During the heat treatment of steel, several defects can occur due to improper control of heating, cooling, or environmental conditions. These defects include decarburization, oxidation, overheating, burning, warping, cracking, and residual stresses. Each defect arises from specific causes and can significantly impact the mechanical properties and structural integrity of the steel. Understanding these defects and their root causes is essential for implementing corrective measures and ensuring the quality of heat-treated steel components.
## Key Points Explained:
1. **Decarburization**:
- **Definition**: Loss of carbon from the surface layer of steel during heat treatment.
- **Causes**: Exposure to oxidizing atmospheres (e.g., air) at high temperatures.
- **Impact**: Reduces surface hardness and wear resistance, leading to weaker components.
- **Prevention**: Use of protective atmospheres (e.g., inert gases) or vacuum furnaces during heating.
2. **Oxidation**:
- **Definition**: Formation of oxide scales on the steel surface due to reaction with oxygen.
- **Causes**: Exposure to air or oxidizing environments at elevated temperatures.
- **Impact**: Leads to material loss, surface roughness, and dimensional inaccuracies.
- **Prevention**: Use of controlled atmospheres or protective coatings.
3. **Overheating**:
- **Definition**: Heating steel to excessively high temperatures, causing grain coarsening.
- **Causes**: Improper temperature control or excessive dwell times.
- **Impact**: Reduces toughness and ductility, making the steel brittle.
- **Prevention**: Strict adherence to recommended temperature ranges and heating times.
4. **Burning**:
- **Definition**: Severe overheating leading to partial melting or grain boundary oxidation.
- **Causes**: Extremely high temperatures or localized hot spots.
- **Impact**: Irreversible damage to the steel structure, rendering it unusable.
- **Prevention**: Avoidance of excessive temperatures and uniform heating practices.
5. **Warping**:
- **Definition**: Distortion or bending of steel components during heat treatment.
- **Causes**: Uneven heating or cooling, residual stresses, or improper fixturing.
- **Impact**: Compromises dimensional accuracy and fit of components.
- **Prevention**: Uniform heating and cooling rates, stress-relieving treatments, and proper fixturing.
6. **Cracking**:
- **Definition**: Formation of cracks due to thermal stresses or phase transformations.
- **Causes**: Rapid cooling (quenching), improper tempering, or high residual stresses.
- **Impact**: Leads to catastrophic failure under load.
- **Prevention**: Controlled cooling rates, proper tempering, and stress-relieving treatments.
7. **Residual Stresses**:
- **Definition**: Internal stresses remaining in the steel after heat treatment.
- **Causes**: Non-uniform cooling or phase transformations.
- **Impact**: Reduces fatigue strength and can lead to premature failure.
- **Prevention**: Stress-relieving treatments and controlled cooling processes.
By understanding these defects and their causes, manufacturers can implement appropriate measures to minimize their occurrence and ensure the production of high-quality heat-treated steel components.
Summary Table:
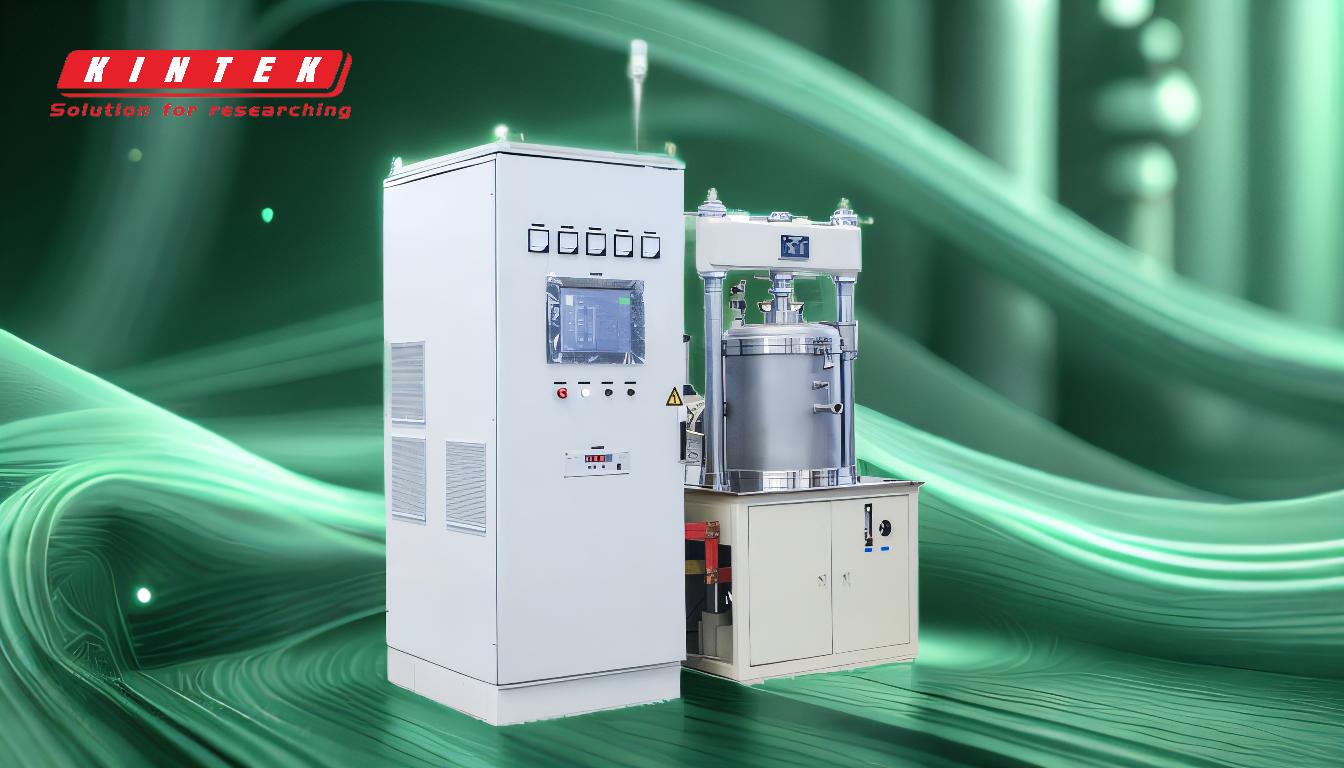
Defect | Causes | Impact | Prevention |
---|---|---|---|
Decarburization | Exposure to oxidizing atmospheres at high temperatures | Reduces surface hardness and wear resistance | Use protective atmospheres or vacuum furnaces |
Oxidation | Exposure to air or oxidizing environments at elevated temperatures | Material loss, surface roughness, dimensional inaccuracies | Use controlled atmospheres or protective coatings |
Overheating | Improper temperature control or excessive dwell times | Reduces toughness and ductility, making steel brittle | Adhere to recommended temperature ranges and heating times |
Burning | Extremely high temperatures or localized hot spots | Irreversible damage to steel structure | Avoid excessive temperatures and ensure uniform heating |
Warping | Uneven heating/cooling, residual stresses, improper fixturing | Distortion, compromising dimensional accuracy | Ensure uniform heating/cooling rates and proper fixturing |
Cracking | Rapid cooling, improper tempering, high residual stresses | Catastrophic failure under load | Control cooling rates, proper tempering, and stress-relieving treatments |
Residual Stresses | Non-uniform cooling or phase transformations | Reduces fatigue strength, leading to premature failure | Use stress-relieving treatments and controlled cooling processes |
Ensure your steel components meet the highest standards—contact our experts today for tailored solutions!