Sintering is a versatile manufacturing process with a wide range of applications across various industries. It is primarily used to join metal particles, especially those with high melting points, without requiring the material to reach its melting temperature. This makes it energy-efficient and suitable for creating complex shapes, such as in 3D printing. Sintering also reduces surface porosity, enhancing material properties like strength and durability. Additionally, it plays a critical role in powder metallurgy, ceramics, glass manufacturing, and the production of filters and refractory metals. Its ability to form custom shapes and improve material characteristics makes it indispensable in modern manufacturing.
Key Points Explained:
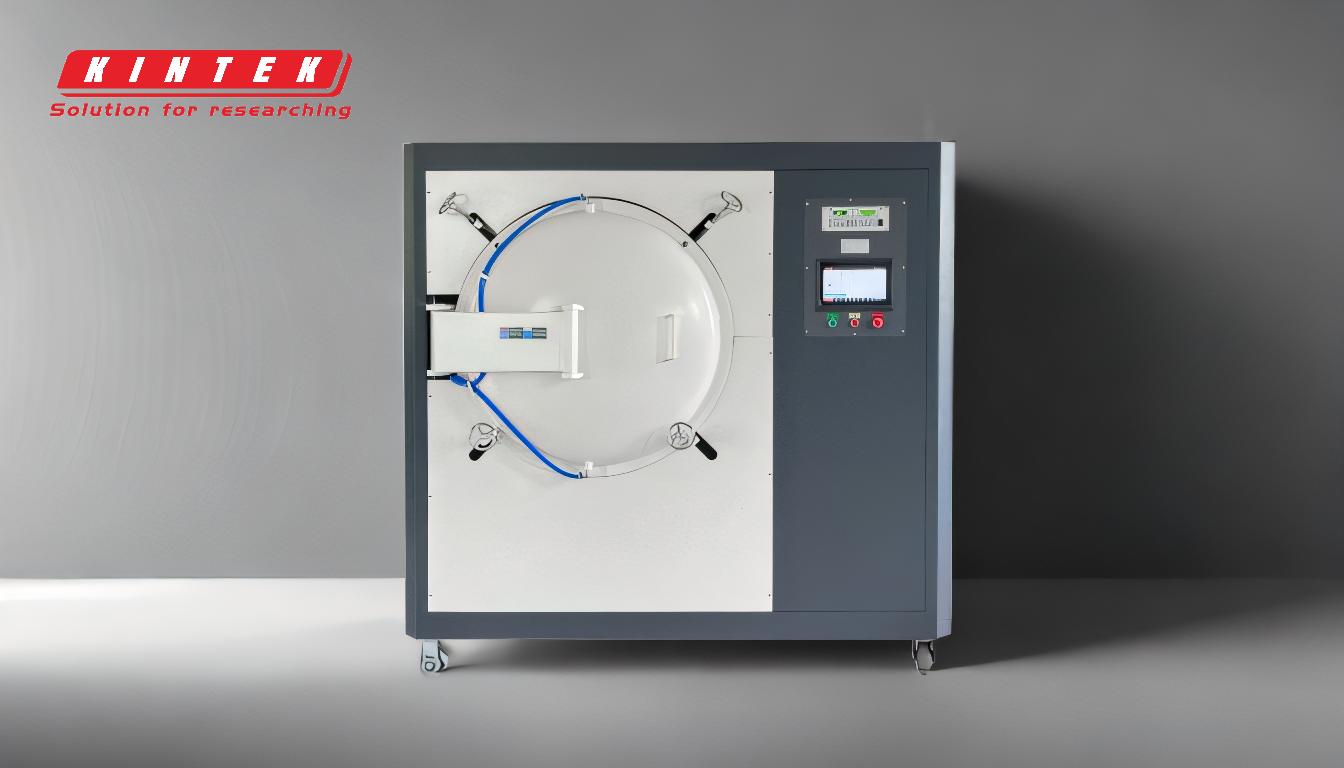
-
Joining Metal Particles, Especially High-Melting-Point Metals:
- Sintering is widely used to bind metal particles together, particularly for metals like tungsten and molybdenum, which have extremely high melting points.
- Since sintering does not require reaching the melting temperature of the material, it is a cost-effective and energy-efficient method for processing these metals.
