Furnace brazing, particularly in a vacuum brazing furnace, offers numerous benefits that make it a preferred method for joining metals in industries such as aerospace, metallurgy, and particle physics. This process provides precise temperature control, uniform heating, and an oxygen-free environment, which ensures high-quality, contamination-free joints. Additionally, vacuum brazing eliminates the need for flux, reduces part distortion, and allows for the joining of materials that are otherwise unweldable. The process is also efficient, cost-effective, and environmentally friendly, making it ideal for producing complex components with tight tolerances and superior performance.
Key Points Explained:
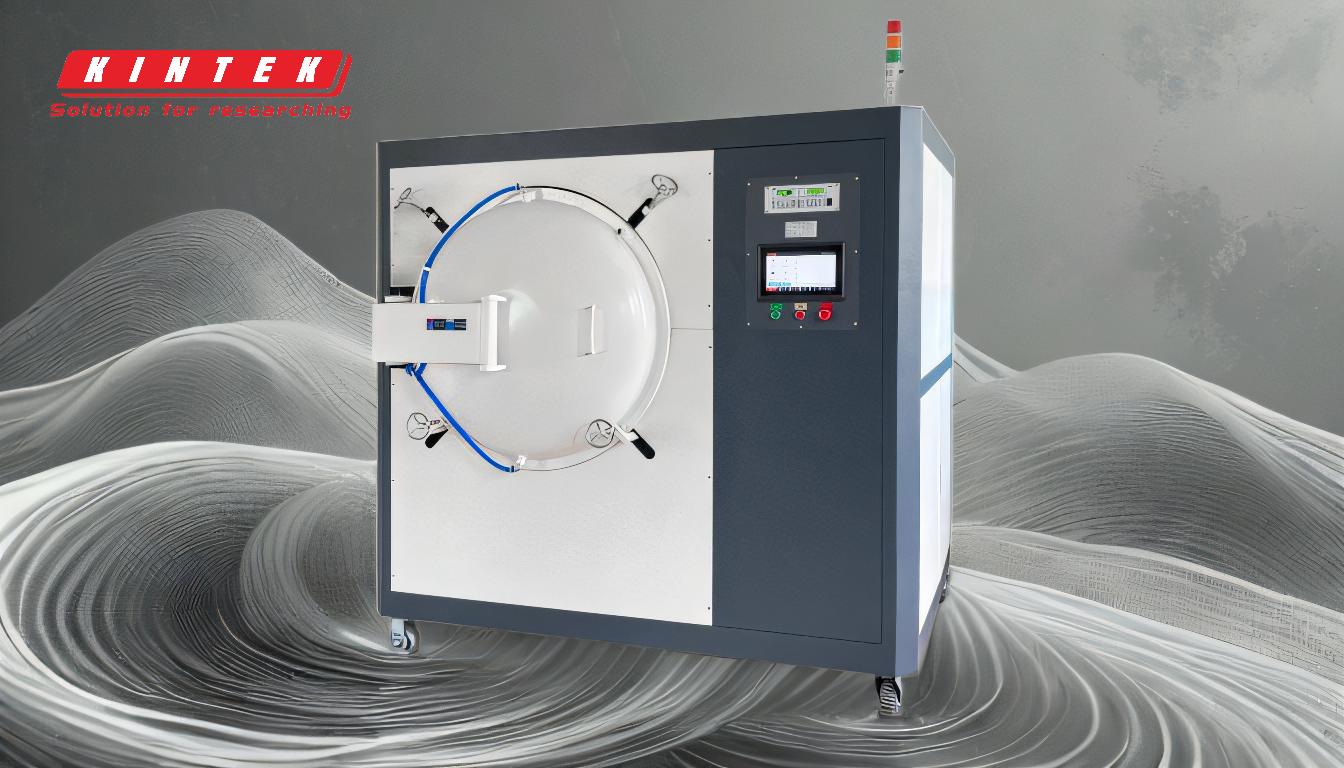
-
Precise Temperature Control and Uniform Heating:
- A vacuum brazing furnace operates within a controlled temperature range (typically 1100-1500°C), ensuring uniform heating across the workpiece. This uniformity is critical for achieving consistent metallurgical properties and high-quality brazed joints.
- The furnace's ability to maintain a uniform hot zone allows for identical heating cycles across multiple loads or continuous brazing of larger pieces, ensuring repeatability and precision.
-
Oxygen-Free Environment and Contamination Prevention:
- The vacuum environment eliminates oxidation and contamination from gases like carbon and oxygen, which can compromise the integrity of the brazed joint.
- The furnace operates at temperatures higher than oxide formation, enabling oxidized pieces to lose their oxide layer before brazing, resulting in cleaner and stronger joints.
-
Flux-Free Brazing:
- Vacuum brazing does not require flux, which eliminates the risk of corrosion caused by flux residues. This is particularly beneficial for applications in sensitive industries like aerospace and metallurgical research.
- The absence of flux also simplifies the post-brazing cleaning process, reducing production time and costs.
-
Reduced Part Distortion and Thermal Stress:
- The controlled heating and cooling cycles in a vacuum brazing furnace minimize thermal distortion, which is common in other metal joining processes like welding.
- This makes vacuum brazing ideal for joining complex or delicate components that require tight tolerances.
-
Ability to Join Unweldable Materials:
- Vacuum brazing can join materials that are difficult or impossible to weld, such as dissimilar metals or alloys containing active elements like aluminum and titanium.
- This capability is particularly valuable in industries like aerospace, where specialized alloys are often used.
-
Efficiency and Cost-Effectiveness:
- The process allows for the simultaneous brazing of multiple pieces, reducing production time and costs.
- Simple brazing fixtures are often sufficient, eliminating the need for expensive specialized equipment.
- The short production cycle, combined with the absence of pollution, makes vacuum brazing an environmentally friendly and economical choice.
-
Improved Product Performance:
- Vacuum brazing produces smooth and dense brazing seams, which enhance the mechanical and thermal properties of the joint.
- This results in components with improved heat-exchanging efficiency, longer service life, and better overall performance.
-
Compliance with Industry Standards:
- Vacuum brazing furnaces are designed to meet stringent industry standards, such as NADCAP requirements, ensuring high-quality and reliable results.
- Sophisticated cycle programming and barcode-linked systems allow for precise control and traceability, making the process suitable for high-precision applications.
In summary, furnace brazing, especially in a vacuum environment, offers unparalleled advantages in terms of quality, efficiency, and versatility. Its ability to produce clean, strong, and precise joints makes it an indispensable process for modern manufacturing and research applications.
Summary Table:
Benefit | Description |
---|---|
Precise Temperature Control | Ensures uniform heating (1100-1500°C) for consistent, high-quality joints. |
Oxygen-Free Environment | Prevents contamination and oxidation, ensuring cleaner, stronger joints. |
Flux-Free Brazing | Eliminates flux residues, reducing corrosion and simplifying cleaning. |
Reduced Part Distortion | Minimizes thermal stress, ideal for complex or delicate components. |
Joins Unweldable Materials | Enables brazing of dissimilar metals and alloys like aluminum and titanium. |
Efficiency and Cost-Effectiveness | Simultaneous brazing of multiple pieces reduces time and costs. |
Improved Product Performance | Produces smooth, dense seams for better mechanical and thermal properties. |
Compliance with Industry Standards | Meets NADCAP requirements, ensuring high-quality and traceable results. |
Ready to enhance your metal joining process? Contact us today to learn more about vacuum brazing furnaces!