Physical Vapor Deposition (PVD) coating is a sophisticated process used to deposit thin films of material onto a substrate, enhancing its properties such as wear resistance, hardness, and aesthetic appearance. The process involves heating a target material until it vaporizes, then depositing the vapor onto the substrate surface. Common materials used in PVD coatings include metals like titanium, chromium, tungsten, and aluminum, which are often combined with reactive gases such as nitrogen or hydrocarbons to form coatings like nitrides and carbonitrides. The PVD process is versatile, capable of incorporating a wide range of inorganic and some organic materials, making it suitable for various applications from durable-decorative coatings to high-performance aerospace components.
Key Points Explained:
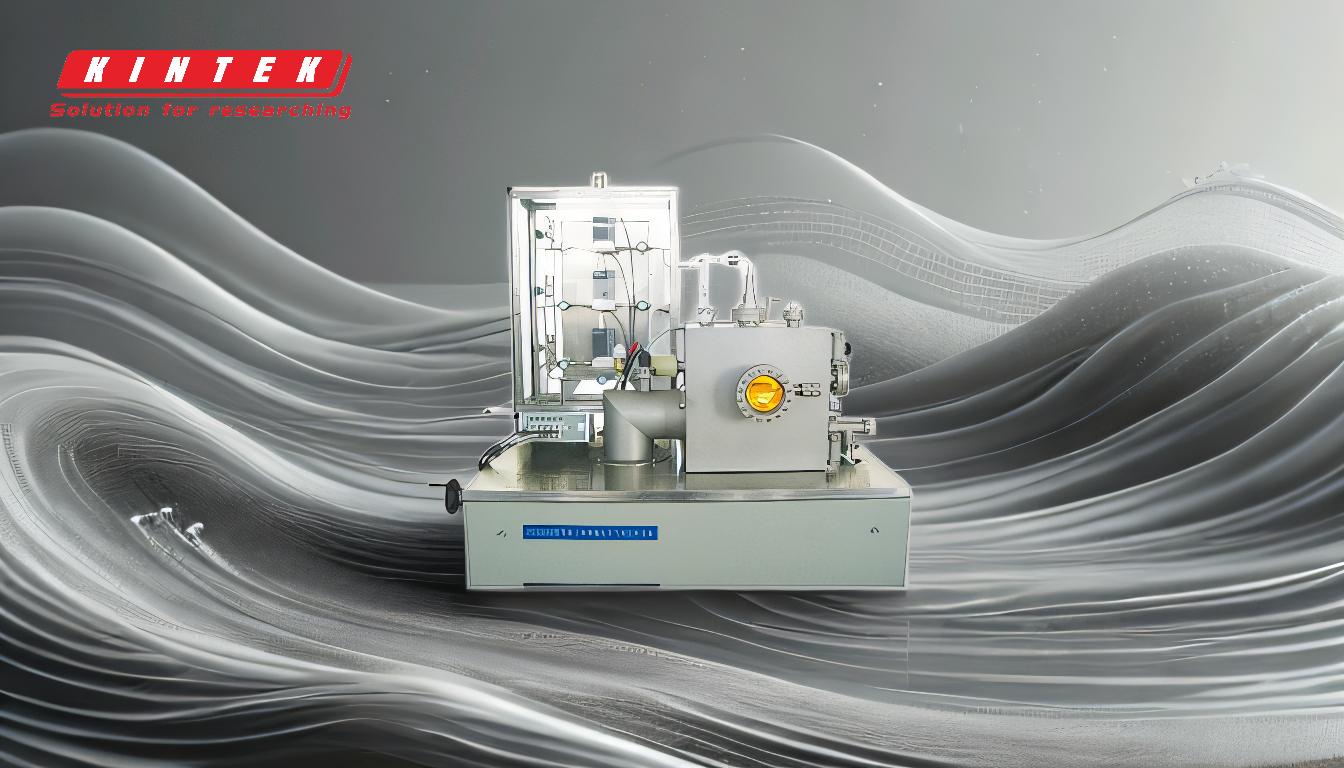
-
Target Materials in PVD Coating:
- Metals and Alloys: Common metals used in PVD coatings include titanium, chromium, tungsten, and aluminum. These metals are chosen for their specific properties, such as hardness, wear resistance, and ability to form strong bonds with reactive gases.
- Ceramics and Compounds: PVD can also deposit ceramics and compounds like carbides, nitrides, silicides, and borides. These materials are often used in specialized applications requiring high performance, such as aerospace and automotive components.
- Periodic Table Elements: The process can utilize a wide range of elements from the periodic table, allowing for the creation of unique coatings tailored to specific needs.
-
Reactive Gases:
- Nitrogen: Often used to form nitride coatings, which are known for their hardness and wear resistance. For example, titanium nitride (TiN) is a common PVD coating used in cutting tools.
- Hydrocarbon-Based Gases: These gases are used to create carbonitride coatings, which combine the properties of carbides and nitrides. They are particularly useful in applications requiring both hardness and low friction.
-
Substrate Materials:
- Base Materials: The substrate, or base material, can be made of various materials including metals, plastics, and ceramics. The choice of substrate depends on the intended application and the desired properties of the final product.
- Surface Preparation: Before the PVD process, the substrate often undergoes surface preparation such as cleaning and polishing to ensure proper adhesion of the coating.
-
PVD Coating Process:
- Vaporization: The target material is heated until it vaporizes. This can be achieved through methods like sputtering or evaporation.
- Deposition: The vaporized material is then deposited onto the substrate surface, forming a thin film. The thickness of the film can range from a few nanometers to a few micrometers.
- Uniformity: The PVD process is known for producing uniform coatings, which are essential for consistent performance and appearance.
-
Applications of PVD Coatings:
- Durable-Decorative Coatings: Used in products where both durability and aesthetic appearance are important, such as watches, jewelry, and consumer electronics.
- Performance Coatings: Applied to components that require enhanced mechanical properties, such as cutting tools, molds, and engine parts.
- Diamond-Like Carbon (DLC) Coatings: These coatings offer high hardness and low friction, making them ideal for applications in the automotive and aerospace industries.
- PVD Chrome Alternatives: Used as an environmentally friendly alternative to traditional chrome plating, offering similar aesthetic and protective properties.
-
Benefits of PVD Coating:
- Enhanced Properties: PVD coatings improve wear resistance, hardness, and corrosion resistance of the substrate.
- Aesthetic Appeal: The process can produce coatings with a variety of colors and finishes, enhancing the visual appeal of the product.
- Environmental Impact: PVD is considered an environmentally friendly process due to its minimal waste and lower energy consumption compared to traditional coating methods.
By understanding these key components and processes, one can appreciate the versatility and effectiveness of PVD coatings in various industrial applications.
Summary Table:
Component | Description |
---|---|
Target Materials | Metals (e.g., titanium, chromium), ceramics, and periodic table elements. |
Reactive Gases | Nitrogen, hydrocarbons (e.g., for nitride and carbonitride coatings). |
Substrate Materials | Metals, plastics, ceramics; requires surface preparation for adhesion. |
Process | Vaporization and deposition methods (e.g., sputtering, evaporation). |
Applications | Durable-decorative coatings, performance coatings, DLC, PVD chrome alternatives. |
Benefits | Enhanced wear resistance, hardness, corrosion resistance, and aesthetic appeal. |
Unlock the potential of PVD coatings for your applications—contact our experts today!