An electric arc furnace (EAF) is a complex system designed for melting metals using electrical energy. Its primary components include the roof, hearth, electrodes, side walls, and various auxiliary systems such as tilting mechanisms, cooling systems, and fume extraction systems. The roof typically has holes for electrode insertion and is made of heat-resistant materials like alumina and magnesite-chromite bricks. The hearth holds the molten metal and slag, while the electrodes generate the arc necessary for melting. Additional systems like the tilting mechanism, cooling systems, and fume extraction ensure efficient and safe operation. Understanding these components is crucial for equipment purchasers to make informed decisions.
Key Points Explained:
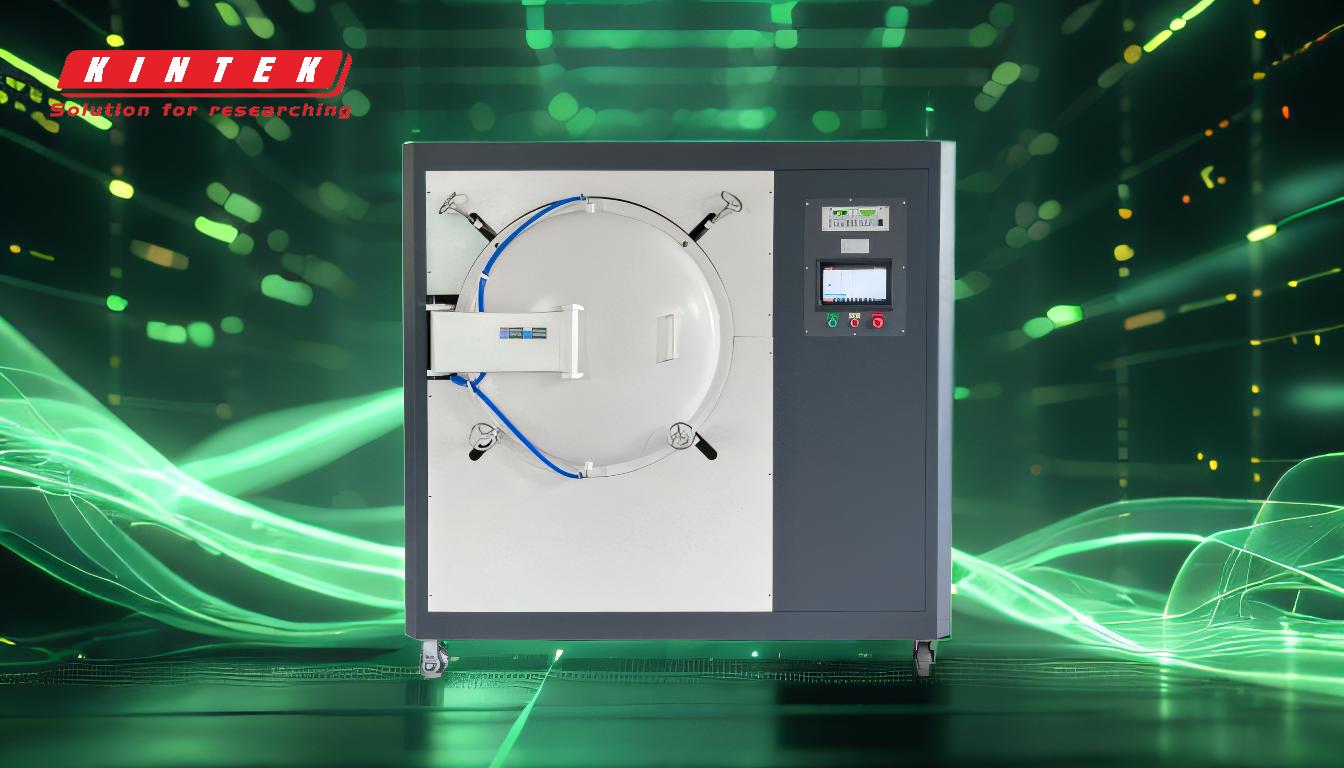
-
Roof:
- The roof of an electric arc furnace is a critical component, often made of heat-resistant materials like alumina and magnesite-chromite bricks to withstand high temperatures.
