Sintering ceramics offers numerous benefits, making it a critical process in advanced material manufacturing. It enhances material properties such as strength, durability, and conductivity while enabling the production of complex shapes with high precision. The process involves heating ceramic powders to high temperatures, leading to densification, reduced porosity, and improved mechanical and thermal properties. Sintering also allows for the creation of tailored material compositions, cost-effective production, and the ability to work with challenging materials. These advantages make sintering indispensable for applications requiring high-performance ceramics, such as in aerospace, electronics, and medical devices.
Key Points Explained:
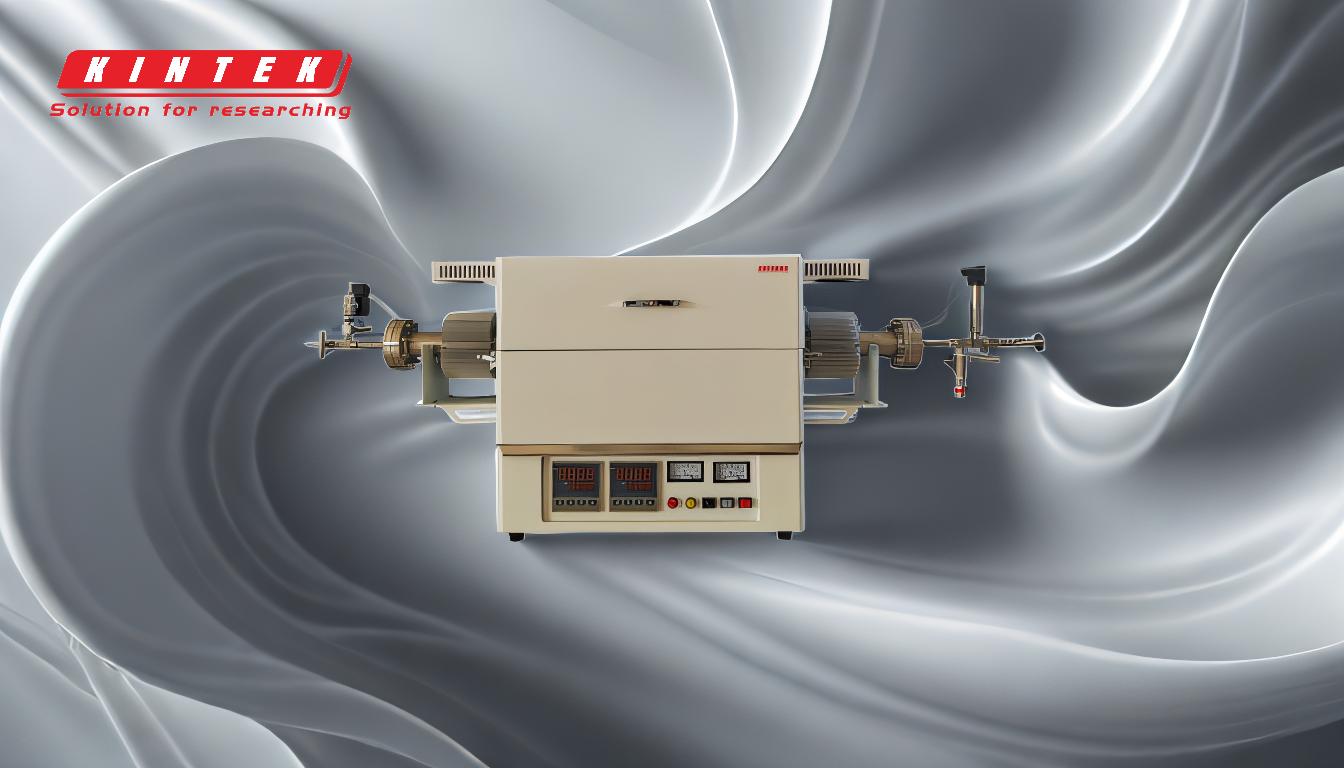
-
Improved Mechanical Properties:
- Sintering enhances the strength, toughness, and hardness of ceramics by reducing porosity and developing sintered necks between particles.
- This results in materials with high mechanical handling strength, making them suitable for demanding applications like turbine blades and structural components.
-
Enhanced Material Uniformity and Purity:
- The process ensures high levels of purity and uniformity in the starting materials, leading to consistent and repeatable operations.
- Controlled grain size and microstructure contribute to stable shapes and excellent properties.
-
Complex Shape Fabrication:
- Sintering enables the production of components with intricate designs and nearly net-shaped objects, which are difficult to achieve with traditional manufacturing methods.
- This capability is particularly useful for creating parts with precise geometries and intricate details.
-
Tailored Material Compositions:
- The process allows for the diffusion of elements like nickel, copper, and graphite, enabling the creation of customized material compositions with specific properties.
- This versatility is beneficial for applications requiring unique combinations of toughness, abrasion resistance, and other characteristics.
-
Cost-Effectiveness and Mass Production:
- Sintering reduces the need for expensive tooling and enables rapid mass production while maintaining precision and repeatability.
- This makes it a cost-effective solution for manufacturing high-performance ceramics in large quantities.
-
Improved Thermal and Electrical Properties:
- The process enhances properties such as thermal conductivity and electrical conductivity, making sintered ceramics suitable for applications in electronics and energy systems.
- It also improves transparency in certain ceramic materials, expanding their use in optical applications.
-
Versatility with Challenging Materials:
- Sintering is capable of processing materials with very high melting points, such as refractory metals and advanced ceramics.
- This makes it a valuable technique for working with materials that are otherwise difficult to manufacture.
-
Reduction of Surface Oxygen and Lubricants:
- The sintering process eliminates lubricants in compacted powders and reduces surface oxygen, leading to cleaner and more durable components.
- This contributes to the overall improvement of the part's properties.
-
Application-Specific Benefits:
- In some cases, sintering is used to increase strength while maintaining gas absorbency, making it ideal for filters or catalysts.
- The process is also critical for producing components with great hardness, toughness, and precision, which are essential in industries like aerospace and medical devices.
-
Transformation of Ceramic Powders:
- Sintering transforms ceramic powder into polycrystalline ceramic materials with specific properties, making it the most important step in preparing advanced ceramics.
- This transformation involves diffusion and mass transfer, resulting in densification and a uniform microstructure.
By leveraging these benefits, sintering ceramics provides a robust and versatile solution for producing high-performance materials tailored to meet the demands of modern industries.
Summary Table:
Benefit | Description |
---|---|
Improved Mechanical Properties | Increases strength, toughness, and hardness by reducing porosity. |
Enhanced Uniformity and Purity | Ensures high purity and uniformity for consistent results. |
Complex Shape Fabrication | Produces intricate designs and precise geometries with high accuracy. |
Tailored Material Compositions | Allows customization for specific properties like abrasion resistance. |
Cost-Effectiveness | Reduces tooling costs and enables mass production with precision. |
Improved Thermal/Electrical Props | Enhances conductivity and transparency for electronics and energy applications. |
Versatility with Challenging Mats | Processes high-melting-point materials like refractory metals and ceramics. |
Reduction of Surface Oxygen | Eliminates lubricants and reduces surface oxygen for cleaner, durable components. |
Application-Specific Benefits | Ideal for filters, catalysts, and components in aerospace and medical devices. |
Transformation of Ceramic Powders | Converts powders into polycrystalline ceramics with uniform microstructures. |
Ready to leverage sintering ceramics for your next project? Contact our experts today to get started!