Heat treatment is a critical process in metallurgy and material science, used to alter the physical and sometimes chemical properties of materials, primarily metals. The process involves controlled heating and cooling to achieve desired material characteristics such as hardness, strength, ductility, and resistance to wear and corrosion. The effectiveness of heat treatment depends on precise control over temperature, time, and cooling rates, tailored to the specific material and desired outcomes. Key considerations include the selection of appropriate heating elements and furnaces, understanding the material's response to heat, and ensuring uniform temperature distribution and proper gas circulation. The choice of heat treatment method—whether for the entire part or specific areas—depends on the part's design, material, and intended application, aiming to enhance performance and durability while minimizing potential issues like maintenance or downtime.
Key Points Explained:
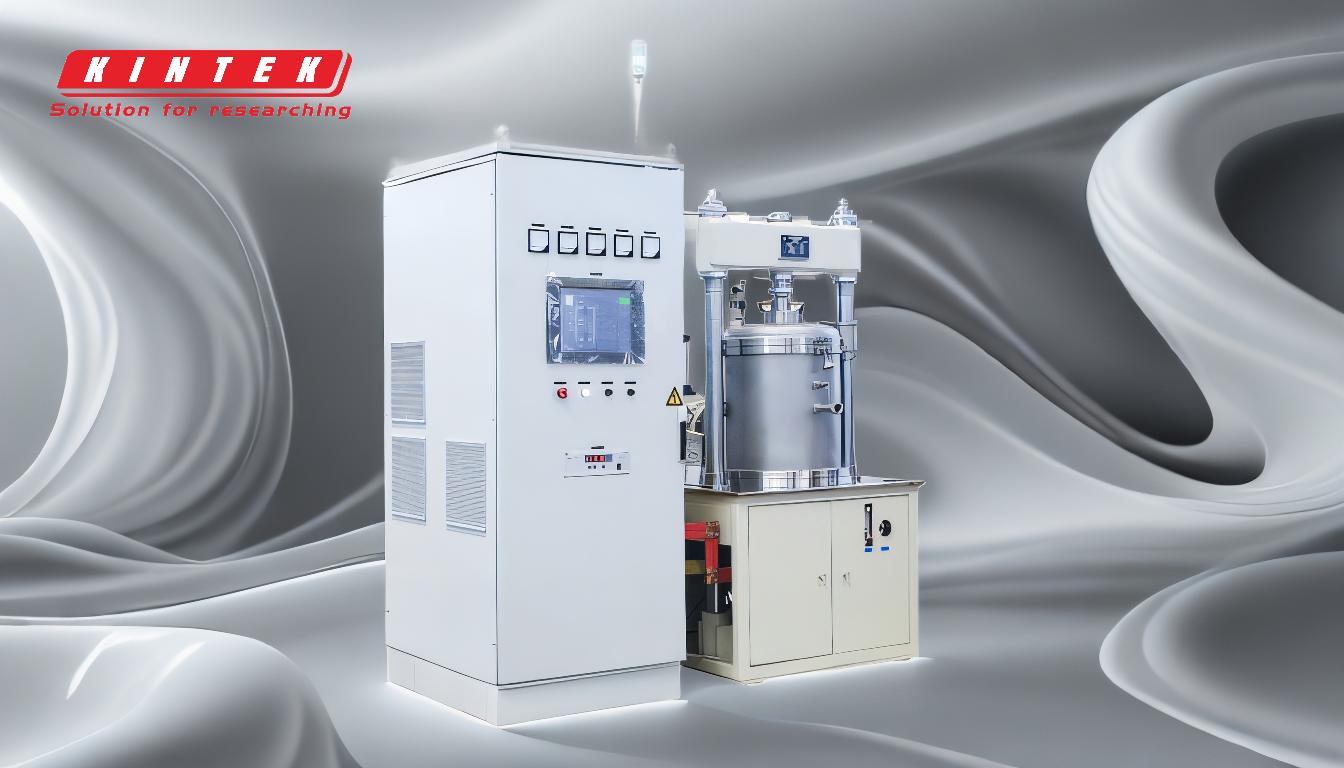
-
Temperature Control and Tolerances:
- Importance: Precise temperature control is essential in heat treatment to ensure the material reaches the necessary state for desired property changes.
- Details: This involves maintaining tight tolerances on maximum temperatures, controlling heat-up and cool-down rates, and optimizing process time without compromising metallurgical quality. For example, overheating can lead to grain growth, while insufficient heating may not achieve the desired hardness.
-
Variables Influencing Heat Treatment Outcomes:
- Temperature: The specific temperature to which the material is heated, which varies based on the material type and desired properties.
- Time: The duration the material is held at the target temperature, affecting the depth and uniformity of the treatment.
- Cooling Method and Rate: The technique and speed of cooling (e.g., quenching, air cooling) determine the final microstructure and properties.
-
Selection of Heating Elements and Furnaces:
- Heating Elements: Chosen based on their maximum temperature capabilities and suitability for specific applications. For instance, silicon carbide elements are used for high-temperature applications.
- Furnaces: Selected according to material type, temperature requirements, and production volume. Factors like uniform temperature distribution and gas circulation are critical for consistent results.
-
Heat Treatment Methods:
- Whole-Part Hardening: Processes like furnace hardening or carburizing are used when the entire part needs to be treated.
- Selective Hardening: Techniques such as flame or induction heat treating are employed for hardening specific areas, useful for parts requiring localized strength.
-
Factors Affecting Final Product Quality:
- Uniform Temperature Distribution: Ensures consistent treatment across the material.
- Gas Circulation: Proper control of partial pressure or quench gas is vital for achieving desired properties.
- Cycle Times and Temperatures: Optimized to balance efficiency and quality.
- Maintenance and Downtime: Anticipating potential issues helps in minimizing disruptions and ensuring consistent output.
-
Project-Specific Considerations:
- Material and Desired Outcome: The choice of heat treatment method depends on the material being used and the intended result, such as hardening, drying, or shaping.
- Part Design and Application: The end use of the part dictates whether the entire part or specific areas need treatment, influencing the selection of the most suitable heat treatment process.
By carefully considering these factors, heat treatment processes can be tailored to achieve the desired material properties, ensuring optimal performance and longevity of the treated components.
Summary Table:
Key Aspect | Details |
---|---|
Temperature Control | Ensures precise heating and cooling for desired material changes. |
Variables Influencing | Temperature, time, and cooling method affect outcomes. |
Heating Elements/Furnaces | Selected based on material type, temperature, and application needs. |
Heat Treatment Methods | Whole-part or selective hardening for specific material requirements. |
Quality Factors | Uniform temperature, gas circulation, and optimized cycle times. |
Project Considerations | Material type, part design, and intended application guide the process. |
Optimize your heat treatment process for superior results—contact our experts today!