- It typically features three holes for electrode insertion, allowing the electrodes to reach the molten metal in the hearth.
- The roof retraction mechanism enables electrode removal and furnace charging, ensuring smooth operation and maintenance.
-
Hearth:
- The hearth is the lower part of the furnace where molten metal and slag are contained.
- It is often lined with refractory materials to endure extreme heat and chemical reactions.
- A tilting mechanism is integrated into the hearth, allowing the furnace to tilt and pour molten metal into molds or ladles.
-
Electrodes:
- Electrodes are essential for generating the electric arc that melts the metal. They are typically made of carbon or graphite due to their high conductivity and heat resistance.
- The electrodes penetrate through the roof and are directed toward the hearth, where the arc is formed.
- The electrode system may include a water-cooled shaft (stinger) to manage heat and extend the lifespan of the electrodes.
-
Side Walls:
- The side walls of the furnace are also lined with refractory materials to protect the furnace structure from the intense heat and chemical reactions occurring inside.
- These walls provide structural integrity and insulation, ensuring efficient heat retention and safe operation.
-
Tilting Mechanism:
- The tilting mechanism is a crucial feature for pouring molten metal. It allows the furnace to tilt forward or backward, facilitating the discharge of molten metal through a drain hole.
- This mechanism can be powered by electric or hydraulic drives, offering precision and control during the pouring process.
-
Cooling System:
- Cooling systems are vital for maintaining the temperature of critical components like the hearth and electrodes.
- Water-cooled copper hearths and electrode shafts are common, ensuring durability and preventing overheating.
- Efficient cooling systems enhance the longevity and performance of the furnace.
-
Fume Extraction System:
- Fume extraction systems are essential for operator safety, removing harmful gases and particulates generated during the melting process.
- These systems help maintain a safe working environment and comply with environmental regulations.
-
Power Supply System:
- The power supply system includes components like transformers and copper busbars, delivering the necessary electrical energy to the furnace.
- High current conductors (short nets) ensure efficient power transfer to the electrodes, enabling the generation of the electric arc.
-
Feeding and Discharging Systems:
- Feeding systems allow for the continuous or batch loading of raw materials into the furnace.
- Discharging systems facilitate the removal of molten metal and slag, ensuring smooth operation and minimizing downtime.
-
Dust Removal System:
- Dust removal systems are integrated to capture and remove particulate matter generated during the melting process.
- These systems contribute to cleaner operations and reduce environmental impact.
Understanding these components is essential for equipment purchasers, as it allows them to evaluate the suitability, efficiency, and safety features of different electric arc furnace models. Each component plays a vital role in the furnace's overall performance, and their quality and design can significantly impact operational outcomes.
Summary Table:
Component | Function | Key Features |
---|---|---|
Roof | Houses electrodes and withstands high temperatures | Made of alumina and magnesite-chromite bricks; retraction mechanism for charging |
Hearth | Contains molten metal and slag | Lined with refractory materials; integrated tilting mechanism |
Electrodes | Generate electric arc for melting | Made of carbon or graphite; water-cooled shafts for heat management |
Side Walls | Provide structural integrity and insulation | Lined with refractory materials for heat retention |
Tilting Mechanism | Facilitates pouring of molten metal | Powered by electric or hydraulic drives for precision |
Cooling System | Maintains temperature of critical components | Water-cooled copper hearths and electrode shafts |
Fume Extraction | Removes harmful gases and particulates | Ensures operator safety and environmental compliance |
Power Supply | Delivers electrical energy to the furnace | Includes transformers and high-current conductors |
Feeding Systems | Enables loading of raw materials | Supports continuous or batch loading |
Dust Removal | Captures and removes particulate matter | Reduces environmental impact and ensures cleaner operations |
Ready to choose the right electric arc furnace for your needs? Contact our experts today for personalized guidance!