Biomass gasification is a thermochemical process that converts biomass into a mixture of gases, known as syngas, and various byproducts. The primary byproducts of biomass gasification include ash, tars, char, and other hydrocarbons. These byproducts are generated due to the incomplete combustion of biomass and the complex chemical reactions occurring during the gasification process. Ash is the inorganic residue left after the biomass is gasified, while tars are complex organic compounds that can condense and cause operational issues if not properly managed. Char, a carbon-rich solid, is another byproduct that can be further processed or used as a fuel. Additionally, other hydrocarbons, such as methane and ethane, may be present in the gas stream. Understanding these byproducts is crucial for optimizing the gasification process and ensuring efficient utilization of biomass resources.
Key Points Explained:
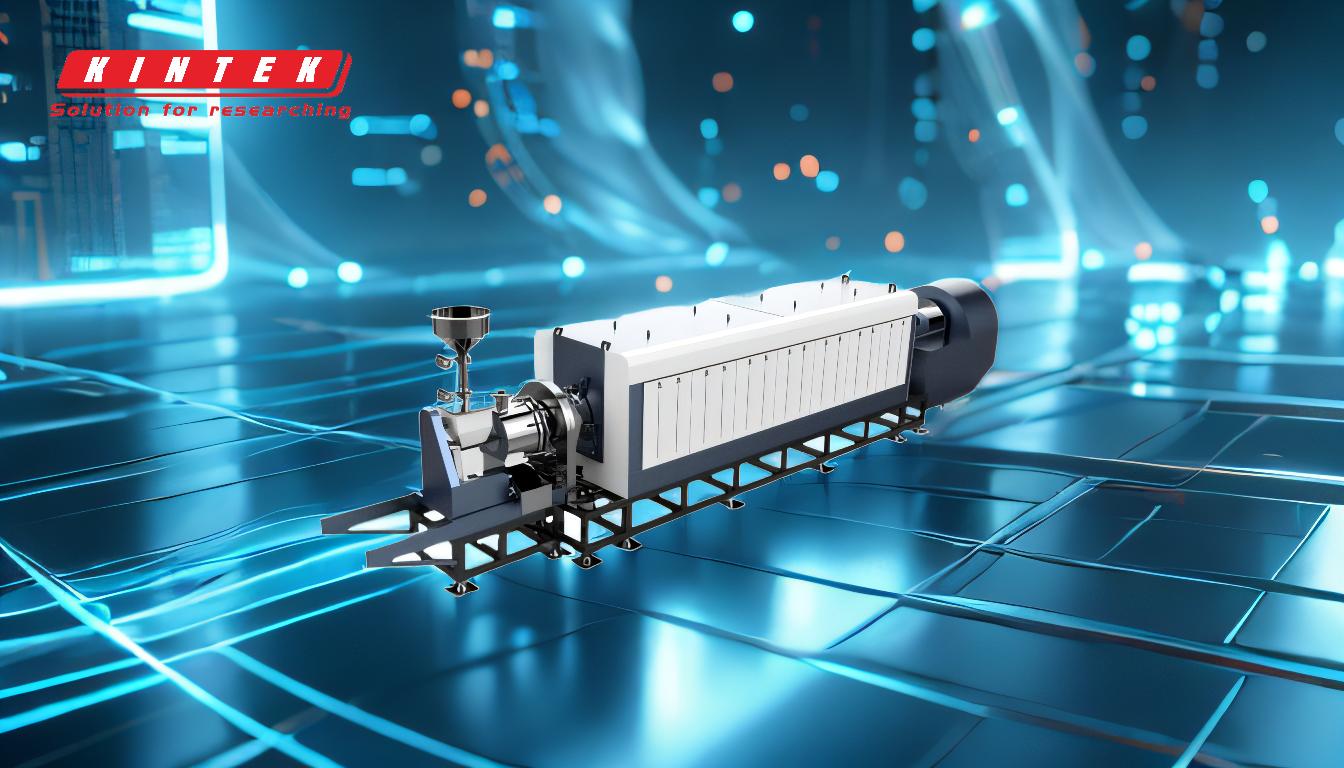
-
Ash:
- Description: Ash is the inorganic residue that remains after the biomass has been gasified. It consists of minerals and other non-combustible materials present in the original biomass.
