Graphene synthesis faces several challenges, primarily due to the complexity of achieving high-quality, large-scale production. The two main methods—bottom-up and top-down—each have their own set of difficulties. Bottom-up methods like chemical vapor deposition (CVD) require precise control over conditions such as temperature and substrate quality, while top-down methods like exfoliation struggle with scalability and consistency. Characterization techniques like Raman spectroscopy are essential but also come with limitations, such as background noise and overlapping spectral features, which complicate accurate analysis. These challenges highlight the need for continued innovation in both synthesis and characterization methods to make graphene more viable for industrial applications.
Key Points Explained:
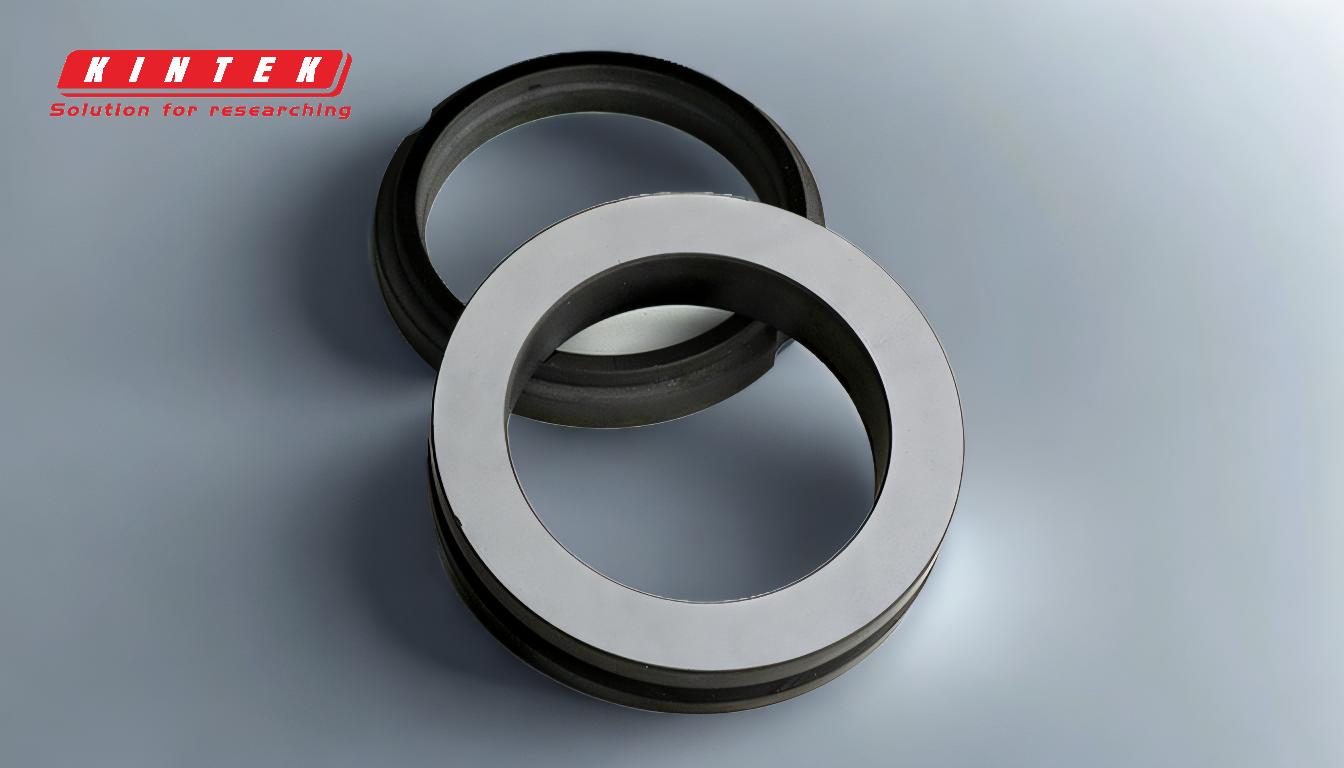
-
Bottom-Up Synthesis Challenges:
- Chemical Vapor Deposition (CVD): This method is the most promising for industrial-scale graphene production but is highly sensitive to process conditions. Precise control over temperature, pressure, and substrate quality is essential. Any deviation can lead to defects or inconsistent layer thickness.
- Epitaxial Growth and Arc Discharging: These methods can produce high-quality graphene but are limited by scalability and high costs. They are more suited for specialized applications rather than mass production.
-
Top-Down Synthesis Challenges:
- Exfoliation: Mechanical exfoliation can produce high-quality graphene but is not scalable. Chemical exfoliation methods, while more scalable, often introduce defects and impurities that degrade the material's properties.
- Chemical Oxidation: This method is scalable but typically results in graphene oxide, which requires additional reduction steps to restore some of graphene's properties. The final product often has residual defects and impurities.
-
Characterization Challenges:
- Raman Spectroscopy: While widely used, Raman spectroscopy has limitations. For instance, distinguishing between highly doped graphene and AB-stacked bilayer graphene can be difficult due to similar spectral features. Additionally, background noise from substrates like copper can reduce accuracy.
- Improving Accuracy: To mitigate these issues, averaging spectra from multiple points or mapped regions is recommended. This approach helps to reduce the impact of localized defects and substrate noise.
-
Industrial-Scale Production:
- Scalability: CVD is currently the only method capable of producing graphene on an industrial scale. However, achieving consistent quality across large areas remains a challenge. Advances in process control and substrate engineering are needed to improve scalability.
- Cost: High production costs are a significant barrier. Reducing costs through process optimization and the development of cheaper substrates is crucial for broader adoption.
-
Future Directions:
- Innovation in Synthesis: Continued research into new synthesis methods and the refinement of existing ones is essential. For example, developing more robust CVD processes or novel exfoliation techniques could address current limitations.
- Advanced Characterization: Improving characterization techniques to better understand and control graphene's properties will be key. This includes developing new spectroscopic methods or enhancing existing ones to provide more accurate and detailed information.
By addressing these challenges, the field can move closer to realizing the full potential of graphene in various applications, from electronics to energy storage.
Summary Table:
Aspect | Challenges |
---|---|
Bottom-Up Synthesis | - CVD: Sensitive to temperature, pressure, and substrate quality. |
- Epitaxial Growth/Arc Discharging: Limited scalability and high costs. | |
Top-Down Synthesis | - Exfoliation: Not scalable or introduces defects. |
- Chemical Oxidation: Produces graphene oxide with residual defects. | |
Characterization | - Raman Spectroscopy: Background noise and overlapping spectral features. |
Industrial-Scale | - Scalability: CVD struggles with consistent quality. |
- Cost: High production costs hinder adoption. | |
Future Directions | - Innovation in synthesis and advanced characterization techniques needed. |
Discover how advancements in graphene synthesis can benefit your projects—contact our experts today!