Torch brazing, while not explicitly detailed in the provided references, can be inferred to share some advantages with furnace brazing, given the similarities in the brazing process. However, torch brazing has its unique benefits, particularly in terms of flexibility, precision, and suitability for smaller-scale or more intricate projects. Below is a detailed exploration of the advantages of torch brazing, drawing parallels and distinctions from the furnace brazing advantages mentioned.
Key Points Explained:
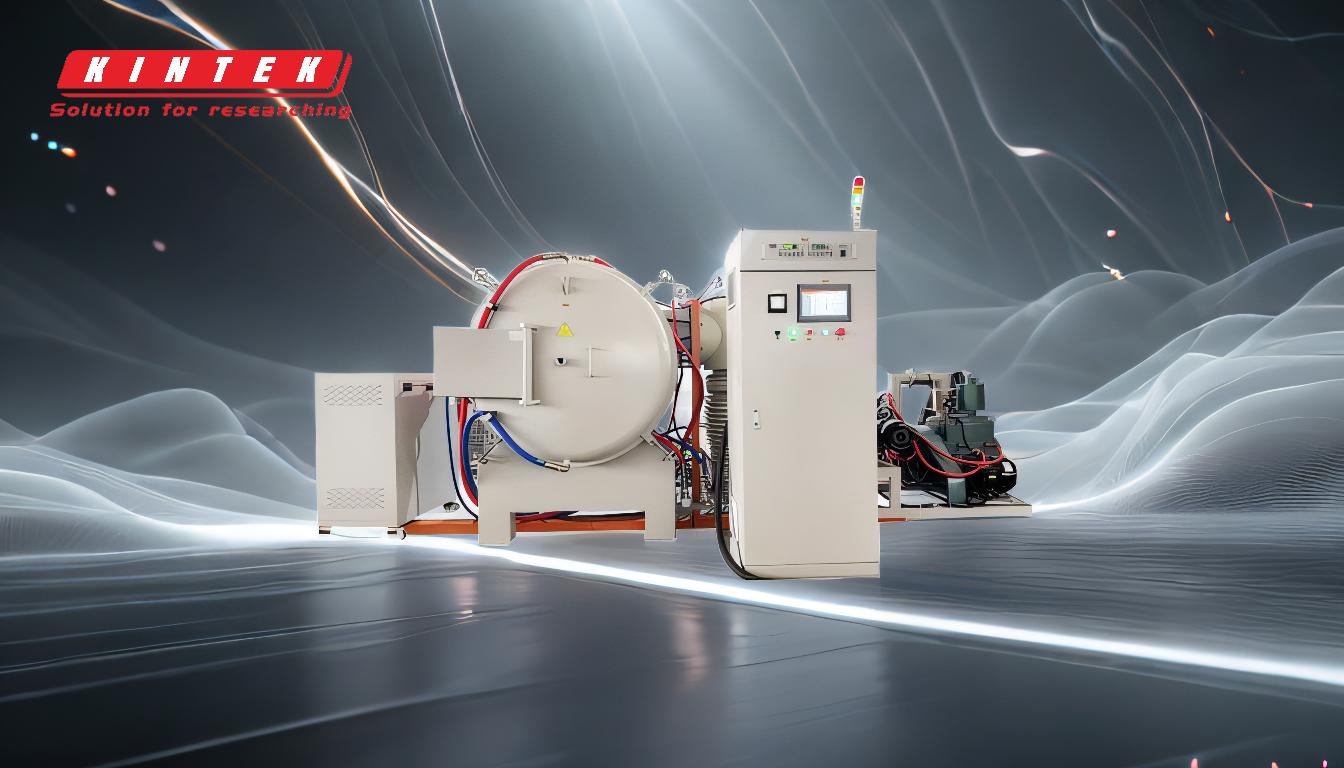
-
Flexibility in Application
- Torch brazing is highly versatile and can be used for a wide range of applications, from small, intricate components to larger assemblies. Unlike furnace brazing, which is better suited for mass production, torch brazing allows for manual control, making it ideal for custom or one-off projects.
- It is particularly useful for joining dissimilar materials, such as metals with different melting points, where precise heat control is necessary.
-
Precision and Control
- The manual nature of torch brazing provides greater control over the heat application, reducing the risk of overheating or damaging sensitive components. This precision is especially beneficial for delicate or complex parts that require localized heating.
- This level of control also allows for tighter tolerances and cleaner joints, as the operator can adjust the flame and heat distribution in real-time.
-
Cost-Effectiveness for Small-Scale Projects
- Torch brazing is often more cost-effective for small-scale or low-volume production runs. It does not require the significant upfront investment in equipment that furnace brazing does, making it accessible for smaller workshops or businesses.
- Additionally, the lower operator skill requirements compared to other welding techniques make it easier to train personnel, further reducing costs.
-
Material Versatility
- Like furnace brazing, torch brazing can join a wide range of materials, including dissimilar metals and non-metallic materials. This versatility makes it a valuable process in industries such as automotive, aerospace, and electronics.
- It is particularly effective for materials that are difficult to weld, such as cast iron or certain alloys, where the controlled heat of torch brazing prevents cracking or distortion.
-
Cleaner Joints and Reduced Thermal Distortion
- Torch brazing produces cleaner joints with minimal oxidation, as the localized heating reduces exposure to air. This results in stronger, more aesthetically pleasing joints.
- The controlled heat application also minimizes thermal distortion, preserving the integrity of the components being joined.
-
Portability and On-Site Repairs
- One of the standout advantages of torch brazing is its portability. Unlike furnace brazing, which requires a fixed setup, torch brazing equipment is lightweight and can be easily transported, making it ideal for on-site repairs or maintenance.
- This portability is particularly valuable in industries like construction or heavy machinery, where equipment failures may occur in remote locations.
-
Faster Lead Times for Small Batches
- For small batches or custom orders, torch brazing can often be completed more quickly than furnace brazing, as it does not require the setup and cooling times associated with furnace processes.
- This faster turnaround can be a significant advantage in industries where time-sensitive projects are common.
In summary, torch brazing offers a unique combination of flexibility, precision, and cost-effectiveness, making it an excellent choice for small-scale, intricate, or on-site applications. While it may not match the production speed or consistency of furnace brazing for large-scale manufacturing, its advantages in controlled heat application, material versatility, and portability make it an indispensable tool in many industries.
Summary Table:
Advantage | Description |
---|---|
Flexibility in Application | Ideal for small, intricate, or custom projects; suitable for dissimilar materials. |
Precision and Control | Manual heat control ensures cleaner joints and reduces overheating risks. |
Cost-Effectiveness | Lower equipment costs and easier operator training for small-scale production. |
Material Versatility | Joins a wide range of materials, including difficult-to-weld metals. |
Cleaner Joints | Minimizes oxidation and thermal distortion for stronger, aesthetically pleasing joints. |
Portability | Lightweight equipment enables on-site repairs and maintenance. |
Faster Lead Times | Quick turnaround for small batches or custom orders. |
Ready to leverage the benefits of torch brazing for your projects? Contact us today to learn more!