Cold isostatic pressing (CIP) is a versatile powder compaction process used to produce high-integrity billets or preforms with minimal distortion or cracking. It is particularly useful for large, complex parts or materials that require uniform density. CIP is divided into two main types: wet bag and dry bag methods. The wet bag method involves removing and refilling the mold after each pressure cycle, making it ideal for large and intricate parts. The dry bag method, on the other hand, integrates the mold into the vessel, making it more suitable for simpler and smaller parts. Both methods utilize a liquid medium, such as an oil-water mixture, pressurized up to 100,000 psi to achieve uniform compaction. CIP is widely used in industries requiring wear-resistant tools, metal forming tools, and components that are too large for uniaxial pressing.
Key Points Explained:
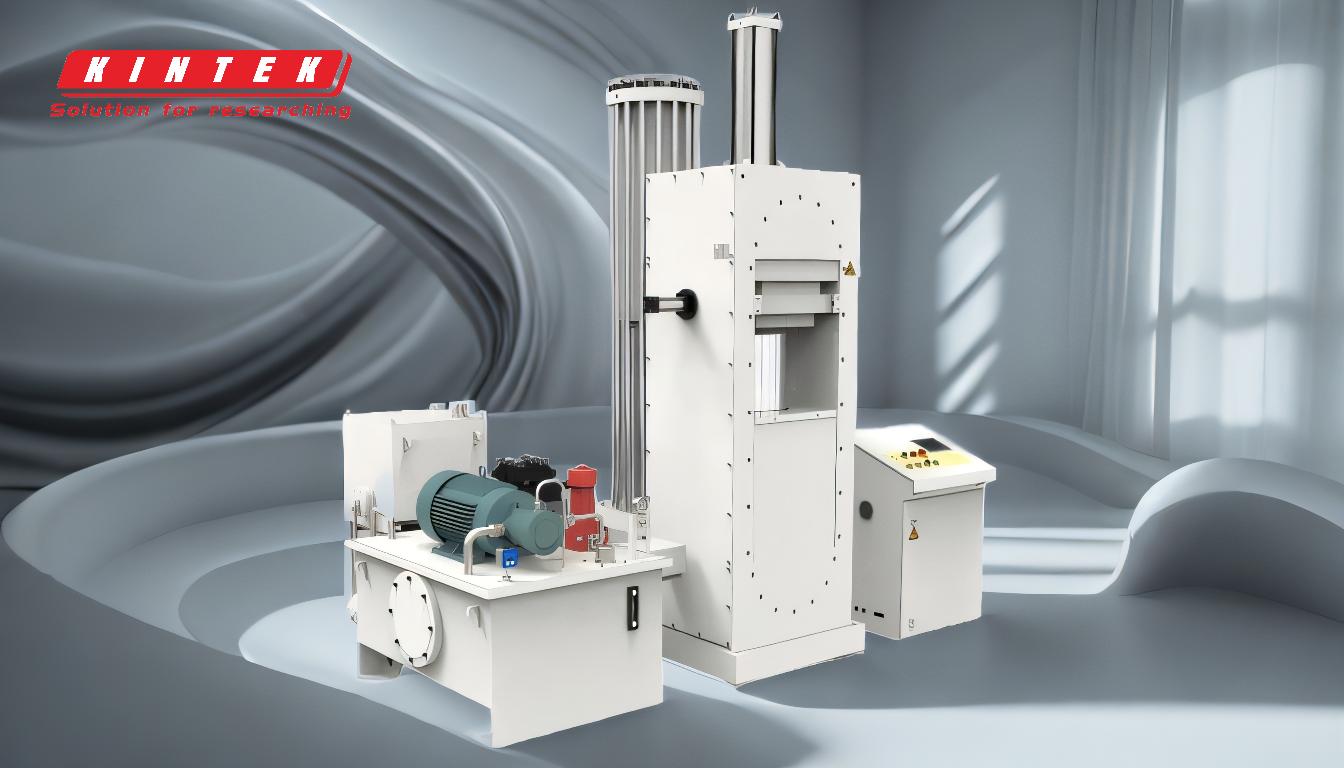
-
Definition and Purpose of Cold Isostatic Pressing (CIP):
- CIP is a powder compaction process performed at ambient temperatures to create uniform, high-density green parts.
- It is particularly useful for large, complex parts or materials that require uniform density and minimal distortion or cracking during firing.
- CIP is commonly used for wear-resistant tools, metal forming tools, and components that are too large for uniaxial pressing.
-
Types of Cold Isostatic Pressing:
- CIP is divided into two main types: wet bag and dry bag methods.
-
Wet Bag Method:
- The mold is removed and refilled after each pressure cycle.
- Suitable for large and complex parts due to its flexibility in handling various shapes and sizes.
- Commonly used in industries requiring intricate designs or large-scale production.
-
Dry Bag Method:
- The mold is an integral part of the pressing vessel.
- More efficient for simpler and smaller parts, as it eliminates the need for mold removal and refilling.
- Ideal for high-volume production of smaller components.
-
Wet Bag Method:
- CIP is divided into two main types: wet bag and dry bag methods.
-
Process Details:
- In CIP, the powder material is placed in a mold and subjected to uniform pressure from all sides using a liquid medium (often an oil-water mixture).
- The pressure in the CIP chamber can reach up to 100,000 psi, ensuring uniform compaction and density.
- The process is performed at ambient temperatures, distinguishing it from hot isostatic pressing (HIP), which operates at elevated temperatures.
-
Applications of Cold Isostatic Pressing:
- CIP is widely used in industries requiring high-integrity parts, such as aerospace, automotive, and tool manufacturing.
- It is ideal for producing wear-resistant tools, metal forming tools, and components that are too large or complex for uniaxial pressing.
- The process is also used for materials that do not require high precision in the sintered state but benefit from uniform density and minimal distortion.
-
Advantages of CIP:
- Produces parts with uniform density and minimal distortion or cracking.
- Suitable for large and complex parts that cannot be pressed using uniaxial methods.
- Versatile and adaptable to a wide range of materials and applications.
By understanding the differences between wet bag and dry bag methods, as well as the applications and advantages of CIP, equipment and consumable purchasers can make informed decisions about the most suitable method for their specific needs.
Summary Table:
Type | Description | Applications |
---|---|---|
Wet Bag | Mold is removed and refilled after each cycle; ideal for large, complex parts. | Large-scale production, intricate designs, aerospace, and automotive industries. |
Dry Bag | Mold is integrated into the vessel; suitable for simpler, smaller parts. | High-volume production of smaller components, tool manufacturing. |
Need help choosing the right cold isostatic pressing method? Contact our experts today!