Filter presses are essential equipment in various industries for solid-liquid separation processes. They come in different types, each designed to meet specific operational needs and applications. The primary types of filter presses include plate and frame filter presses, recessed plate filter presses, membrane filter presses, and automatic filter presses. Each type has unique features, advantages, and limitations, making them suitable for different scenarios. Understanding these types helps in selecting the right filter press for specific industrial requirements, ensuring efficient and cost-effective operations.
Key Points Explained:
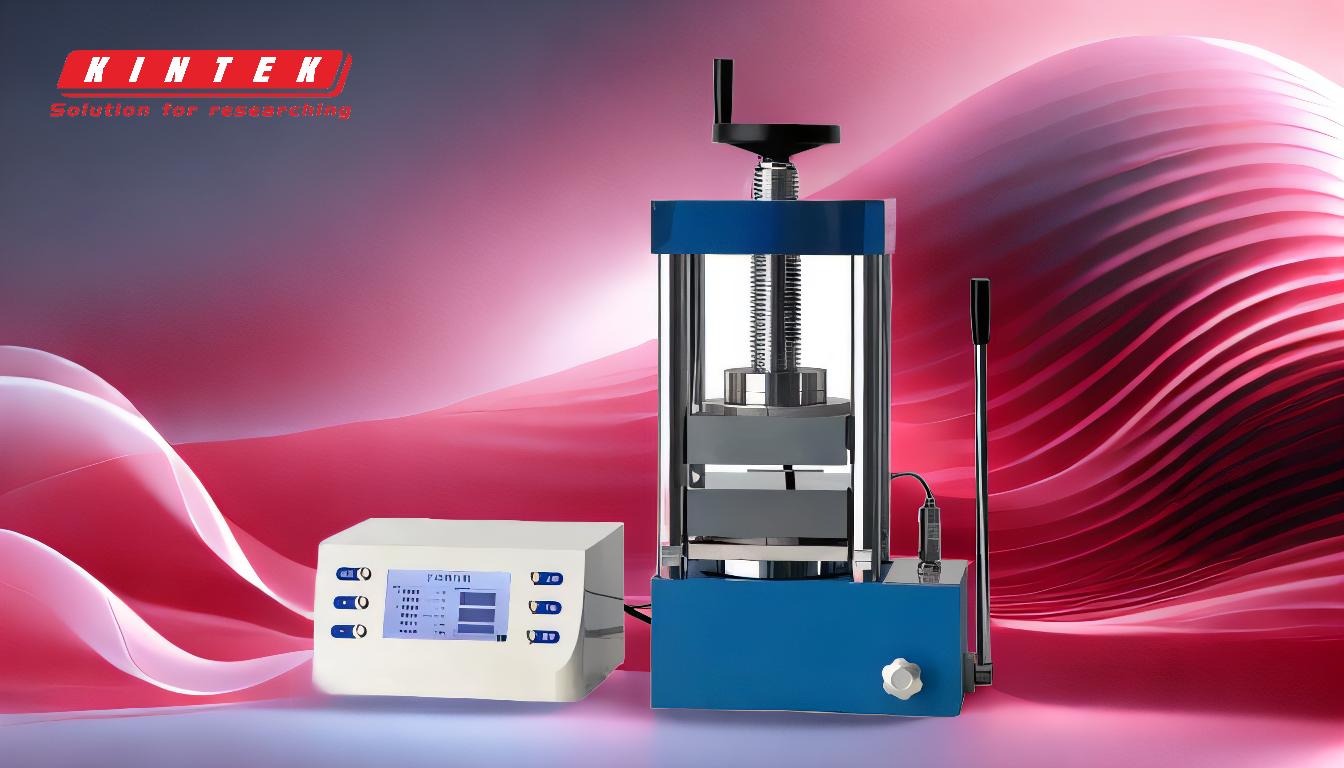
-
Plate and Frame Filter Press
- Structure: Consists of alternating plates and frames, with filter cloths placed between them.
- Operation: Slurry is pumped into the press, and solids are captured between the plates and frames while the filtrate passes through the cloth.
- Applications: Widely used in industries like chemical processing, food and beverage, and wastewater treatment.
- Advantages: Simple design, easy maintenance, and cost-effective for small to medium-scale operations.
- Limitations: Manual operation can be labor-intensive and time-consuming.
-
Recessed Plate Filter Press
- Structure: Similar to plate and frame presses but with recessed plates that create chambers for solids to accumulate.
- Operation: Slurry is pumped into the chambers, and solids are retained while the filtrate passes through the cloth.
- Applications: Suitable for applications requiring higher solids content, such as mining and metallurgy.
- Advantages: Higher capacity and better sealing compared to plate and frame presses.
- Limitations: Requires more robust construction, leading to higher costs.
-
Membrane Filter Press
- Structure: Features plates with flexible membranes that can be inflated to apply additional pressure.
- Operation: After the initial filtration, the membranes are inflated to squeeze out more liquid, resulting in drier filter cakes.
- Applications: Ideal for industries requiring high levels of dewatering, such as chemical and environmental sectors.
- Advantages: Produces drier cakes, reduces disposal costs, and improves efficiency.
- Limitations: Higher initial investment and maintenance costs.
-
Automatic Filter Press
- Structure: Equipped with automated mechanisms for plate shifting, cake discharge, and cloth washing.
- Operation: Reduces manual intervention, making the process faster and more consistent.
- Applications: Suitable for large-scale operations in industries like pharmaceuticals and food processing.
- Advantages: Increases productivity, reduces labor costs, and ensures consistent performance.
- Limitations: Higher initial cost and complexity in operation and maintenance.
By understanding the distinct features and applications of these filter press types, purchasers can make informed decisions based on their specific operational needs, ensuring optimal performance and cost-efficiency.
Summary Table:
Type | Structure | Applications | Advantages | Limitations |
---|---|---|---|---|
Plate and Frame Filter Press | Alternating plates and frames with filter cloths | Chemical processing, food and beverage, wastewater treatment | Simple design, easy maintenance, cost-effective | Manual operation can be labor-intensive and time-consuming |
Recessed Plate Filter Press | Recessed plates creating chambers for solids | Mining, metallurgy | Higher capacity, better sealing | Requires robust construction, higher costs |
Membrane Filter Press | Plates with flexible membranes for additional pressure | Chemical, environmental sectors (high dewatering needs) | Produces drier cakes, reduces disposal costs, improves efficiency | Higher initial investment and maintenance costs |
Automatic Filter Press | Automated mechanisms for plate shifting, cake discharge, and cloth washing | Pharmaceuticals, food processing (large-scale operations) | Increases productivity, reduces labor costs, ensures consistent performance | Higher initial cost, complexity in operation and maintenance |
Need help selecting the right filter press for your operations? Contact our experts today for personalized guidance!