Welding stainless steel presents several challenges due to its unique properties, such as high thermal conductivity, susceptibility to distortion, and sensitivity to contamination. These challenges require careful consideration of welding techniques, material preparation, and post-weld treatments to ensure strong, corrosion-resistant joints. Key issues include managing heat input to prevent warping, avoiding contamination from carbon steel or other impurities, and selecting appropriate filler materials to match the base metal's composition. Additionally, stainless steel's tendency to form chromium carbides during welding can lead to reduced corrosion resistance, necessitating proper heat treatment or the use of low-carbon grades. Understanding these challenges is crucial for achieving high-quality welds in stainless steel applications.
Key Points Explained:
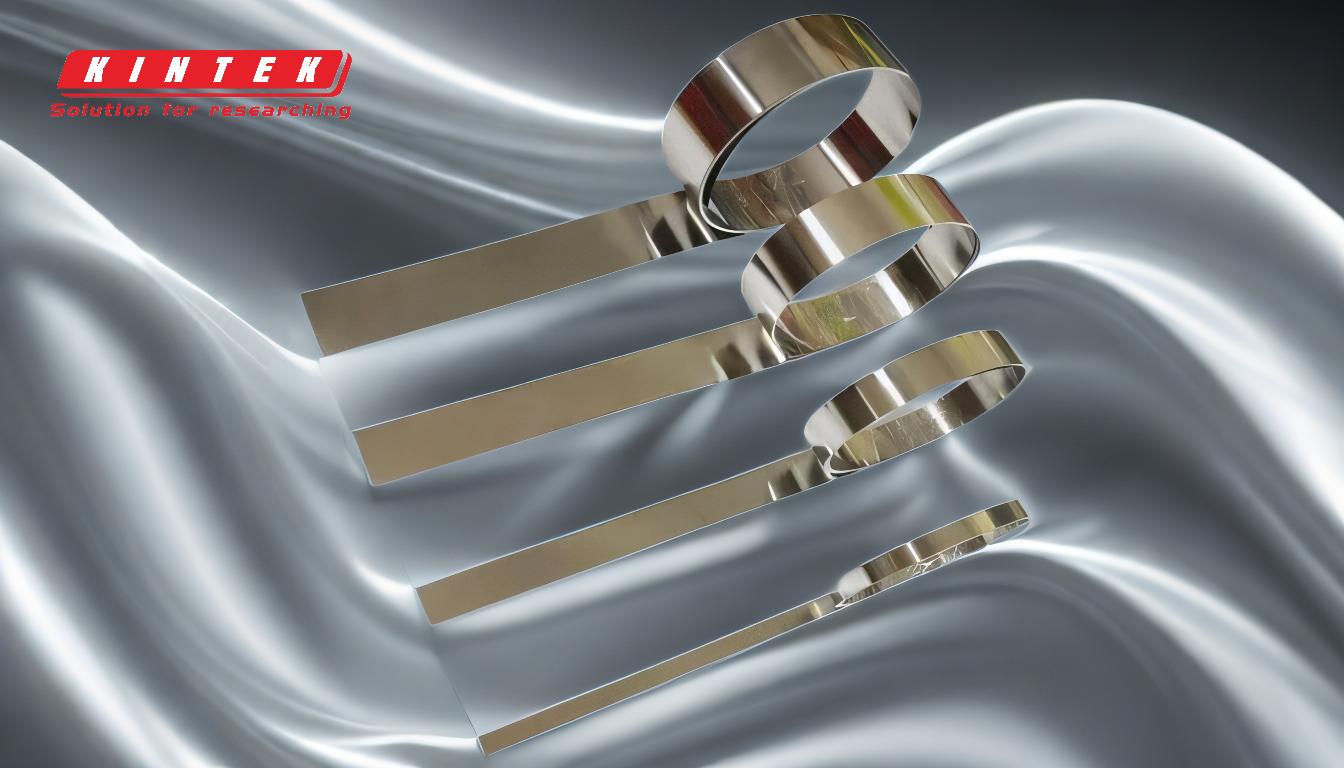
-
High Thermal Conductivity and Heat Management:
- Stainless steel has higher thermal conductivity compared to carbon steel, which means it dissipates heat more rapidly during welding. This can lead to uneven heating and cooling, increasing the risk of warping or distortion.
- To mitigate this, precise control of heat input is essential. Techniques such as pulsed welding or using lower amperage settings can help manage heat distribution and minimize distortion.
-
Susceptibility to Contamination:
- Stainless steel is highly sensitive to contamination from carbon steel, dirt, oils, or other impurities. Even small amounts of contamination can lead to weld defects, such as porosity or inclusions, and compromise the material's corrosion resistance.
- Proper cleaning of the base metal and welding environment is critical. Tools and equipment used for carbon steel should not be used for stainless steel to avoid cross-contamination.
-
Chromium Carbide Formation and Intergranular Corrosion:
- During welding, stainless steel can form chromium carbides at grain boundaries when exposed to temperatures between 450°C and 850°C. This depletes the chromium content in the surrounding areas, reducing the material's corrosion resistance.
- To prevent this, low-carbon grades of stainless steel (e.g., 304L or 316L) are often used. Alternatively, post-weld heat treatment or the use of stabilizing elements like titanium or niobium can help mitigate carbide formation.
-
Selection of Filler Materials:
- Choosing the correct filler material is crucial to match the composition of the base metal and maintain the weld's mechanical and corrosion-resistant properties. Mismatched filler materials can lead to weak joints or reduced performance.
- For example, when welding austenitic stainless steel, filler materials with similar nickel and chromium content are typically used to ensure compatibility.
-
Distortion and Residual Stresses:
- Stainless steel's lower thermal expansion coefficient compared to carbon steel can lead to significant residual stresses and distortion after welding. This is particularly problematic in thin sections or complex geometries.
- Techniques such as backstep welding, clamping, or preheating can help control distortion. Additionally, stress-relieving treatments may be required for critical applications.
-
Oxidation and Discoloration:
- Stainless steel is prone to oxidation and discoloration during welding, especially in the heat-affected zone (HAZ). This not only affects the appearance but can also reduce corrosion resistance.
- Using inert shielding gases, such as argon or helium, and ensuring proper gas coverage can minimize oxidation. Post-weld cleaning with pickling paste or passivation treatments can restore the material's surface properties.
-
Specialized Welding Techniques:
- Certain stainless steel grades, such as duplex or martensitic stainless steels, require specialized welding techniques due to their unique microstructures and properties.
- For example, duplex stainless steels require precise heat input to maintain a balanced austenite-ferrite microstructure, while martensitic grades may need preheating and post-weld heat treatment to prevent cracking.
By addressing these challenges through careful planning, material selection, and welding practices, high-quality welds in stainless steel can be achieved, ensuring durability and performance in demanding applications.
Summary Table:
Challenge | Key Considerations |
---|---|
High Thermal Conductivity | Use pulsed welding or lower amperage to manage heat input and minimize distortion. |
Susceptibility to Contamination | Clean base metal thoroughly; avoid cross-contamination from carbon steel tools. |
Chromium Carbide Formation | Use low-carbon grades (e.g., 304L, 316L) or stabilize with titanium/niobium. |
Filler Material Selection | Match filler material to base metal composition for compatibility and performance. |
Distortion and Residual Stresses | Use backstep welding, clamping, or preheating to control distortion. |
Oxidation and Discoloration | Use inert shielding gases and post-weld cleaning to restore surface properties. |
Specialized Welding Techniques | Apply precise heat input for duplex grades; preheat and post-weld treat martensitic. |
Struggling with stainless steel welding challenges? Contact our experts today for tailored solutions!