Induction and dielectric heating are versatile technologies with a wide range of industrial and commercial applications. Induction heating, which uses electromagnetic induction to heat conductive materials, is particularly prominent in industries such as metallurgy, automotive, semiconductor manufacturing, and food processing. It is used for surface hardening, melting, welding, brazing, annealing, and even in household appliances like induction cooktops. Dielectric heating, which involves heating insulating materials using high-frequency electric fields, is commonly used in food processing, wood drying, plastic welding, and medical applications. Both technologies offer precise temperature control, energy efficiency, and the ability to automate processes, making them indispensable in modern manufacturing and processing industries.
Key Points Explained:
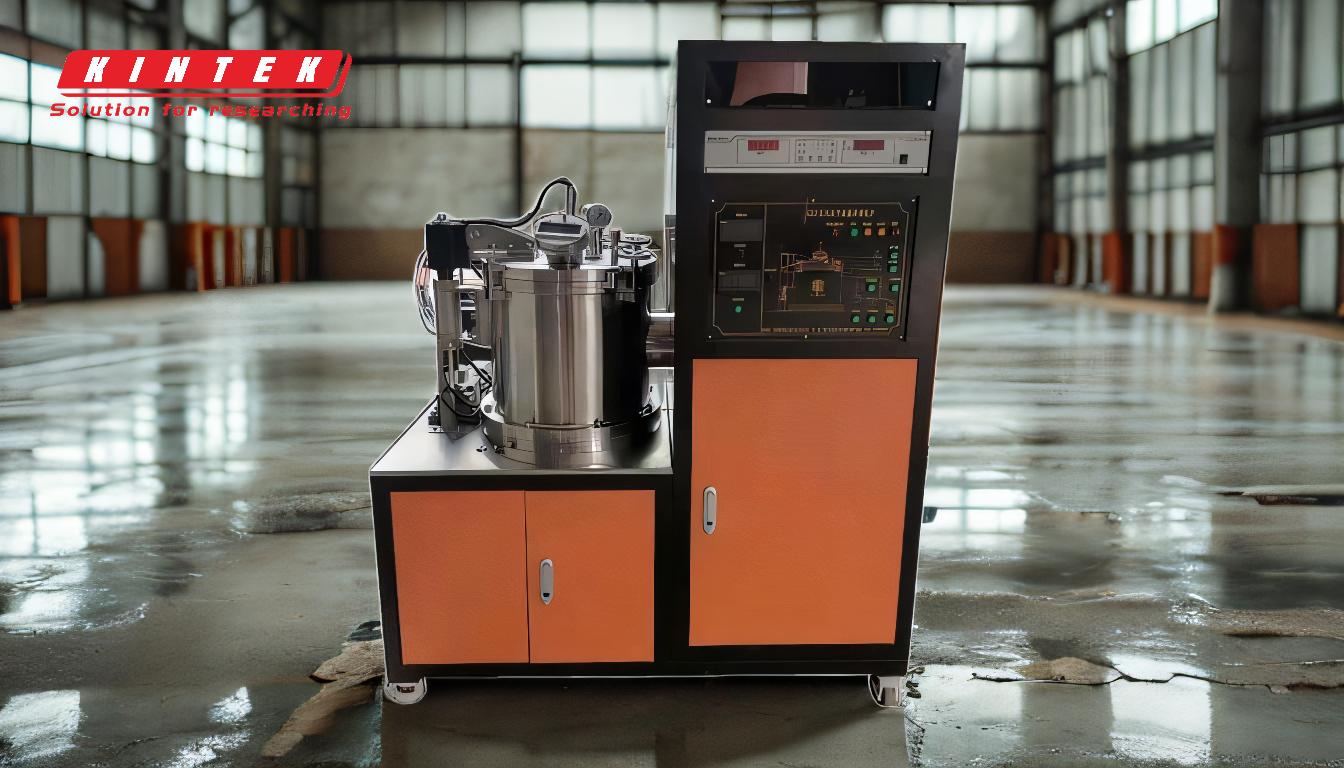
-
Industrial Applications of Induction Heating:
- Surface Hardening: Induction heating is widely used for surface hardening of steel parts. The process involves heating the surface to a high temperature using an alternating magnetic field and then quenching it to achieve a hard outer layer while keeping the core unaffected. This is commonly used in automotive and machinery components to improve wear resistance.
- Melting and Casting: Induction furnaces are used to melt metals, including refractory metals that require extremely high temperatures. This is essential in the production of specialized steel, alloys, and semiconductors.
- Welding and Joining: Induction heating is used for welding metals and joining components through brazing and soldering. It is also used for welding plastics doped with ferromagnetic ceramics.
- Heat Treatment: Processes like induction annealing and tempering are used to selectively soften or harden specific areas of metal parts, improving their mechanical properties.
-
Semiconductor and Electronics Industry:
- Crystal Growth: Induction heating is used in the Czochralski process for growing single crystals of silicon and other semiconductors.
- Zone Refining: This process, used in the semiconductor industry, involves melting a narrow zone of a material and moving it along the length of the material to purify it.
-
Household and Commercial Applications:
- Induction Cooktops: Induction heating is used in modern cooktops to heat cookware directly, offering faster and more energy-efficient cooking compared to traditional methods.
- Tamper-Resistant Sealing: Induction heating is used to seal caps on bottles and pharmaceutical containers, ensuring tamper resistance and product safety.
-
Emerging and Specialized Applications:
- Medical Applications: Induction heating is being explored for heating biological tissues in medical treatments, such as hyperthermia therapy for cancer.
- Low-Resistivity Materials: Research is ongoing to optimize induction heating for materials with low electrical resistivity, expanding its potential applications.
-
Advantages of Induction Heating:
- Contactless Heating: Induction heating does not require physical contact between the heat source and the material, reducing wear and tear.
- Precise Temperature Control: The ability to control heating parameters precisely ensures consistent and repeatable results, which is critical for high-quality manufacturing.
- Energy Efficiency: Induction heating is highly energy-efficient, as it directly heats the material without significant heat loss to the surroundings.
-
Dielectric Heating Applications:
- Food Processing: Dielectric heating is used for drying, cooking, and pasteurizing food products. It is particularly effective for heating materials with high moisture content.
- Wood Drying: High-frequency dielectric heating is used to dry wood quickly and uniformly, reducing drying times and improving product quality.
- Plastic Welding: Dielectric heating is used to weld thermoplastic materials, creating strong and durable bonds.
- Medical Applications: Dielectric heating is used in diathermy, a medical treatment that uses high-frequency electric currents to generate heat in body tissues for therapeutic purposes.
-
Future Trends and Research:
- Technological Advancements: Continued research is expected to expand the range of applications for both induction and dielectric heating, particularly in emerging fields like renewable energy and advanced materials.
- Process Optimization: Efforts are underway to optimize process parameters for new materials and applications, improving efficiency and reducing costs.
In conclusion, induction and dielectric heating are critical technologies with diverse applications across industries. Their ability to provide precise, efficient, and contactless heating makes them indispensable in modern manufacturing, processing, and even household applications. As technology advances, their use is expected to grow, enabling new and innovative applications.
Summary Table:
Technology | Key Applications | Advantages |
---|---|---|
Induction Heating | Surface hardening, melting, welding, brazing, annealing, induction cooktops | Contactless heating, precise temperature control, energy efficiency |
Dielectric Heating | Food processing, wood drying, plastic welding, medical diathermy | Uniform heating, effective for high-moisture materials, strong bonds creation |
Discover how induction and dielectric heating can transform your processes—contact us today for expert guidance!