Sintering in ceramics is a critical process that transforms powdered materials into dense, strong, and durable components. It involves heating ceramic powders below their melting point to facilitate particle bonding and densification. The process is influenced by factors such as temperature, pressure, particle size, and the sintering atmosphere. These variables directly affect the microstructure, including grain size, pore distribution, and grain boundaries, which in turn determine the material's mechanical and physical properties. Understanding the characteristics of sintering is essential for optimizing the process to achieve desired product properties, such as strength, durability, and porosity.
Key Points Explained:
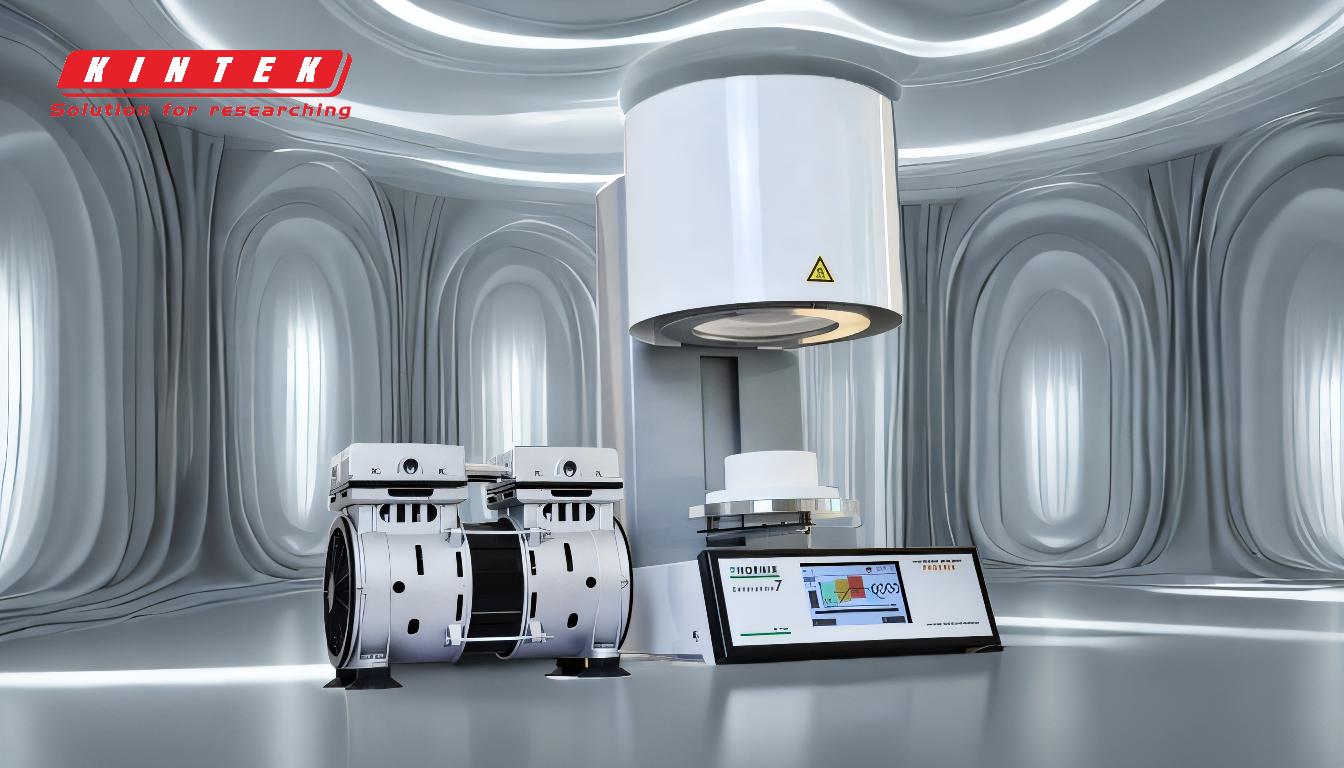
-
Dependence on Initial Porosity and Sintering Conditions:
- The final porosity of sintered ceramics is influenced by the initial porosity of the green compact and the sintering conditions, including temperature and duration.
- Higher temperatures and longer sintering times are required for pure oxide ceramics due to solid-state particle diffusion.
- Applying pressure during sintering can reduce porosity and shorten the sintering time.
-
Impact of Sintering Variables:
- Atmosphere: The sintering atmosphere (air, vacuum, or inert gases like argon/nitrogen) affects the material's properties by influencing oxidation or reduction reactions.
- Temperature: High-temperature sintering enhances properties such as tensile strength, bending fatigue strength, and impact energy.
- Cooling Rate: The cooling rate post-sintering can affect the microstructure and residual stresses in the material.
-
Microstructural Changes:
- Sintering alters the grain size, pore size, and grain boundary distribution in the material's microstructure.
- These changes directly influence the material's mechanical properties, such as strength, durability, and thermal stability.
-
Optimization of Sintering Parameters:
- The optimal sintering process depends on parameters like sintering temperature, applied pressure, average grain size, and the gaseous atmosphere.
- Finer powders and higher temperatures can increase compaction, but the liquid phase must be carefully controlled to avoid defects.
- The choice of sintering parameters is tailored to achieve the desired product properties while considering limiting factors.
-
Techniques and Methods:
- Different sintering techniques are employed based on the use of electrical currents, pressure, heat sources, and the specific materials being sintered.
- For example, pressure-assisted sintering methods like hot pressing or spark plasma sintering can enhance densification and reduce sintering time.
-
Sintering in Metallurgy vs. Ceramics:
- In metallurgy, sintering involves melting metal powders and alloying elements in a controlled furnace environment, with temperatures always below the material's melting point.
- In ceramics, sintering primarily relies on solid-state diffusion, and the process is tailored to achieve full densification without melting.
-
Importance of Sintering for Material Properties:
- Sintering is essential for producing fully dense ceramic parts with the desired mechanical and thermal properties.
- The process ensures that the final product exhibits characteristics such as high strength, durability, and resistance to wear and corrosion.
-
Influencing Factors:
- Temperature: Determines the kinetics of sintering and the resulting material properties.
- Heating Rate: Affects the densification process, with slower rates often leading to more uniform microstructures.
- Pressure: Enhances particle rearrangement and reduces porosity, leading to higher density.
- Particle Size and Composition: Smaller particles and homogeneous compositions promote better densification and uniform properties.
By carefully controlling these factors, manufacturers can optimize the sintering process to produce high-quality ceramic components with tailored properties for specific applications.
Summary Table:
Key Factor | Impact on Sintering |
---|---|
Temperature | Higher temperatures enhance particle bonding and improve mechanical properties. |
Pressure | Reduces porosity and shortens sintering time for denser materials. |
Atmosphere | Influences oxidation/reduction reactions, affecting material properties. |
Particle Size | Smaller particles promote better densification and uniform properties. |
Cooling Rate | Affects microstructure and residual stresses in the final product. |
Optimize your ceramic sintering process—contact our experts today for tailored solutions!