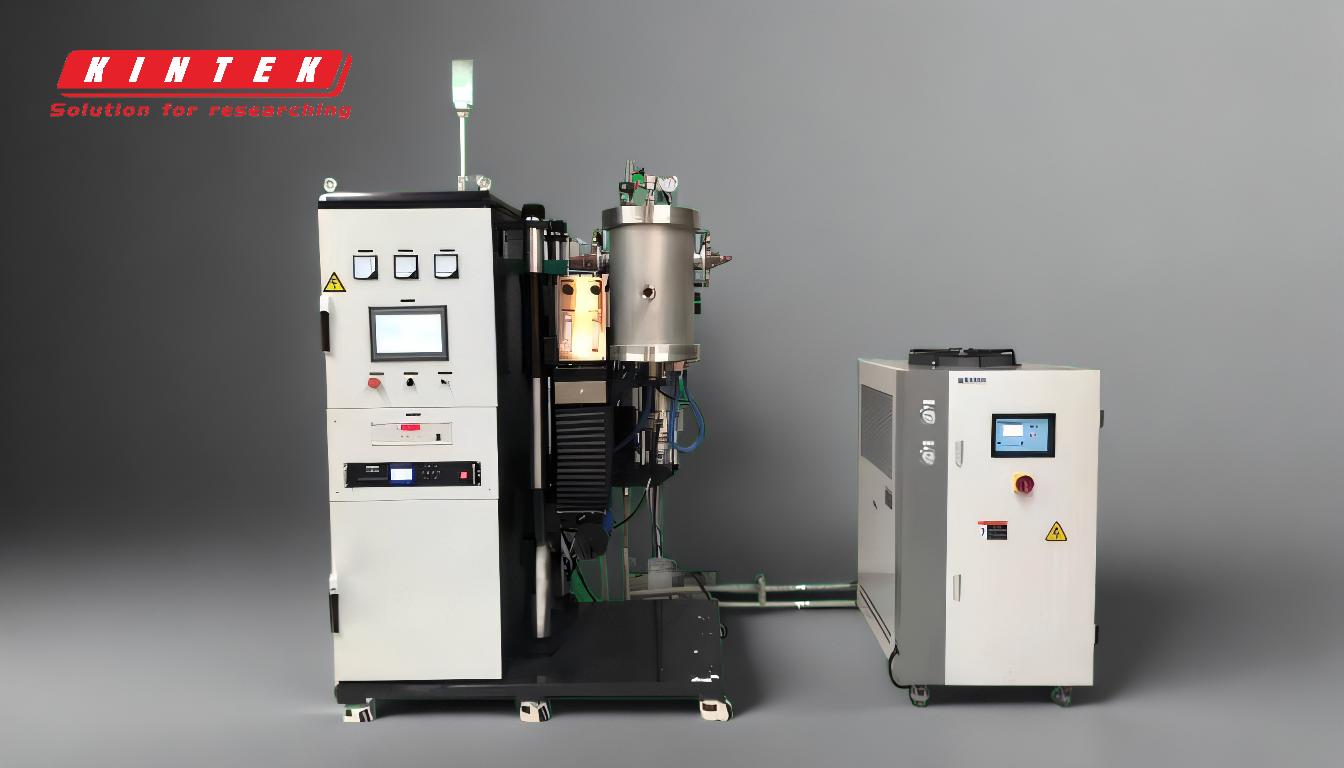
-
Ability to Produce Complex Shapes and Intricate Designs
- Sintering allows for the creation of highly complex parts and shapes that would be difficult or impossible to achieve with traditional manufacturing methods. This is particularly useful in industries like aerospace, automotive, and medical devices, where intricate designs are often required.
- The process reduces the need for further machining, saving time and resources while maintaining precision.
-
Improved Mechanical Properties
- Sintering enhances the mechanical properties of materials, such as tensile strength, hardness, and wear resistance. This is achieved by reducing surface porosity and creating denser, more uniform structures.
- Improved properties like conductivity, corrosion resistance, and thermal conductivity make sintered parts suitable for demanding applications.
-
Tailored Material Compositions
- The sintering process allows for the customization of material compositions, enabling manufacturers to create parts with specific properties tailored to their application. This includes blending different powders to achieve desired characteristics, such as enhanced strength or conductivity.
-
Cost-Effectiveness
- Sintering is a cost-effective manufacturing method, particularly for large-volume production. It minimizes material waste, as excess powder can often be reused, and reduces the need for additional finishing processes.
- The ability to produce parts with minimal machining further lowers production costs.
-
Versatility in Material Selection
- Sintering can be used with a wide range of materials, including metals, ceramics, and composites. This versatility makes it suitable for diverse applications across industries.
- It is particularly beneficial for materials that are difficult to process through melting and casting, such as those with high melting points or complex compositions.
-
High Production Efficiency
- The sintering process is highly efficient, allowing for rapid production of parts with consistent quality. This efficiency is beneficial for both low- and high-volume production runs.
- Faster startups and fewer process interruptions contribute to increased productivity.
-
Environmentally Friendly
- Sintering is an environmentally friendly process, as it generates minimal waste and often eliminates the need for harmful chemicals or finishing treatments.
- The ability to recycle excess powder further reduces its environmental impact.
-
Excellent Surface Finishes and Tolerance Control
- Sintered parts often have excellent surface finishes, reducing or eliminating the need for additional finishing processes.
- The process allows for precise control over tolerances, ensuring that parts meet strict dimensional requirements.
-
Non-Machinable Geometries for Mass Production
- Sintering enables the production of parts with non-machinable geometries, making it ideal for mass production of complex components.
- This capability is particularly valuable in industries where traditional machining methods are impractical or too costly.
In summary, the sintering process offers a unique combination of advantages, including the ability to produce complex parts, improve material properties, and achieve cost-effective, high-volume production. Its versatility, efficiency, and environmental benefits make it a preferred choice for manufacturers across various sectors.
Summary Table:
Advantage | Key Benefits |
---|---|
Complex Shapes & Intricate Designs | Enables production of difficult-to-manufacture parts, reducing machining needs. |
Improved Mechanical Properties | Enhances strength, conductivity, and corrosion resistance. |
Tailored Material Compositions | Customizes material properties for specific applications. |
Cost-Effectiveness | Reduces material waste and minimizes machining costs. |
Versatility in Material Selection | Works with metals, ceramics, and composites for diverse applications. |
High Production Efficiency | Ensures rapid, consistent production for low- and high-volume runs. |
Environmentally Friendly | Minimizes waste and eliminates harmful chemicals. |
Excellent Surface Finishes | Reduces or eliminates the need for additional finishing processes. |
Precise Tolerance Control | Ensures parts meet strict dimensional requirements. |
Non-Machinable Geometries | Ideal for mass production of complex components. |
Ready to leverage the sintering process for your manufacturing needs? Contact us today to learn more!