Vacuum carburization offers numerous advantages over traditional carburization methods, making it a preferred choice for modern manufacturing processes. It is faster, more energy-efficient, and environmentally friendly due to its lower temperature requirements and absence of harmful chemical emissions. The process ensures a more uniform carburized layer, reducing deformation and post-processing workload, particularly for complex parts like gears. Additionally, it integrates seamlessly into manufacturing systems, supports full automation, and provides precise control through computer simulations. These benefits make vacuum carburization ideal for industries requiring durable, high-performance components, such as aerospace, automotive, and rail sectors.
Key Points Explained:
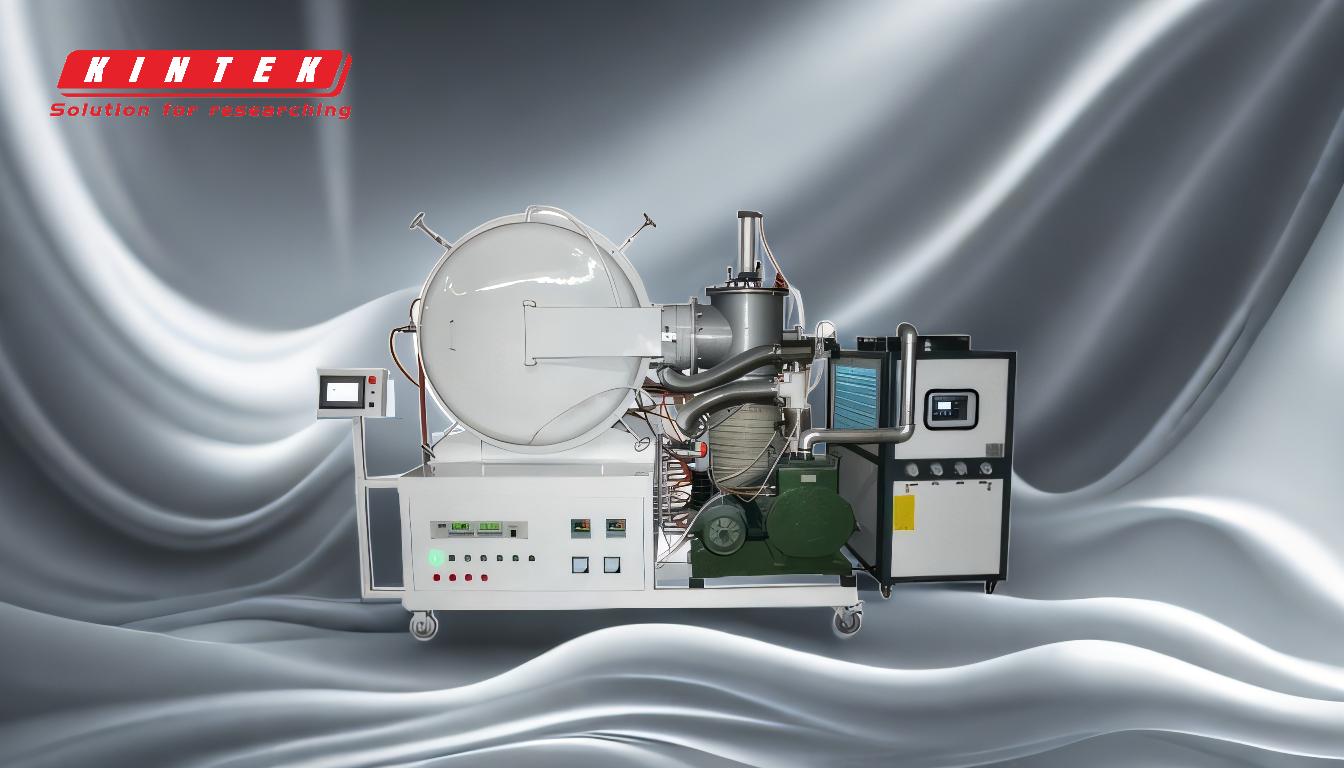
-
Faster Processing Time:
- Vacuum carburization is quicker than traditional methods because propane decomposes rapidly under heat, releasing carbon, hydrocarbon, and hydrogen. This accelerates the carburization process.
- Lower temperatures are required, reducing the time needed to reach the optimal carburization temperature. This efficiency translates to faster production cycles and cost savings.
-
Energy Efficiency:
- The process consumes energy only when needed, reducing overall energy consumption.
- Lower operating temperatures further contribute to energy savings, making it a cost-effective solution for manufacturers.
-
Environmental Friendliness:
- Unlike traditional methods that use solids or gases, vacuum carburization does not release harmful chemicals, making it an eco-friendly alternative.
- The absence of pollutants aligns with modern sustainability goals and regulatory requirements.
-
Uniform Carburized Layer:
- Vacuum carburization ensures a more uniform carburized layer, especially for parts with varying wall thicknesses, such as gears.
- Unlike gas carburizing, which can cause uneven heating and carburizing depth, vacuum carburizing heats parts uniformly from room temperature, adjusting the heating rate based on part geometry rather than wall thickness. This reduces deformation and minimizes the need for subsequent machining.
-
Improved Material Properties:
- The process enhances the toughness and durability of low-carbon steel, making it suitable for demanding applications in aerospace, automotive, and rail industries.
- It also prevents contamination and balances durability with machinability, ensuring high-quality end products.
-
Integration and Automation:
- Vacuum carburization can be easily integrated into existing manufacturing systems, supporting full automation.
- This capability enhances production efficiency and consistency, reducing the need for manual intervention.
-
Precise Process Control:
- The use of computer simulations allows for precise control over the carburization process, ensuring consistent results and high-quality outputs.
- Flexible cycles and the ability to operate at higher temperatures further enhance process adaptability.
-
Cost Savings:
- The combination of faster processing, lower energy consumption, and reduced post-processing requirements leads to significant cost savings.
- These economic benefits make vacuum carburization an attractive option for manufacturers looking to optimize their operations.
By leveraging these advantages, vacuum carburization not only improves product quality and performance but also supports sustainable and cost-effective manufacturing practices.
Summary Table:
Advantage | Description |
---|---|
Faster Processing Time | Propane decomposition accelerates carburization; lower temperatures save time. |
Energy Efficiency | Reduced energy consumption and lower operating temperatures cut costs. |
Environmental Friendliness | No harmful emissions, aligning with sustainability goals. |
Uniform Carburized Layer | Ensures even carburizing, reducing deformation and post-processing. |
Improved Material Properties | Enhances toughness and durability of low-carbon steel for demanding industries. |
Integration and Automation | Seamless integration into manufacturing systems with full automation support. |
Precise Process Control | Computer simulations enable consistent, high-quality results. |
Cost Savings | Faster processing, lower energy use, and reduced post-processing save costs. |
Ready to optimize your manufacturing process with vacuum carburization? Contact us today to learn more!