- Significance: Ash content varies depending on the type of biomass used. High ash content can lead to operational challenges, such as slagging and fouling in the gasifier.
- Management: Proper ash management is essential to maintain the efficiency of the gasification process. Ash can be collected and disposed of or used in applications such as construction materials or soil amendment.
-
Tars:
- Description: Tars are complex organic compounds that form during the gasification process. They are typically composed of aromatic hydrocarbons and can condense at lower temperatures.
- Significance: Tars can cause operational issues, such as clogging and fouling of equipment, and can also reduce the quality of the syngas.
- Management: Tar removal is critical for the efficient operation of gasifiers. Techniques such as thermal cracking, catalytic reforming, and filtration are commonly used to reduce tar content in the syngas.
-
Char:
- Description: Char is a carbon-rich solid byproduct of gasification. It is formed when biomass is partially oxidized and contains a significant amount of fixed carbon.
- Significance: Char has potential applications as a fuel, soil amendment, or as a precursor for activated carbon production.
- Management: Char can be collected and further processed or used directly. Its utilization depends on the specific requirements of the gasification system and the intended end-use.
-
Other Hydrocarbons:
- Description: In addition to syngas, the gasification process can produce other hydrocarbons such as methane (CH₄), ethane (C₂H₆), and ethylene (C₂H₄).
- Significance: These hydrocarbons can contribute to the heating value of the syngas and may be separated and used as fuel or chemical feedstocks.
- Management: The presence of these hydrocarbons in the syngas can be beneficial, but their concentration must be controlled to avoid issues such as incomplete combustion or the formation of unwanted byproducts.
-
Syngas Composition:
- Description: The primary product of biomass gasification is syngas, which is a mixture of hydrogen (H₂), carbon monoxide (CO), carbon dioxide (CO₂), and other gases.
- Significance: The composition of syngas can vary depending on the type of biomass, gasification conditions, and the presence of byproducts.
- Management: The quality of syngas is crucial for its downstream applications, such as power generation or chemical synthesis. Proper management of byproducts, such as tars and ash, is essential to maintain syngas quality.
-
Environmental Considerations:
- Description: The byproducts of biomass gasification, such as tars and ash, can have environmental impacts if not properly managed.
- Significance: Effective management of these byproducts is necessary to minimize environmental pollution and ensure sustainable operation of the gasification process.
- Management: Techniques such as scrubbing, filtration, and catalytic conversion are used to reduce the environmental impact of gasification byproducts. Additionally, the utilization of byproducts, such as char and ash, in beneficial applications can contribute to the overall sustainability of the process.
-
Economic Considerations:
- Description: The economic viability of biomass gasification is influenced by the management and utilization of byproducts.
- Significance: Byproducts such as char and tars can have economic value if they are processed and used in other applications.
- Management: The development of efficient byproduct management strategies can enhance the economic feasibility of biomass gasification projects. This includes the development of markets for byproducts and the integration of byproduct utilization into the overall gasification process.
In summary, the byproducts of biomass gasification, including ash, tars, char, and other hydrocarbons, play a significant role in the overall efficiency, environmental impact, and economic viability of the gasification process. Proper management and utilization of these byproducts are essential for optimizing the gasification process and ensuring its sustainability.
Summary Table:
Byproduct | Description | Significance | Management Strategies |
---|---|---|---|
Ash | Inorganic residue from gasified biomass. | High ash content can cause slagging and fouling. | Collected for disposal or used in construction/soil amendment. |
Tars | Complex organic compounds that condense at lower temperatures. | Can clog equipment and reduce syngas quality. | Removed via thermal cracking, catalytic reforming, or filtration. |
Char | Carbon-rich solid byproduct. | Used as fuel, soil amendment, or for activated carbon production. | Collected and processed for specific applications. |
Hydrocarbons | Methane, ethane, and ethylene in the gas stream. | Enhance syngas heating value but require concentration control. | Managed to avoid incomplete combustion or unwanted byproducts. |
Optimize your biomass gasification process—contact our experts today for tailored solutions!