Annealing is a heat treatment process used to alter the physical and sometimes chemical properties of a material to increase its ductility and reduce its hardness, making it more workable. The process involves heating the material to a specific temperature, holding it there for a certain period, and then cooling it at a controlled rate. The different methods of annealing include full annealing, process annealing, stress relief annealing, and hydrogen annealing, each tailored to specific materials and desired outcomes. The process typically involves three stages: recovery, recrystallization, and grain growth, which occur as the material is heated to the appropriate temperature.
Key Points Explained:
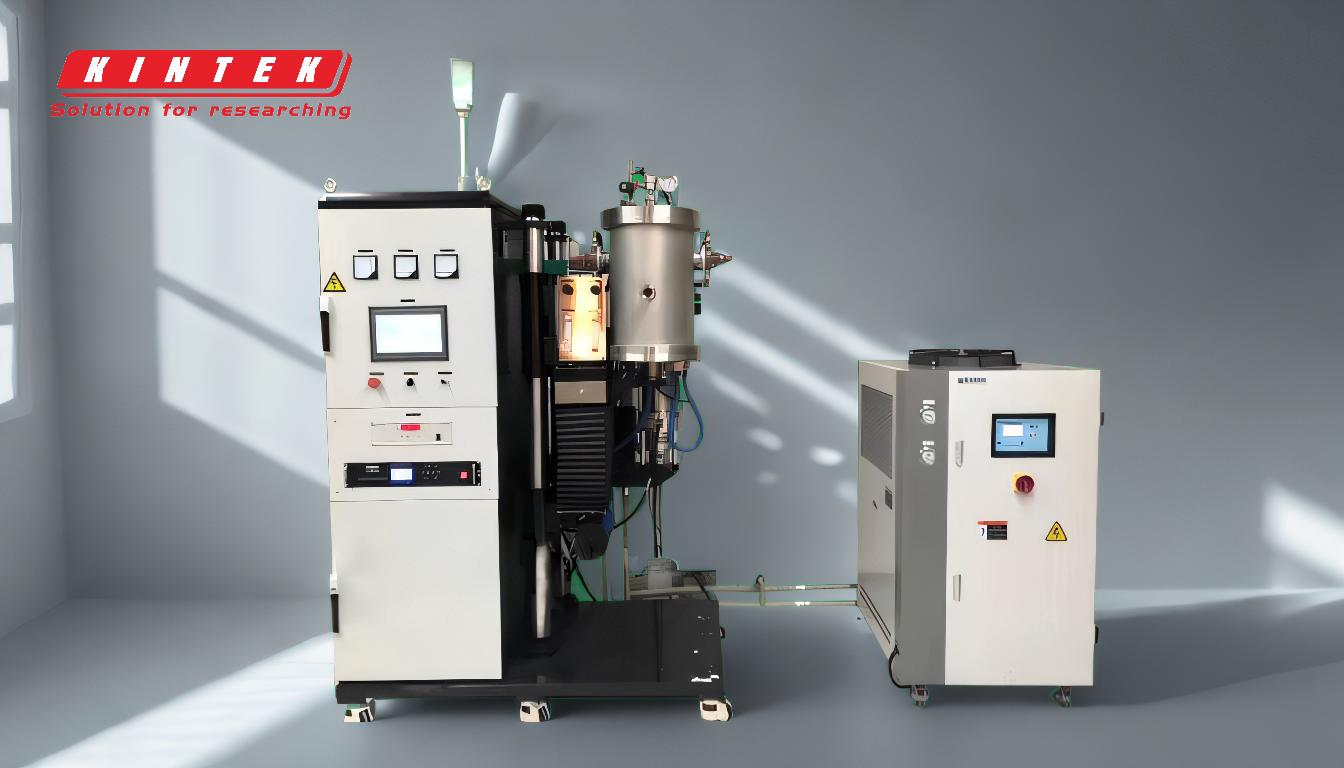
-
Stages of Annealing:
- Recovery: This is the first stage where the material is heated to a temperature that allows the internal stresses to be relieved without altering the microstructure significantly. The material regains some of its pre-deformation properties, such as reduced hardness and increased ductility.
- Recrystallization: In this stage, new strain-free grains nucleate and grow to replace the deformed grains. This occurs at a higher temperature than recovery and results in a significant reduction in hardness and an increase in ductility.
- Grain Growth: The final stage involves the growth of these new grains, which can lead to a coarser grain structure if the temperature is held too long. This stage is crucial for achieving the desired mechanical properties.
-
Types of Annealing Methods:
- Full Annealing: This method involves heating the material to a temperature above its upper critical temperature, holding it there to allow complete austenitization, and then cooling it slowly, usually in the furnace. This process results in a coarse pearlitic structure, which is soft and ductile.
- Process Annealing: Also known as intermediate annealing, this method is used to soften the material for further cold working. It is performed at temperatures below the lower critical temperature and is typically used for low-carbon steels.
- Stress Relief Annealing: This method is used to relieve internal stresses in a material without significantly altering its structure. It is performed at temperatures below the recrystallization temperature and is commonly used after welding or machining.
- Hydrogen Annealing: This specialized method uses a controlled atmosphere of 100% hydrogen to prevent oxidation and product discoloration. Hydrogen is a highly reducing gas, which promotes 'surface cleaning' of oxidized parts by reducing oxides on the wire. This process is often called 'bright annealing.' However, hydrogen may decarburize steel parts, so precautions are necessary. It is also the most expensive atmosphere, but lower-cost nitrogen-hydrogen blends can be effective alternatives.
-
Applications and Considerations:
- Material Compatibility: Different materials require different annealing methods. For example, full annealing is suitable for high-carbon steels, while process annealing is more appropriate for low-carbon steels.
- Atmosphere Control: In methods like hydrogen annealing, the atmosphere plays a crucial role in preventing oxidation and achieving the desired surface finish. The choice of atmosphere can also affect the cost and complexity of the process.
- Temperature and Time: The specific temperature and time parameters are critical for achieving the desired microstructure and mechanical properties. Overheating or holding the material at high temperatures for too long can lead to undesirable grain growth.
In summary, annealing is a versatile heat treatment process with various methods tailored to specific materials and desired outcomes. Understanding the stages of annealing and the different methods available is crucial for selecting the appropriate process for a given application.
Summary Table:
Annealing Method | Description | Best For |
---|---|---|
Full Annealing | Heats material above upper critical temperature, slow cooling for soft structure | High-carbon steels |
Process Annealing | Softens material for further cold working, below lower critical temperature | Low-carbon steels |
Stress Relief Annealing | Relieves internal stresses without altering structure | Post-welding or machining |
Hydrogen Annealing | Uses hydrogen atmosphere to prevent oxidation, ideal for surface cleaning | Bright annealing, oxidized parts |
Need help choosing the right annealing method for your materials? Contact our experts today for tailored advice!