- This application is crucial in industries like aerospace and electronics, where high-performance materials are required.
-
Additive Manufacturing and 3D Printing:
- Sintering is a key process in additive manufacturing, especially in 3D metal printing. It allows for the creation of custom metal shapes layer by layer.
- This method saves energy compared to traditional melting processes and offers greater control and consistency in producing complex geometries.
- Applications include prototyping, medical implants, and lightweight components for automotive and aerospace industries.
-
Reduction of Surface Porosity:
- Sintering reduces the porosity of a material's surface, which enhances its mechanical properties, such as strength, hardness, and wear resistance.
- This is particularly beneficial for materials used in high-stress environments, such as industrial machinery or cutting tools.
- Improved surface properties also make sintered materials suitable for applications requiring tight tolerances and smooth finishes.
-
Powder Metallurgy:
- Sintering is a fundamental process in powder metallurgy, where metal powders are compacted and heated to form solid parts.
- This technique is used to produce components like gears, bearings, and automotive parts, offering high precision and material efficiency.
- It is also used to create porous materials, such as filters and self-lubricating bearings.
-
Ceramics and Glass Manufacturing:
- Sintering is traditionally used in the production of ceramic objects, where it helps fuse ceramic particles into a solid structure.
- In glass manufacturing, sintering is used to create dense, high-strength glass components.
- These applications are essential in industries like construction, electronics, and consumer goods.
-
Production of Refractory Metals:
- Refractory metals, such as tungsten and molybdenum, are difficult to process using traditional melting methods due to their high melting points.
- Sintering allows these metals to be shaped and formed into usable components, such as filaments, electrodes, and heat shields.
- This makes sintering indispensable in industries like lighting, electronics, and high-temperature applications.
-
Creation of Sintered Filters and Plastics:
- Sintering is used to produce porous filters, such as sintered plastic and polyethylene (PE) filters, which are used in filtration systems for liquids and gases.
- These filters are valued for their durability, chemical resistance, and ability to trap fine particles.
- Sintered plastics are also used in applications requiring lightweight, high-strength materials, such as in the automotive and medical industries.
-
Steel Production via Iron Ore Sintering:
- In the steel industry, sintering is used to process iron ore mixed with coke, creating lumps suitable for burning in a blast furnace.
- This process improves the efficiency of steel production by reducing waste and optimizing material usage.
- It is a critical step in the manufacturing of steel, which is used in construction, infrastructure, and machinery.
-
Energy Efficiency and Environmental Benefits:
- Sintering is an energy-efficient process compared to melting, as it operates at lower temperatures.
- It also reduces material waste, making it an environmentally friendly manufacturing method.
- These benefits align with global efforts to reduce energy consumption and promote sustainable industrial practices.
-
Customization and Versatility:
- Sintering allows for the creation of highly customized and intricate shapes, making it suitable for specialized applications.
- Its versatility extends to a wide range of materials, including metals, ceramics, and plastics, enabling its use in diverse industries.
- This adaptability makes sintering a cornerstone of modern manufacturing and innovation.
By leveraging sintering, industries can achieve cost savings, improved material properties, and enhanced design flexibility, making it a critical process in today's advanced manufacturing landscape.
Summary Table:
Key Applications | Benefits |
---|---|
Joining high-melting-point metals | Cost-effective, energy-efficient, ideal for aerospace and electronics |
Additive manufacturing (3D printing) | Custom shapes, energy savings, precision in medical and automotive industries |
Surface porosity reduction | Enhanced strength, hardness, and wear resistance |
Powder metallurgy | High precision, material efficiency, porous filters, and self-lubricating parts |
Ceramics and glass manufacturing | Dense, high-strength components for construction and electronics |
Refractory metals production | Shapes tungsten, molybdenum for filaments, electrodes, and heat shields |
Sintered filters and plastics | Durable, chemical-resistant filters for liquids and gases |
Steel production | Efficient iron ore processing, reduced waste, optimized material usage |
Energy efficiency | Lower temperatures, reduced material waste, environmentally friendly |
Customization and versatility | Intricate shapes, adaptable to metals, ceramics, and plastics |
Unlock the potential of sintering for your manufacturing needs—contact our experts today!